Wet process ceramic slurry of multi-layer chip ceramic dielectric capacitor and preparation method thereof
A multi-layer chip, wet process technology, applied in the direction of laminated capacitors, capacitors, fixed capacitors, etc., can solve the problems of easy delamination of products, high cost of process equipment, narrow product series, etc. The risk of delamination and cracking, the improvement of shrinkage matching, the effect of less organic solvent content
- Summary
- Abstract
- Description
- Claims
- Application Information
AI Technical Summary
Problems solved by technology
Method used
Image
Examples
Embodiment 1
[0020] 1. The composition of the porcelain paste of the multilayer chip ceramic capacitor is calculated by weight percentage: porcelain powder 85%, organic additive 1.5%, and organic solvent 13.5%.
[0021] Further, the organic additive is composed of a dispersant and a binding agent in a mass ratio of 3:2; wherein the dispersant is formed by mixing phosphoric acid ester and ethyl cellulose A type in a mass ratio of 6:4; The binder is made by mixing ethyl cellulose type B, ethyl cellulose type C, ethyl cellulose type D, and polyvinyl butyral in a mass ratio of 1:1:1:4.
[0022] Further, the organic solvent is composed of solvent type A and solvent type B with a mass ratio of 1:1; wherein, solvent type A is formed by mixing terpinolene and eucalyptol with a mass ratio of 1:5 ; Solvent type B is formed by mixing terpinolene and α-terpineol with a mass ratio of 1:6.
[0023] 2. The preparation method of the porcelain slurry of the multilayer chip ceramic capacitor, comprising th...
Embodiment 2
[0032] 1. The composition of the porcelain paste of the multilayer chip ceramic capacitor is calculated by weight percentage: porcelain powder 80%, organic additive 2%, and organic solvent 18%.
[0033] Further, the organic additive is composed of a dispersant and a binding agent in a mass ratio of 3:2; wherein the dispersant is formed by mixing phosphoric acid ester and ethyl cellulose A type in a mass ratio of 6:4; The binder is made by mixing ethyl cellulose type B, ethyl cellulose type C, ethyl cellulose type D, and polyvinyl butyral in a mass ratio of 1:1:1:4.
[0034] Further, the organic solvent is composed of solvent type A and solvent type B with a mass ratio of 1:1; wherein, solvent type A is formed by mixing terpinolene and eucalyptol with a mass ratio of 1:5 ; Solvent type B is formed by mixing terpinolene and α-terpineol with a mass ratio of 1:6.
[0035] 2. The preparation method of the porcelain slurry of the multilayer chip ceramic capacitor, comprising the fo...
Embodiment 3
[0043] 1. The composition of the porcelain paste of the multilayer chip ceramic capacitor is calculated by weight percentage: porcelain powder 77%, organic additive 7%, and organic solvent 16%.
[0044]Further, the organic additive is composed of a dispersant and a binding agent with a mass ratio of 2:1; wherein, the dispersant is formed by mixing phosphoric acid ester and ethyl cellulose A type with a mass ratio of 4:3; The binder is made by mixing ethyl cellulose type B, ethyl cellulose type C, ethyl cellulose type D, and polyvinyl butyral in a mass ratio of 1:1:1:3.
[0045] Further, the organic solvent is formed by mixing alcohol and toluene in a mass ratio of 1:1, and both alcohol and toluene are electronic grade.
[0046] 2. The preparation method of the porcelain slurry of the multilayer chip ceramic capacitor, comprising the following steps:
[0047] (1) Pre-dispersion: Add organic solvent, dispersant and porcelain powder into the mixing tank, and stir for 35 minutes ...
PUM
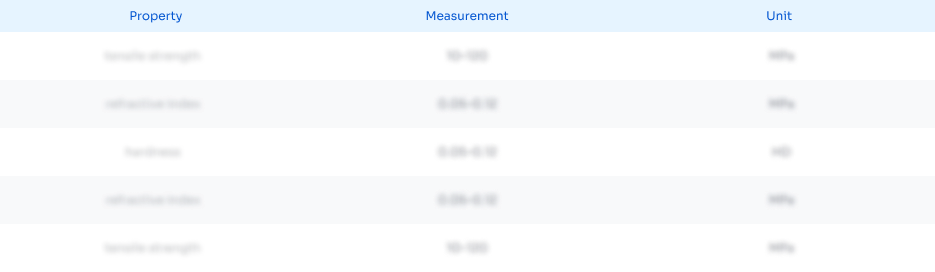
Abstract
Description
Claims
Application Information

- R&D
- Intellectual Property
- Life Sciences
- Materials
- Tech Scout
- Unparalleled Data Quality
- Higher Quality Content
- 60% Fewer Hallucinations
Browse by: Latest US Patents, China's latest patents, Technical Efficacy Thesaurus, Application Domain, Technology Topic, Popular Technical Reports.
© 2025 PatSnap. All rights reserved.Legal|Privacy policy|Modern Slavery Act Transparency Statement|Sitemap|About US| Contact US: help@patsnap.com