Method for co-producing X-type zeolite by mineralizing CO2 with blast furnace slag
A blast furnace slag and zeolite technology is applied in the field of using blast furnace slag to mineralize CO2 to co-produce X-type zeolite.
- Summary
- Abstract
- Description
- Claims
- Application Information
AI Technical Summary
Problems solved by technology
Method used
Image
Examples
Embodiment 1
[0025] (1) Evenly mix the blast furnace slag and ammonium sulfate which are finely ground to below 150 μm into the sulfuric acid solution, control the mass ratio of blast furnace slag and ammonium sulfate to 1:2, the concentration of sulfuric acid solution is 10wt%, and the mass ratio of sulfuric acid solution to solid material is 4:1; and the mixed material was magnetically stirred at 25°C for 60 minutes, and filtered to obtain sulfate leachate and hemihydrate gypsum leach residue;
[0026] (2) Slowly add ammonia water to the sulfate leach solution obtained in step 1, adjust the pH value to 6, control the temperature at 30° C., and obtain silica-alumina gel and magnesium sulfate mother liquor after filtering;
[0027] (3) Mix and dissolve aluminum hydroxide and sodium hydroxide in water, add an appropriate amount of sodium silicate, and control the molar ratio of silicon to aluminum to be 1:1 to obtain a directing agent;
[0028] (4) Add the directing agent obtained in step 3...
Embodiment 2
[0031] (1) Evenly mix blast furnace slag and ammonium sulfate finely ground to below 150 μm into sulfuric acid solution, control the mass ratio of blast furnace slag and ammonium sulfate to 1:3, the concentration of sulfuric acid solution is 20wt%, and the mass ratio of sulfuric acid to solid material is 3 : 1; and the mixed material was magnetically stirred at 40° C. for 50 min, filtered to obtain sulfate leachate, and hemihydrate gypsum leach slag;
[0032] (2) Slowly add ammonia water to the sulfate leach solution obtained in step 1, adjust the pH value to 6.5, control the temperature at 45° C., and obtain silica-alumina gel and magnesium sulfate mother liquor after filtering;
[0033] (3) Mix and dissolve aluminum hydroxide and sodium hydroxide in water, add an appropriate amount of sodium silicate, and control the molar ratio of silicon to aluminum to 2:1 to obtain a directing agent;
[0034] (4) Add the directing agent obtained in step 3 to the silica-alumina gel obtaine...
Embodiment 3
[0037] (1) Evenly mix blast furnace slag and ammonium sulfate finely ground to below 150 μm into sulfuric acid solution, control the mass ratio of blast furnace slag and ammonium sulfate to 1:4, the concentration of sulfuric acid solution is 30wt%, and the mass ratio of sulfuric acid to solid material is 1 : 1; and the mixed material was magnetically stirred at 55° C. for 35 min, filtered to obtain sulfate leachate, and hemihydrate gypsum leach slag;
[0038] (2) Slowly add ammonia water to the sulfate leach solution obtained in step 1, adjust the pH value to 7, control the temperature at 65° C., and obtain silica-alumina gel and magnesium sulfate mother liquor after filtering;
[0039] (3) Aluminum hydroxide and sodium hydroxide are mixed and dissolved in water, an appropriate amount of sodium silicate is added, and the silicon-aluminum molar ratio is controlled to be 3:1 to obtain a directing agent;
[0040] (4) Add the directing agent obtained in step 3 to the silica-alumin...
PUM
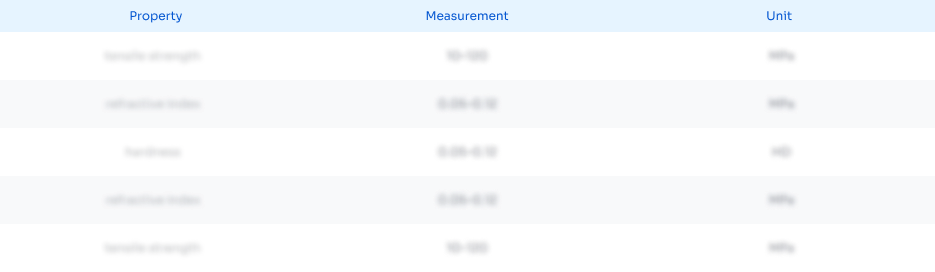
Abstract
Description
Claims
Application Information

- Generate Ideas
- Intellectual Property
- Life Sciences
- Materials
- Tech Scout
- Unparalleled Data Quality
- Higher Quality Content
- 60% Fewer Hallucinations
Browse by: Latest US Patents, China's latest patents, Technical Efficacy Thesaurus, Application Domain, Technology Topic, Popular Technical Reports.
© 2025 PatSnap. All rights reserved.Legal|Privacy policy|Modern Slavery Act Transparency Statement|Sitemap|About US| Contact US: help@patsnap.com