Magnesium alloy and surface treatment method thereof
A surface treatment and surface pretreatment technology, which is applied in metal material coating process, liquid chemical plating, superimposed layer plating, etc., can solve problems such as difficult industrialization, complex activation methods, and unstable processes, and achieve High success rate, wide application range and good stability
- Summary
- Abstract
- Description
- Claims
- Application Information
AI Technical Summary
Problems solved by technology
Method used
Image
Examples
Embodiment 1
[0046] Polishing: Polish the VW93 rare earth magnesium alloy sample with a polishing machine and wash it with water;
[0047] Degreasing and degreasing treatment: at room temperature, wash with acetone solvent (organic solvent) for 10 minutes under the action of ultrasonic waves. The organic solvent may have release agent, polishing paste and other grease in the parts to be treated (magnesium alloy) for degreasing and degreasing cleaning;
[0048] Alkaline washing to remove ester: use lye solution containing 50g / L sodium hydroxide and 10g / L sodium phosphate dodecahydrate, and wash with alkali for 10 minutes at a temperature of 60°C. Alkaline washing is a further degreasing treatment with alkaline solution;
[0049] Pickling, derusting and etching: acid solution of 30mL / L nitric acid, pickling at room temperature for 1min, using acidic solution (pickling solution) to remove the passivation film and intermetallic segregation compounds on the surface of the magnesium alloy, so as ...
Embodiment 2
[0057] The electroless nickel plating process after the electro-oxidation passivation of the magnesium alloy is the same as in Example 1, the only difference being that the activation time is changed to 1 min. The obtained nickel coating properties are listed in Table 1.
Embodiment 3
[0059] The electroless nickel plating process after the electro-oxidation passivation of the magnesium alloy is the same as in Example 1, the only difference being that the activation time is changed to 5 minutes. The obtained nickel coating properties are listed in Table 1.
PUM
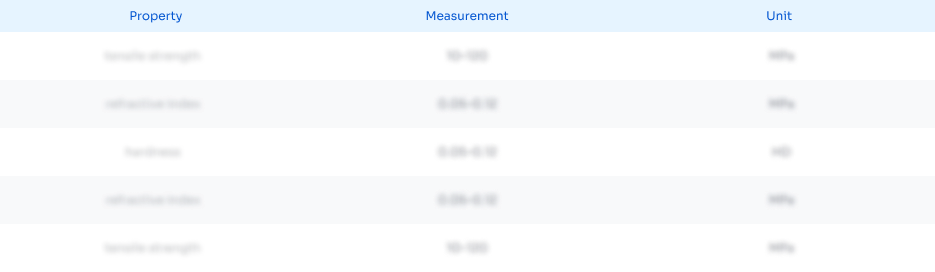
Abstract
Description
Claims
Application Information

- Generate Ideas
- Intellectual Property
- Life Sciences
- Materials
- Tech Scout
- Unparalleled Data Quality
- Higher Quality Content
- 60% Fewer Hallucinations
Browse by: Latest US Patents, China's latest patents, Technical Efficacy Thesaurus, Application Domain, Technology Topic, Popular Technical Reports.
© 2025 PatSnap. All rights reserved.Legal|Privacy policy|Modern Slavery Act Transparency Statement|Sitemap|About US| Contact US: help@patsnap.com