Microwave dielectric ceramic by low-temperature co-fired ceramics
A technology of low-temperature co-fired ceramics and microwave dielectric ceramics, which is applied in the field of manufacturing microwave dielectric ceramics, and can solve problems such as large changes in sintered density, uneven powder dispersion, and reduction
- Summary
- Abstract
- Description
- Claims
- Application Information
AI Technical Summary
Problems solved by technology
Method used
Image
Examples
Embodiment -1
[0025] when (1-x)Ba 5 Nb 4 o 15 -xBaNb 2 o 6 When the ceramic material is equal to 30, mix 0wt%-15wt% BaO-B 2 o 3 -SiO 2 When the glass material is sintered at 890°C, it can be found that when 0wt% glass is added, the sintering is not dense, and the dielectric constant cannot be increased due to the large number of pores in the ceramic, only reaching 25.4. In addition, if 1wt%-15wt% BaO -B 2 o 3 -SiO 2 After glass, the density increases, and the dielectric constant is between 29.5-30.4. In addition, the quality factor also increases to 10,284 and 16,136GHz due to the increase in density. The temperature capacitance coefficient is -36 to -43ppm / ℃, and the temperature frequency The coefficient is 19 to 21ppm / ℃, and the insulation resistance reaches 2.5×10 11 to 9.4×10 11 Ω.
Embodiment -2
[0027] when (1-x)Ba 5 Nb 4 o 15 -xBaNb 2 o 6 When the ceramic material is equal to 50, mix 0wt%-15wt% BaO-B 2 o 3 -SiO 2 When the glass material is sintered at 890°C, it can be found that when 0wt% glass is added, the sintering is not dense, and the dielectric constant value cannot be increased to 17.3 due to the large number of pores in the ceramic. In addition, if 1wt%-15wt% of BaO-B is added 2 o 3 -SiO 2 After glass, the density increases, the dielectric constant is between 19.6-20.2, the quality factor is also due to the increase in density, and the quality factor increases to 11,765 and 15,766GHz, the temperature capacitance coefficient is -2 to 2ppm / ℃, and the temperature frequency coefficient is -1 to 1ppm / ℃, insulation resistance up to 3.3×10 11 to 6.7×10 11 Ω.
Embodiment -3
[0029] when (1-x)Ba 5 Nb 4 o 15 -xBaNb 2 o 6 When the ceramic material is equal to 70, mix 0wt%-15wt% BaO-B 2 o 3 -SiO 2 When the glass material is sintered at 890°C, it can be found that when 0wt% glass is added, the sintering is not dense, and the dielectric constant value cannot be increased to 11.3 due to the large number of pores in the ceramic. In addition, if 1wt%-15wt% of BaO-B is added 2 o 3 -SiO 2 After glass, the density increases, the dielectric constant is between 13.8-16.2, the quality factor is also due to the increase in density, and the quality factor increases to 12,478 and 19,753GHz, the temperature capacitance coefficient is 32 to 36ppm / ℃, and the temperature frequency coefficient is - 16 to -18ppm / ℃, insulation resistance up to 1.3×10 11 to 3.6×10 11 Ω.
PUM
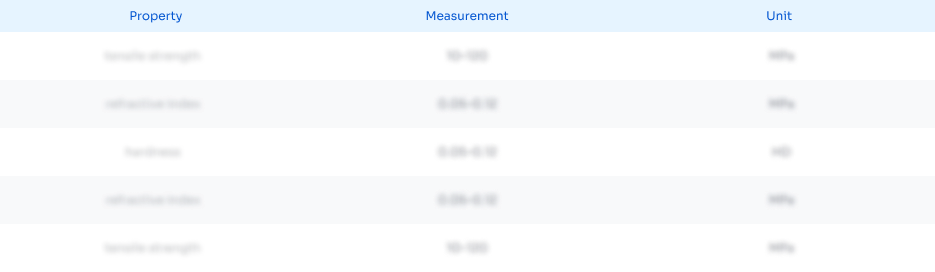
Abstract
Description
Claims
Application Information

- Generate Ideas
- Intellectual Property
- Life Sciences
- Materials
- Tech Scout
- Unparalleled Data Quality
- Higher Quality Content
- 60% Fewer Hallucinations
Browse by: Latest US Patents, China's latest patents, Technical Efficacy Thesaurus, Application Domain, Technology Topic, Popular Technical Reports.
© 2025 PatSnap. All rights reserved.Legal|Privacy policy|Modern Slavery Act Transparency Statement|Sitemap|About US| Contact US: help@patsnap.com