Preparation process of wear-resistant elbow material
A preparation process and pipe bending technology, which is applied in the field of preparation process of wear-resistant bend pipe materials, can solve the problems of poor wear resistance and easy-to-adhesive materials, and achieve improved wear resistance, reduced material adhesion, and wear-resistant bends. The effect of tube material lifting
- Summary
- Abstract
- Description
- Claims
- Application Information
AI Technical Summary
Problems solved by technology
Method used
Examples
Embodiment 1
[0020] The invention provides a technical solution: a wear-resistant elbow material. The formula of the wear-resistant elbow material includes the following components: 3.3% carbon, 2.8% silicon, 0.5% manganese, 1.0% chromium, 0.03% phosphorus, sulfur 0.02%, magnesium 0.03%, cerium 0.02%, vanadium 0.3%, neodymium 1.0%, alumina 4%, titanium diboride 6%, and the rest is iron.
[0021] A preparation process for a wear-resistant elbow material as described above, the preparation method comprises the following steps:
[0022] Step 1: Weighing quantitatively, weighing all the raw materials according to the above components;
[0023] Step 2: Raw material smelting. The raw materials configured in step 1 are smelted in an intermediate frequency induction furnace. When the melting temperature of molten iron reaches 1500°C, the iron is tapped into the spheroidizing treatment bag;
[0024] Step 3: Nodularization treatment and inoculation treatment, weighing 1.2% rare earth magnesium sili...
Embodiment 2
[0030] The invention provides a technical solution: a wear-resistant elbow material, the formula of which includes the following components: carbon 3.7%, silicon 2.3%, manganese 1.0%, chromium 0.4%, phosphorus 0.06%, sulfur 0.01%, magnesium 0.05%, cerium 0.01%, vanadium 1.0%, neodymium 0.3%, alumina 6%, titanium diboride 3%, and the rest is iron.
[0031] A preparation process for a wear-resistant elbow material as described above, the preparation method comprises the following steps:
[0032] Step 1: Weighing quantitatively, weighing all the raw materials according to the above components;
[0033] Step 2: Raw material smelting. The raw material prepared in step 1 is smelted in an intermediate frequency induction furnace. When the melting temperature of the molten iron reaches 1550°C, the iron is tapped into the spheroidizing treatment bag;
[0034] Step 3: Spheroidization treatment and inoculation treatment, weighing 1.6% rare earth magnesium silicon ferrosilicon nodulizer ...
Embodiment 3
[0040] The invention provides a technical solution: a wear-resistant elbow material, the formula of which includes the following components: 3.4% carbon, 2.4% silicon, 0.7% manganese, 0.6% chromium, 0.04% phosphorus, sulfur 0.01%, magnesium 0.04%, cerium 0.01%, vanadium 0.5%, neodymium 0.6%, alumina 5%, titanium diboride 4%, and the rest is iron.
[0041] A preparation process for a wear-resistant elbow material as described above, the preparation method comprises the following steps:
[0042] Step 1: Weighing quantitatively, weighing all the raw materials according to the above components;
[0043] Step 2: Raw material smelting. The raw materials configured in step 1 are smelted in an intermediate frequency induction furnace. When the melting temperature of molten iron reaches 1520°C, the iron is tapped into the spheroidizing treatment bag;
[0044] Step 3: Spheroidization treatment and inoculation treatment, weighing 1.4% rare earth magnesium silicon ferrosilicon nodulizer ...
PUM
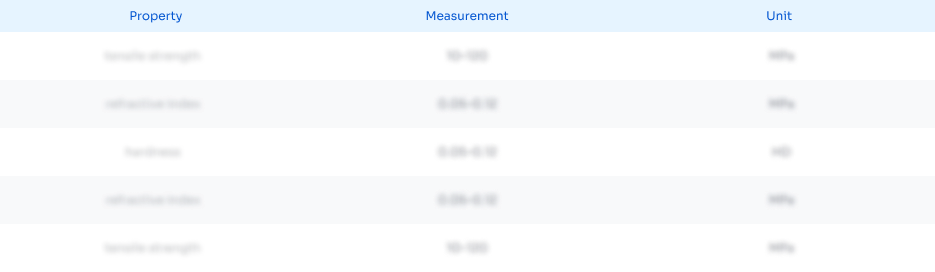
Abstract
Description
Claims
Application Information

- R&D
- Intellectual Property
- Life Sciences
- Materials
- Tech Scout
- Unparalleled Data Quality
- Higher Quality Content
- 60% Fewer Hallucinations
Browse by: Latest US Patents, China's latest patents, Technical Efficacy Thesaurus, Application Domain, Technology Topic, Popular Technical Reports.
© 2025 PatSnap. All rights reserved.Legal|Privacy policy|Modern Slavery Act Transparency Statement|Sitemap|About US| Contact US: help@patsnap.com