Efficient synthetic method of terephthalic polyester
A terephthalic acid and synthesis method technology, applied in the field of terephthalic acid-based polyester synthesis, can solve problems such as back-mixing and removal of small molecule by-products, reduce polycondensation time, reduce thermal decomposition side reactions, The effect of avoiding side effects
- Summary
- Abstract
- Description
- Claims
- Application Information
AI Technical Summary
Problems solved by technology
Method used
Image
Examples
Embodiment 1
[0036] Embodiment 1: prepare polyethylene terephthalate (PET)
[0037] Put 1800g of terephthalic acid and 706g of ethylene glycol (excess 5mol%) into the esterification reaction kettle, add 0.3g of zinc acetate, after nitrogen replacement, heat up to 200°C and start timing, control the pressure at 0.20-0.30MpaA, the stirring rate 50 rpm. After 2 hours of reaction, the liquid output was 176g. The reaction solution was transferred to the pre-condensation reaction kettle through a gear pump, and 0.3 g of antimony ethylene glycol was added at the same time. The temperature was controlled at 230 ° C, the pressure was 5-8 kPaA, and the stirring rate was 150 rpm. After 1 hour of reaction, the liquid output was 30.0 g. The reaction solution was transferred to the finishing polycondensation horizontal reactor through a gear pump, and 0.1 g of triethyl phosphite was added at the same time, the temperature was controlled at 260° C., the pressure was 100-300 Pa, and the average residence...
Embodiment 2
[0039] Embodiment 2: prepare polybutylene terephthalate (PBT)
[0040] Put 1,800g of terephthalic acid and 1,073g of 1,4-butanediol (10mol% in excess) into the esterification reaction kettle, add 0.4g of aluminum acetate, replace with nitrogen, raise the temperature to 230°C and start timing, and control the pressure at 0.20-0.30 MPaA, stirring rate 200rpm. After 2 hours of reaction, the liquid output was 176g. The reaction solution was transferred to the precondensation reaction kettle through a gear pump, and 0.4 g of butyl titanate was added at the same time. The temperature was controlled at 240 ° C, the pressure was 5-10 kPaA, and the stirring rate was 200 rpm. After 1 hour of reaction, the liquid output was 88.0 g. The reaction solution was transferred to the finishing packed tower through a gear pump, and 0.2 g of trimethyl phosphite was added at the same time, the temperature was controlled at 260° C., the pressure was 80-200 Pa, and the average residence time was 0.5...
Embodiment 3
[0042] Example 3: Preparation of polyethylene terephthalate-1,4-cyclohexanedimethanol copolyester (PETG)
[0043] Put 1800g of terephthalic acid, 538g of ethylene glycol, and 468g of 1,4-cyclohexanedimethanol (10mol% in excess of binary total amount) into the esterification reaction kettle, add 0.3g of magnesium acetate, and after nitrogen replacement, heat up to Start timing at 200°C, control the pressure at 0.20-0.30MPaA, and stir at 100rpm. After 2 hours of reaction, the liquid output was 176g. The reaction solution was transferred to the pre-condensation reaction kettle through a gear pump, and 0.3 g of antimony ethylene glycol was added at the same time. The temperature was controlled at 230 ° C, the pressure was 5-7 kPaA, and the stirring rate was 150 rpm. After 1 hour of reaction, the liquid output was 154.0 g. The reaction solution was transferred to the finishing polycondensation horizontal reaction kettle through a gear pump, and 0.1 g of tri-cresyl phosphite was ad...
PUM
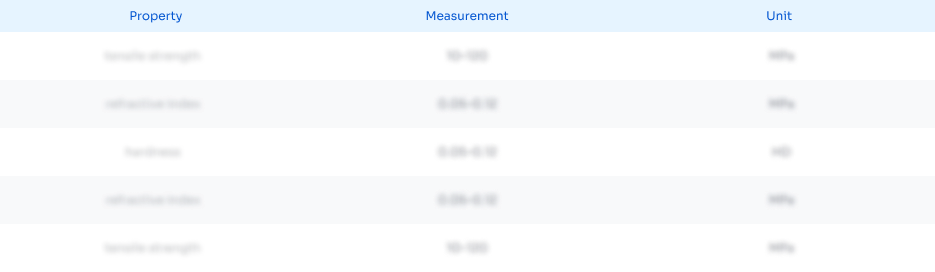
Abstract
Description
Claims
Application Information

- R&D
- Intellectual Property
- Life Sciences
- Materials
- Tech Scout
- Unparalleled Data Quality
- Higher Quality Content
- 60% Fewer Hallucinations
Browse by: Latest US Patents, China's latest patents, Technical Efficacy Thesaurus, Application Domain, Technology Topic, Popular Technical Reports.
© 2025 PatSnap. All rights reserved.Legal|Privacy policy|Modern Slavery Act Transparency Statement|Sitemap|About US| Contact US: help@patsnap.com