Method for preparing barium carbide and producing acetylene
A barium carbide and product technology, which is applied in the field of barium carbide and acetylene preparation, can solve the problems of high energy consumption and harsh synthesis conditions of coal-based acetylene carbide, and achieve the effects of simple process, reduced energy consumption and mild reaction conditions
- Summary
- Abstract
- Description
- Claims
- Application Information
AI Technical Summary
Problems solved by technology
Method used
Examples
Embodiment 1
[0029] Mix lumpy metallurgical coke (fixed carbon content of 85%) and barium carbonate (mass content of barium carbonate is greater than 98%) according to the molar ratio of carbon to barium of 4:1, and then process it into a powder mill with a particle size of 20 mesh or more The mixed powder with no more than 2% is sent into a microwave heating furnace with an air extraction system, and reacted at 1390-1420°C and a pressure of 0.01-0.02atm for 60 minutes to obtain barium carbide with a mass percentage of 82-85%. The product, the furnace gas is sent to the CO purification process after heat exchange and dedusting, and the barium carbide product is sent to the acetylene generator after heat exchange to react with water to generate acetylene.
Embodiment 2
[0031] Mix blue carbon (fixed carbon content of 87%) and barium carbonate (mass content of barium carbonate is greater than 98%) according to the carbon-barium molar ratio of 3.9:1 and then process it into a mixed powder with a particle size of 40-80 mesh. Send the powder into a microwave heating furnace with an air extraction system, and react in a hydrogen atmosphere at 1380-1410°C and a pressure of 0.015-0.02 atm for 60 minutes to obtain a product with a mass percentage of barium carbide of 89-93%. After heat exchange and cooling, the barium carbide product is sent to the acetylene generator to react with water to obtain acetylene, and the furnace gas is sent to the CO purification process after heat exchange and dust removal. By comparison of Example 1 and Example 2, it can be seen that the reaction in a hydrogen atmosphere can increase the content of barium carbide in the product.
Embodiment 3
[0033] Coal-based activated carbon (fixed carbon content is 99%) and barium hydroxide (mass content of barium hydroxide is greater than 97%) is made into a mixed powder with a particle size of 20-40 mesh according to the carbon-barium molar ratio of 3.9:1. Put the powder into an electric heating furnace, react at 1520°C, 0.015-0.02atm, and argon atmosphere for 180 minutes to obtain a product with a mass percentage of barium carbide of 86%. After heat exchange and cooling, the barium carbide product is sent to the acetylene generator to react with water to obtain acetylene, and the furnace gas is sent to the CO purification process after heat exchange and dust removal.
PUM
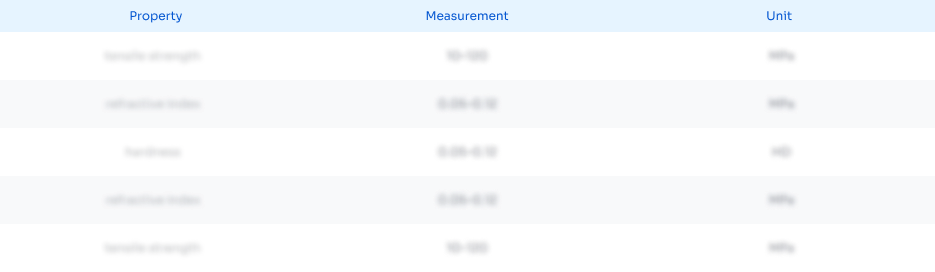
Abstract
Description
Claims
Application Information

- R&D
- Intellectual Property
- Life Sciences
- Materials
- Tech Scout
- Unparalleled Data Quality
- Higher Quality Content
- 60% Fewer Hallucinations
Browse by: Latest US Patents, China's latest patents, Technical Efficacy Thesaurus, Application Domain, Technology Topic, Popular Technical Reports.
© 2025 PatSnap. All rights reserved.Legal|Privacy policy|Modern Slavery Act Transparency Statement|Sitemap|About US| Contact US: help@patsnap.com