Friction material for motor vehicle
A technology for friction materials and motor vehicles, applied in friction linings, mechanical equipment, gear transmission mechanisms, etc., can solve the problems of unstable friction properties of friction materials, unreasonable preparation methods, lack of small temperature changes, etc., to improve quality and safety. The effect of high stability, strong quality stability and low production cost
- Summary
- Abstract
- Description
- Claims
- Application Information
AI Technical Summary
Problems solved by technology
Method used
Image
Examples
Embodiment 1
[0023] Concrete raw material is weighed by table 1, and step preparation step is as follows:
[0024] (1) Mix phenolic resin, calcium sulfate whiskers, graphite, aluminum fiber, dolomite, wollastonite, silica microspheres, and brass into the mixer for mixing according to the components, keep the temperature ≤ 60 ° C, and the speed of the mixer 1100rad / min, treatment 40min;
[0025] (2) Open the feeding port of the mixer, sequentially put nitrile rubber, aramid fiber, potassium tetratitanate whisker, potassium octatitanate whisker, keep the temperature ≤ 60 ℃, the mixer speed is 800rad / min, process for 20min, park and cool down to room temperature , to get the mixture;
[0026] (3) Add the mixture evenly into the mold cavity of the molding machine and hot press, wherein the upper mold temperature is 155°C, the lower mold temperature is 165°C, and the actual mold cavity temperature is 120±5°C to obtain a semi-finished product;
[0027] (4) Heat-treat the molded semi-finished p...
Embodiment 2
[0029] (1) Mix phenolic resin, calcium sulfate whiskers, graphite, aluminum fiber, dolomite, wollastonite, silica microspheres, and brass into the mixer for mixing according to the components, keep the temperature ≤ 60 ° C, and the speed of the mixer 1200rad / min, treatment 50min;
[0030] (2) Open the feeding port of the mixer, sequentially put the nitrile rubber, aramid fiber, potassium tetratitanate whisker, potassium octatitanate whisker, keep the temperature ≤ 60 ℃, the speed of the mixer is 1000rad / min, process for 30min, park and cool down to room temperature , to get the mixture;
[0031] (3) Add the mixture evenly into the mold cavity of the molding machine and hot press, wherein the upper mold temperature is 160°C, the lower mold temperature is 170°C, and the actual mold cavity temperature is 120±5°C to obtain a semi-finished product;
[0032] (4) Heat-treat the molded semi-finished product of (3) in an oven for 40 hours with hot air circulation and electric heating ...
Embodiment 3
[0034] (1) Mix phenolic resin, calcium sulfate whiskers, graphite, aluminum fiber, dolomite, wollastonite, silica microspheres, and brass into the mixer for mixing according to the components, keep the temperature ≤ 60°C, and the mixer speed 1100rad / min, treatment 50min;
[0035] (2) Open the feeding port of the mixer, sequentially put nitrile rubber, aramid fiber, potassium tetratitanate whisker, potassium octatitanate whisker, keep the temperature ≤ 60 ℃, the speed of the mixer is 1000rad / min, process for 20min, park and cool down to room temperature , to get the mixture;
[0036] (3) Add the mixture evenly into the mold cavity of the molding machine and hot press, wherein the upper mold temperature is 150°C, the lower mold temperature is 160°C, and the actual mold cavity temperature is 120±5°C to obtain a semi-finished product;
[0037] (4) Heat-treat the molded semi-finished product of (3) in an oven for 40 hours with hot air circulation and electric heating to obtain fin...
PUM
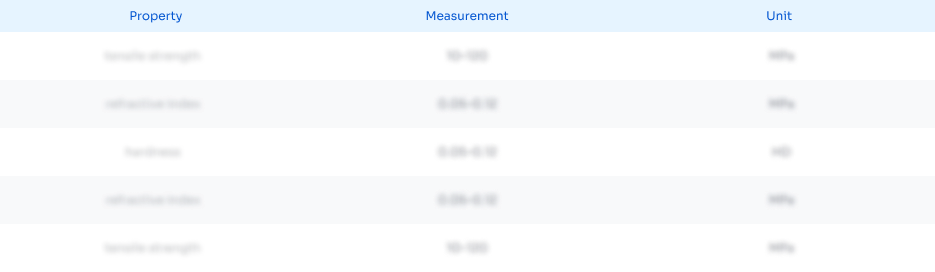
Abstract
Description
Claims
Application Information

- Generate Ideas
- Intellectual Property
- Life Sciences
- Materials
- Tech Scout
- Unparalleled Data Quality
- Higher Quality Content
- 60% Fewer Hallucinations
Browse by: Latest US Patents, China's latest patents, Technical Efficacy Thesaurus, Application Domain, Technology Topic, Popular Technical Reports.
© 2025 PatSnap. All rights reserved.Legal|Privacy policy|Modern Slavery Act Transparency Statement|Sitemap|About US| Contact US: help@patsnap.com