Copper-based friction material suitable for carbon ceramic brake disc and preparation method thereof
A technology of carbon-ceramic brake discs and friction materials, applied in the field of friction materials, to achieve the effects of improving high-temperature strength and toughness, improving friction and wear performance, and good thermal conductivity
- Summary
- Abstract
- Description
- Claims
- Application Information
AI Technical Summary
Problems solved by technology
Method used
Image
Examples
Embodiment 1
[0033] Step 1: the mass fraction is: copper powder 56%, iron powder 14%, molybdenum disulfide powder 3%, granular graphite powder 6%, flake graphite powder 4%, ferrochrome powder (chromium content is 55wt%) 3%, 3% of ferrosilicon powder, 4% of ferroboron powder, 4% of ferromanganese powder (manganese content is 75wt%), 3% of ferrosilicon powder raw material powder is prepared in proportion to the mixture, and the mixture is mixed in V-type mixer for 8h ;
[0034] Step 2: Pressing and molding the mixture to obtain a compact, and the unit pressing pressure is 500MPa;
[0035] Step 3: Put the green compact on the copper-plated steel back, place it in a bell-type pressurized sintering furnace for sintering, the sintering temperature is 960°C, the holding time is 3h, the sintering unit pressure is 2MPa, and the sintering atmosphere is pure hydrogen;
[0036] Step 4: After the heat preservation is over, remove the heating furnace body, add a cooling cover, and keep applying a unit ...
Embodiment 2
[0038] Step 1: the mass fraction is: copper powder 52%, iron powder 18%, molybdenum disulfide powder 3%, granular graphite powder 6%, flake graphite powder 4%, ferrochrome powder (chromium content is 55wt%) 2%, 3% of ferrosilicon powder, 6% of ferroboron powder, 5% of ferromanganese powder (manganese content is 65wt%), 1% of ferrosilicon powder raw material powder is prepared in proportion to the mixture, and the mixture is mixed in V-shaped mixer for 6h ;
[0039] Step 2: Pressing and molding the mixture to obtain a compact, the unit pressing pressure is 400MPa;
[0040] Step 3: Put the green compact on the copper-plated steel back, place it in a bell-type pressurized sintering furnace for sintering, the sintering temperature is 1020°C, the holding time is 2h, the sintering unit pressure is 2MPa, and the sintering atmosphere is hydrogen and nitrogen Mixed gas with a ratio of 3:1;
[0041] Step 4: After the heat preservation is over, remove the heating furnace body, add a co...
Embodiment 3
[0043] Step 1: the mass fraction is: copper powder 55%, iron powder 15%, molybdenum disulfide powder 2%, granular graphite powder 5%, flake graphite powder 5%, ferrochrome powder (chromium content is 65wt%) 4%, 4% of ferrosilicon powder, 3% of ferroboron powder, 4% of ferromanganese powder (manganese content is 65wt%), 3% of ferrosilicon powder raw material powder is prepared in proportion to the mixture, and the mixture is mixed in V-shaped mixer for 4h ;
[0044] Step 2: Pressing and molding the mixture to obtain a compact, and the unit pressing pressure is 500MPa;
[0045] Step 3: Put the green compact on the copper-plated steel back, place it in a bell-type pressurized sintering furnace for sintering, the sintering temperature is 980°C, the holding time is 3h, the sintering unit pressure is 3MPa, and the sintering atmosphere is hydrogen and nitrogen Mixed gas with a ratio of 3:1;
[0046] Step 4: After the heat preservation is over, remove the heating furnace body, add a...
PUM
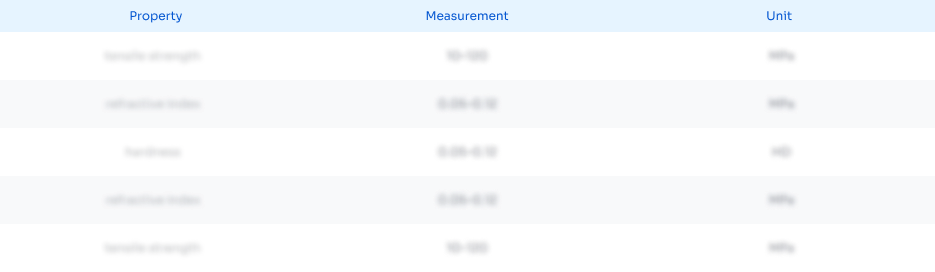
Abstract
Description
Claims
Application Information

- R&D
- Intellectual Property
- Life Sciences
- Materials
- Tech Scout
- Unparalleled Data Quality
- Higher Quality Content
- 60% Fewer Hallucinations
Browse by: Latest US Patents, China's latest patents, Technical Efficacy Thesaurus, Application Domain, Technology Topic, Popular Technical Reports.
© 2025 PatSnap. All rights reserved.Legal|Privacy policy|Modern Slavery Act Transparency Statement|Sitemap|About US| Contact US: help@patsnap.com