Annealing process for Al-Mg-Er alloy with medium and high Mg content
An annealing process and alloy technology, applied in manufacturing tools, heat treatment equipment, furnaces, etc., can solve the problems affecting the internal dislocation density and recrystallization degree of the alloy, poor corrosion resistance, etc., so as to improve the recrystallization temperature and improve the corrosion resistance. properties and toughness, improved mechanical properties and thermal stability
- Summary
- Abstract
- Description
- Claims
- Application Information
AI Technical Summary
Problems solved by technology
Method used
Image
Examples
Embodiment 1
[0011] Example 1 (i.e. comparative example):
[0012] The erbium-containing aluminum alloy (alloy composition mass percentage: Mg, 4.66%, Mn, 0.82%, Er 0.21%, Zr0.13%, the balance is Al) ingot was kept at 280 ° C for 15 h, and then heated to 470 ° C for 30 h Double-stage homogenization heat treatment was performed, and the ingot was hot-rolled to obtain an 8mm hot-rolled sheet with a total deformation of 97%. The obtained hot-rolled sheet was tested for mechanical properties at room temperature and low temperature. The test results are shown in Table 1.
[0013] Table 1 Tensile properties of hot-rolled alloys at different temperatures
[0014]
Embodiment 2
[0016] The hot-rolled sheet obtained in Example 1 was subjected to an annealing process at 350° C. for different times, and its mechanical properties were tested at room temperature and low temperature, respectively. The test results are shown in Table 2.
[0017] Table 2 Tensile properties of hot-rolled alloys at different temperatures after annealing
[0018]
[0019] It can be seen from Table 2 that no matter in the room temperature or low temperature test environment, after the annealing process at 350 °C, with the prolongation of the annealing time, the tensile strength and yield strength of the alloy show a downward trend, and the elongation increases significantly. And the change trend at room temperature and low temperature is the same, the annealed alloy with higher strength at room temperature is still higher than other states at low temperature. The low temperature elongation of the hot rolled sheet after annealing at 350℃ for 8h is the highest, reaching 35%.
...
Embodiment 3
[0024] The two state alloys in Example 1 and Example 2 were selected in the same area to observe the EBSD structure, and the grains were measured along the thickness of the plate. The average grain widths of the alloys in the two states were 2.56um and 2.55um, respectively. After annealing, the grains did not Significant growth occurred. The difference in orientation and the degree of recrystallization of the alloys in the two states were counted, and the results are shown in Tables 4 and 5.
[0025] Table 4 The ratio of grain boundary orientation difference between hot-rolled state and annealed state
[0026]
[0027] Table 5 Recrystallization degree of hot rolled and annealed state
[0028]
[0029] It can be seen from Table 4 and Table 5 that after annealing, the proportion of high-angle grain boundaries increases, the deformed structure decreases, and the proportion of subgrain and recrystallization increases. That is, subgrain, which corresponds to the decrease in...
PUM
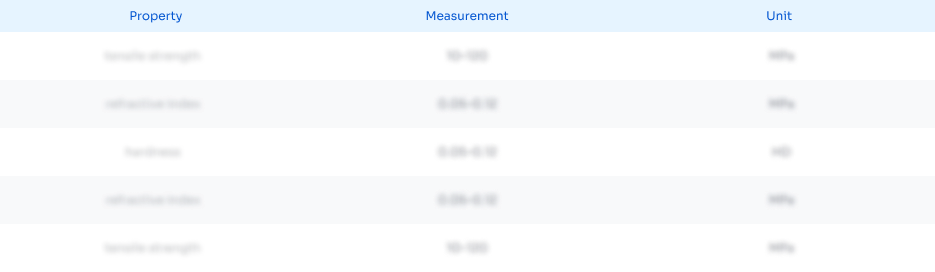
Abstract
Description
Claims
Application Information

- R&D Engineer
- R&D Manager
- IP Professional
- Industry Leading Data Capabilities
- Powerful AI technology
- Patent DNA Extraction
Browse by: Latest US Patents, China's latest patents, Technical Efficacy Thesaurus, Application Domain, Technology Topic, Popular Technical Reports.
© 2024 PatSnap. All rights reserved.Legal|Privacy policy|Modern Slavery Act Transparency Statement|Sitemap|About US| Contact US: help@patsnap.com