Preparation process of viscose-based carbon fiber composite material graphite felt and prepared graphite felt
A viscose-based carbon fiber and composite material technology, used in carbon fiber, fiber processing, textiles and papermaking, etc., can solve problems such as affecting the quality of monocrystalline silicon products, backward acupuncture and weaving processes, and inability to meet customers, and reduce equipment. The effect of maintenance frequency, reducing the volatilization of impurities and prolonging the production cycle
- Summary
- Abstract
- Description
- Claims
- Application Information
AI Technical Summary
Problems solved by technology
Method used
Examples
Embodiment 1
[0040] The preparation technology of viscose-based carbon fiber composite material graphite felt comprises the following steps:
[0041] Step 1: Material preparation, purchase viscose-based white felt from outside. The white felt is made of viscose fiber and needle-punched into felt. Different gram weights (generally the number of grams per square meter of fabric weight) make felts with different thermal insulation effects. , the grammage of viscose base white felt in the present embodiment is 1900g / m 2 , which was purchased from BWF Environtech (Wuxi) Co., Ltd.
[0042] Step 2: The above-mentioned viscose-based white felt is pre-oxidized to make carbon fiber pre-oxidized felt; the white felt is soaked in a soaking tank (85% diamine hydrogen phosphate solution diluted to 1% diamine hydrogen phosphate solution) for 2 hours, and then put into The drying machine dries the water vapor in the non-woven felt, and enters the pre-oxidation furnace for heating treatment. The heating t...
Embodiment 2
[0046] The preparation technology of viscose-based carbon fiber composite material graphite felt comprises the following steps:
[0047] Step 1: Material preparation, purchase viscose-based white felt from outside. The white felt is made of viscose fiber and needle-punched into felt. Different gram weights (generally the number of grams per square meter of fabric weight) make felts with different thermal insulation effects. , the grammage of viscose base white felt in the present embodiment is 2100g / m 2 , which was purchased from Defeng Environmental Protection Technology (Yangzhou) Co., Ltd.
[0048] Step 2: The above-mentioned viscose-based white felt is pre-oxidized to make carbon fiber pre-oxidized felt; the white felt is soaked in a soaking tank (85% diamine hydrogen phosphate solution diluted to 1% diamine hydrogen phosphate solution) for 2.5 hours, and then put into The drying machine dries the water vapor in the non-woven felt, and enters the pre-oxidation furnace for...
Embodiment 3
[0052] The preparation technology of viscose-based carbon fiber composite material graphite felt comprises the following steps:
[0053] Step 1: Material preparation, purchase viscose-based white felt from outside. The white felt is made of viscose fiber and needle-punched into felt. Different gram weights (generally the number of grams per square meter of fabric weight) make felts with different thermal insulation effects. , the grammage of viscose base white felt in the present embodiment is 2050g / m 2 , which was purchased from Yizheng Haifeng Industry and Trade Co., Ltd.
[0054] Step 2: The above-mentioned viscose-based white felt is pre-oxidized to make carbon fiber pre-oxidized felt; the white felt is soaked in a soaking tank (diluted with 85% diamine hydrogen phosphate solution into 1% diamine hydrogen phosphate solution) for 3 hours, and put into The drying machine dries the water vapor in the non-woven felt, and enters the pre-oxidation furnace for heating treatment....
PUM
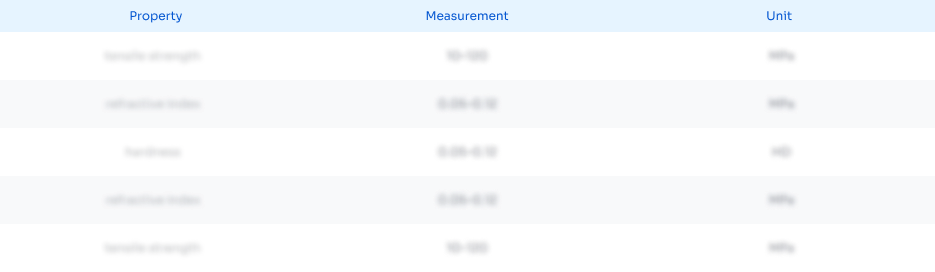
Abstract
Description
Claims
Application Information

- R&D
- Intellectual Property
- Life Sciences
- Materials
- Tech Scout
- Unparalleled Data Quality
- Higher Quality Content
- 60% Fewer Hallucinations
Browse by: Latest US Patents, China's latest patents, Technical Efficacy Thesaurus, Application Domain, Technology Topic, Popular Technical Reports.
© 2025 PatSnap. All rights reserved.Legal|Privacy policy|Modern Slavery Act Transparency Statement|Sitemap|About US| Contact US: help@patsnap.com