HDPE pipe and preparation method thereof
A pipe and pipe blank technology, which is applied in the field of HDPE pipe and its preparation, can solve the problems such as the difficulty of taking into account various indicators of mechanical strength, achieve good market prospects, improve flexibility, and make up for market vacancies
- Summary
- Abstract
- Description
- Claims
- Application Information
AI Technical Summary
Problems solved by technology
Method used
Image
Examples
Embodiment 1
[0030] A preparation method of HDPE pipes, first put HDPE resin in a polymer pipe rotary extrusion device for melt and rotary extrusion, and the extruded pipe blanks are cooled and sized under traction to obtain the HDPE pipe ; Wherein, in parts by weight, HDPE resin is prepared by the following method:
[0031] (1) First add 1 part of catalyst, 5 parts of n-hexane and 1 part of n-heptane into the polymerization kettle, and raise the temperature of the polymerization kettle to 60°C;
[0032] (2) Then feed 0.1 part of vinyl fluoride, 0.8 part of 1-octene, 1 part of hydrogen and 100 parts of ethylene, react at 83°C and 0.5MPa for 3 hours, cool down to normal temperature, discharge, and dry to obtain a resin matrix;
[0033] (3) Finally, the resin matrix and the filler are melt-blended to obtain HDPE resin;
[0034] The catalyst is obtained by mixing vanadium-modified SBA-15 molecular sieve with titanium tetrachloride and butyl titanate; the filler is obtained by grafting graphe...
Embodiment 2
[0047] A preparation method of HDPE pipes, first put HDPE resin in a polymer pipe rotary extrusion device for melt and rotary extrusion, and the extruded pipe blanks are cooled and sized under traction to obtain the HDPE pipe ; Wherein, in parts by weight, HDPE resin is prepared by the following method:
[0048] (1) First add 2 parts of catalyst, 3 parts of n-hexane and 2 parts of n-heptane into the polymerization kettle, and raise the temperature of the polymerization kettle to 50°C;
[0049] (2) Then feed 0.2 parts of vinyl fluoride, 0.5 parts of 1-octene, 2 parts of hydrogen and 100 parts of ethylene, react at 80°C and 0.8MPa for 2 hours, cool down to normal temperature, discharge, and dry to obtain a resin matrix;
[0050] (3) Finally, the resin matrix and the filler are melt-blended to obtain HDPE resin;
[0051] The catalyst is obtained by mixing vanadium-modified SBA-15 molecular sieve with titanium tetrachloride and butyl titanate; the filler is obtained by grafting g...
Embodiment 3
[0064] A preparation method of HDPE pipes, first put HDPE resin in a polymer pipe rotary extrusion device for melt and rotary extrusion, and the extruded pipe blanks are cooled and sized under traction to obtain the HDPE pipe ; Wherein, in parts by weight, HDPE resin is prepared by the following method:
[0065] (1) First add 1.5 parts of catalyst, 4 parts of n-hexane and 1.5 parts of n-heptane into the polymerization kettle, and raise the temperature of the polymerization kettle to 55°C;
[0066] (2) Then feed 0.15 parts of vinyl fluoride, 0.6 parts of 1-octene, 1.5 parts of hydrogen and 100 parts of ethylene, react at 82°C and 0.7 MPa for 2.5 hours, cool down to normal temperature, discharge, and dry to obtain a resin matrix;
[0067] (3) Finally, the resin matrix and the filler are melt-blended to obtain HDPE resin;
[0068] The catalyst is obtained by mixing vanadium-modified SBA-15 molecular sieve with titanium tetrachloride and butyl titanate; the filler is obtained by ...
PUM
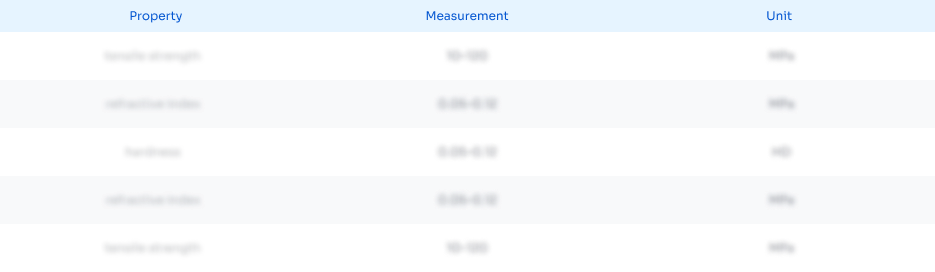
Abstract
Description
Claims
Application Information

- R&D
- Intellectual Property
- Life Sciences
- Materials
- Tech Scout
- Unparalleled Data Quality
- Higher Quality Content
- 60% Fewer Hallucinations
Browse by: Latest US Patents, China's latest patents, Technical Efficacy Thesaurus, Application Domain, Technology Topic, Popular Technical Reports.
© 2025 PatSnap. All rights reserved.Legal|Privacy policy|Modern Slavery Act Transparency Statement|Sitemap|About US| Contact US: help@patsnap.com