Non-quenching high-toughness cold-working die steel and production process
A technology with high strength and toughness and production process, applied in the field of metallurgical manufacturing, can solve the problems of easy generation of reticulated carbides, affect performance, and high manufacturing costs, and achieve significant economic benefits, low manufacturing costs, and reasonable ratios.
- Summary
- Abstract
- Description
- Claims
- Application Information
AI Technical Summary
Problems solved by technology
Method used
Examples
Embodiment 1
[0045] Embodiment one is used for cold shearing blade
[0046] 9CrSi is a commonly used cold working die steel. The cold shear blade made of this steel, the original mold processing process is: smelting→forging→spheroidizing annealing→rough turning→finishing→quenching and tempering→grinding→aging→fine grinding . The final heat treatment is heating and quenching at 870°C and tempering at 200°C. Cold shear blades often fail early due to crushing, chipping or peeling off during use, and their service life is short. Change it to non-quenched high-strength toughness cold work die steel. After forging, it will be normalized at 900°C, and after tempering at 300°C, its hardness will be 3-5HRC higher than the conventional one, but the fracture toughness will be K IC Improve nearly 20%. The application on the 600t bar shearing machine shows that the normalized and low-temperature tempered blade cuts scrap steel 15467t / pair on average, and the conventional annealing blade cuts scrap st...
Embodiment 2
[0081] Embodiment two is used for cold extrusion die
[0082] The spinning die of a factory is made of Cr12MoV. The processing flow of the original mold is: smelting→forging→spheroidizing annealing→rough turning→finishing→quenching and tempering→grinding→aging→fine grinding. The hardness of the mold is HRC52-55, and the life span is only a few hundred pieces, all of which fail due to brittle cracking. Switch to non-quenched high-strength toughness cold work die steel after forging and normalizing at 850°C, and after tempering at 250°C at low temperature, its hardness is 3-5HRC higher than that of Cr12MoV, but the fracture toughness is K IC The toughness of the mold is increased by nearly 20%, and the final hardness of the mold is HRC, which further reduces its brittleness. The life of the mold is increased to more than 2,000 rolling pieces, reaching the level of imported molds. The specific material composition and manufacturing process parameters are as follows:
[0083] 1...
PUM
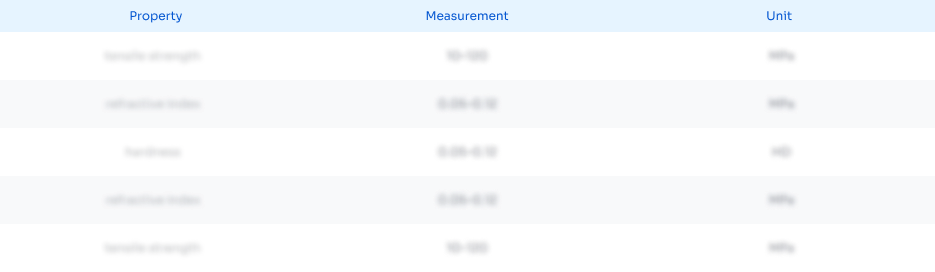
Abstract
Description
Claims
Application Information

- R&D
- Intellectual Property
- Life Sciences
- Materials
- Tech Scout
- Unparalleled Data Quality
- Higher Quality Content
- 60% Fewer Hallucinations
Browse by: Latest US Patents, China's latest patents, Technical Efficacy Thesaurus, Application Domain, Technology Topic, Popular Technical Reports.
© 2025 PatSnap. All rights reserved.Legal|Privacy policy|Modern Slavery Act Transparency Statement|Sitemap|About US| Contact US: help@patsnap.com