Method for preparing anti-cutting gloves from carbon fiber composite material
A composite material and carbon fiber technology, used in gloves, applications, protective clothing, etc., can solve the problems of uniform transmission, unfavorable fiber and resin infiltration, unfavorable stress, etc., to improve adhesion, improve reprocessing performance, and improve interface adhesion. The effect of junction performance
- Summary
- Abstract
- Description
- Claims
- Application Information
AI Technical Summary
Problems solved by technology
Method used
Image
Examples
Embodiment 1
[0032] (1) Disperse the carbon fibers in an acetone solution with a volume concentration of 50% for ultrasonic treatment. The ultrasonic treatment is carried out under the condition of condensation and reflux for 8 hours, the ultrasonic frequency is 20 kHz, the ultrasonic power is 1000 W, suction filtration, washing and drying.
[0033] (2) Place the carbon fiber after the impurity removal treatment in step (1) in a hydrogen peroxide solution with a mass concentration of 20% for oxidation treatment. The oxidation treatment time is 8 hours and the temperature is 80 ° C. Suction filtration, washing, drying, and oxidation treatment are obtained. carbon fiber.
[0034] (3) Disperse 10g of the carbon oxide fiber prepared in step (2) in N,N-dimethylformamide, then add 24.8g of 1,3-bis(3-aminopropyl)-1,1,3,3- Tetramethyldisiloxane and 16.6g of terephthalic acid were stirred and dissolved, and then 20g of 1-ethyl-(3-dimethylaminopropyl)carbodiimide hydrochloride and 14g of 1-hydroxybe...
Embodiment 2
[0037] (1) Disperse the carbon fibers in an acetone solution with a volume concentration of 60% for ultrasonic treatment. The ultrasonic treatment is carried out under the condition of condensation and reflux for 5 hours, the ultrasonic frequency is 20 kHz, the ultrasonic power is 500 W, suction filtration, washing and drying.
[0038] (2) Place the carbon fiber after the impurity removal treatment in step (1) in a hydrogen peroxide solution with a mass concentration of 30% for oxidation treatment. The oxidation treatment time is 5 hours and the temperature is 70°C. Suction filtration, washing, and drying obtain oxidation treatment. carbon fiber.
[0039] (3) Disperse 12g of carbon dioxide fibers prepared in step (2) in N,N-dimethylformamide, then add 28.5g of 1,3-bis(3-aminopropyl)-1,1,3,3- Tetramethyldisiloxane and 16.6g of terephthalic acid were stirred and dissolved, and then 20g of 1-ethyl-(3-dimethylaminopropyl)carbodiimide hydrochloride and 14g of 1-hydroxybenzodiimide ...
Embodiment 3
[0042] (1) Disperse the carbon fibers in an acetone solution with a volume concentration of 70% for ultrasonic treatment. The ultrasonic treatment is carried out under the condition of condensation and reflux for 3 hours, the ultrasonic frequency is 20 kHz, the ultrasonic power is 800 W, suction filtration, washing and drying.
[0043] (2) Place the carbon fiber after the impurity removal treatment in step (1) in a hydrogen peroxide solution with a mass concentration of 30% for oxidation treatment. The oxidation treatment time is 8 hours and the temperature is 80°C. Suction filtration, washing, and drying obtain oxidation treatment. carbon fiber.
[0044] (3) Disperse 15g of the carbon oxide fiber prepared in step (2) in N,N-dimethylformamide, then add 26.7g of 1,3-bis(3-aminopropyl)-1,1,3,3- Tetramethyldisiloxane and 16.6g of terephthalic acid were stirred and dissolved, then 20g of 1-ethyl-(3-dimethylaminopropyl)carbodiimide hydrochloride and 14g of 1-hydroxybenzodiimide wer...
PUM
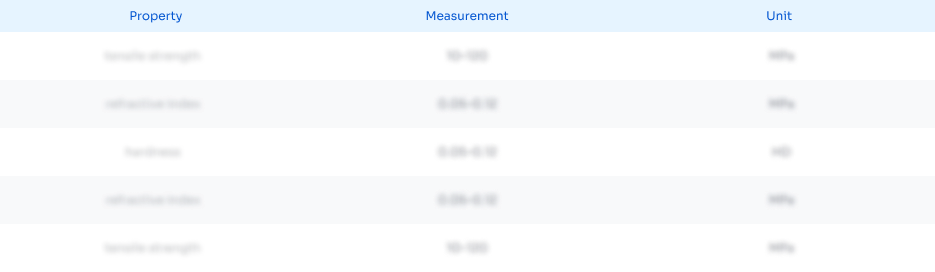
Abstract
Description
Claims
Application Information

- R&D Engineer
- R&D Manager
- IP Professional
- Industry Leading Data Capabilities
- Powerful AI technology
- Patent DNA Extraction
Browse by: Latest US Patents, China's latest patents, Technical Efficacy Thesaurus, Application Domain, Technology Topic, Popular Technical Reports.
© 2024 PatSnap. All rights reserved.Legal|Privacy policy|Modern Slavery Act Transparency Statement|Sitemap|About US| Contact US: help@patsnap.com