Powder injection molding process
A powder injection molding and injection molding technology, applied in the field of powder injection molding materials, can solve problems such as human health, production safety and environmental protection, volatile, high toxicity, etc., to improve the production environment and production safety, The effect of high safety and slight toxicity
- Summary
- Abstract
- Description
- Claims
- Application Information
AI Technical Summary
Problems solved by technology
Method used
Image
Examples
Embodiment example 1
[0030] Feed: powder injection molding wax-based zirconia feed formula is as follows:
[0031]
[0032]
[0033] Zirconia powder, polyethylene, polystyrene, and isopropyl titanate triisostearate are added to the banburying tank, the temperature of the banburying tank is raised to 185°C, and the speed of the banburying tank is 15r / min for 0.5h; the temperature of the banburying tank is lowered to At 165°C, add stearic acid, paraffin wax, and carnauba wax, continue stirring for 1 hour, and then extrude and granulate.
[0034] Injection molding: Conventional injection process.
[0035]Solvent extraction and degreasing: degreasing with limonene + dipentene mixed solution (mass ratio 1:1), solvent temperature 60°C, degreasing time: 12h. Sintering: Thermal degreasing process, heating up to 600°C in 4 hours, holding at 600°C for 4 hours. Sintering process: 1500℃ / 6h air sintering.
Embodiment example 2
[0037] Feeding: powder injection molding wax-based 95W5Ni feeding formula is as follows:
[0038]
[0039]
[0040] 95W5Ni alloy powder, polyethylene, polypropylene, and isopropyl titanate triisostearate are added to the banburying tank, the temperature of the banburying tank is raised to 190°C, and the speed of the banburying tank is 18r / min for 0.5h; the temperature of the banburying tank is lowered to 170°C °C, add stearic acid, paraffin wax, and microcrystalline wax, continue stirring for 1 hour, and then extrude and granulate. Injection molding: Conventional injection process.
[0041] Solvent extraction degreasing: degreasing with terpineol, solvent temperature 70°C, degreasing time: 12h. Sintering: Thermal degreasing process, heating up to 600°C in 5 hours, and holding at 600°C for 4 hours. Sintering process: 1450℃ / 8h hydrogen sintering.
Embodiment example 3
[0043] Feed: powder injection molding wax-based 17-4 stainless steel feed formula is as follows:
[0044]
[0045] 17-4 stainless steel alloy powder, polyethylene, polypropylene, ethylene-vinyl acetate copolymer, and isopropyl titanate triisostearate are added to the banburying tank, the temperature of the banburying tank is raised to 180°C, and the speed is 20r / min for banburying 0.5h; lower the temperature of the banbury tank to 160°C, add zinc stearate and microcrystalline wax, continue stirring for 0.5h, and then extrude and granulate. Injection molding: Conventional injection process.
[0046] Solvent extraction degreasing: degreasing with limonene, solvent temperature 70°C, degreasing time: 8h. Sintering: Thermal degreasing process, heating up to 600°C in 4 hours, holding at 600°C for 2 hours. Sintering process: 1310℃ / 4h vacuum sintering.
PUM
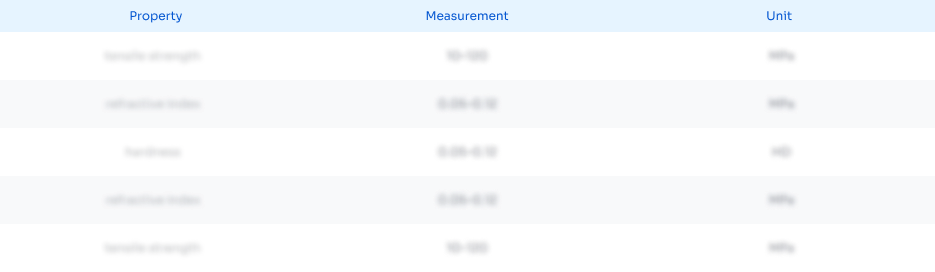
Abstract
Description
Claims
Application Information

- Generate Ideas
- Intellectual Property
- Life Sciences
- Materials
- Tech Scout
- Unparalleled Data Quality
- Higher Quality Content
- 60% Fewer Hallucinations
Browse by: Latest US Patents, China's latest patents, Technical Efficacy Thesaurus, Application Domain, Technology Topic, Popular Technical Reports.
© 2025 PatSnap. All rights reserved.Legal|Privacy policy|Modern Slavery Act Transparency Statement|Sitemap|About US| Contact US: help@patsnap.com