Preparation method of metal type flux-cored wire and stainless steel bearing ring
A technology of flux-cored welding wire and bearing rings, applied in metal processing equipment, welding equipment, welding equipment, etc., can solve problems such as fatigue cracks, achieve the effects of improving strength and toughness, good process performance, and improving material utilization
- Summary
- Abstract
- Description
- Claims
- Application Information
AI Technical Summary
Problems solved by technology
Method used
Examples
preparation example Construction
[0030] The preparation method of stainless steel bearing ring, comprises the following steps:
[0031] Step 1. Weigh raw materials according to mass percentage: chromium powder 11-13%, nickel powder 4.5-5.5%, molybdenum powder 1.2-1.4%, vanadium iron powder 1.8-2.1%, niobium iron powder 1.8-2.2%, aluminum powder 1.1-1.3%, tungsten powder 2.4-2.6%, chromium nitride 3.6-4.5%, hafnium boride 0.08-0.12%, tantalum powder 0.05-0.065%, lanthanum oxide 0.48-0.52%, sodium fluoride 0.8-1%, The rest is iron powder, and the sum of the mass percentages of the above components is 100%;
[0032]Step 2. Mix the raw materials weighed in step 1, place them in a tube furnace, continuously feed argon gas, and keep warm at 200°C-300°C for 2h-3h to obtain the drug core powder;
[0033] Step 3. Place a stainless steel strip with a width of 7mm and a thickness of 0.3mm (the composition is shown in Table 1) on the strip feeding machine of the welding wire forming machine, and roll the stainless steel...
Embodiment 1
[0037] Step 1. Weigh 12% of chromium powder, 5% of nickel powder, 1.3% of molybdenum powder, 2.0% of vanadium iron powder, 2% of ferroniobium powder, 1.2% of aluminum powder, 2.4% of tungsten powder and 4% of chromium nitride according to mass percentage %, hafnium boride 0.1%, tantalum powder 0.05%, lanthanum oxide 0.5%, sodium fluoride 1%, the rest is iron powder, the sum of the mass percentages of the above components is 100%;
[0038] Step 2. Mix all the raw materials weighed in step 1 evenly and place them in a tube furnace. Under the condition of continuously feeding argon gas, keep the temperature at 200° C. for 2 hours to obtain the core powder;
[0039] Step 3. Place a stainless steel strip with a width of 7mm and a thickness of 0.3mm (the composition is shown in Table 1) on the strip feeding machine of the welding wire forming machine, and roll the stainless steel strip into a U-shaped groove through the pressing groove of the forming machine , the drug core powder i...
Embodiment 2
[0043] Step 1. Weigh 12% of chromium powder, 5% of nickel powder, 1.3% of molybdenum powder, 1.8% of vanadium-iron powder, 2% of niobium-iron powder, 1.2% of aluminum powder, 2.6% of tungsten powder and 4% of chromium nitride according to mass percentage. %, hafnium boride 0.1%, tantalum powder 0.065%, lanthanum oxide 0.5%, sodium fluoride 1%, the rest is iron powder, the sum of the mass percentages of the above components is 100%;
[0044] Step 2. Mix all the raw materials weighed in step 1 evenly, place them in a tube furnace, keep the temperature at 230° C. for 3 hours under the condition of continuously feeding argon gas, and obtain the drug core powder;
[0045] Step 3. Place a stainless steel strip with a width of 7mm and a thickness of 0.3mm (the composition is shown in Table 1) on the strip feeding machine of the welding wire forming machine, and roll the stainless steel strip into a U-shaped groove through the pressing groove of the forming machine , the drug core pow...
PUM
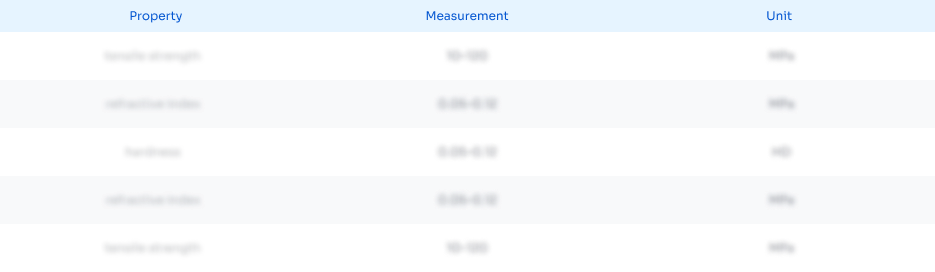
Abstract
Description
Claims
Application Information

- R&D
- Intellectual Property
- Life Sciences
- Materials
- Tech Scout
- Unparalleled Data Quality
- Higher Quality Content
- 60% Fewer Hallucinations
Browse by: Latest US Patents, China's latest patents, Technical Efficacy Thesaurus, Application Domain, Technology Topic, Popular Technical Reports.
© 2025 PatSnap. All rights reserved.Legal|Privacy policy|Modern Slavery Act Transparency Statement|Sitemap|About US| Contact US: help@patsnap.com