Wear-resistant cast steel and preparation method thereof
A technology of cast steel and raw materials, which is applied in the field of wear-resistant cast steel and its preparation, can solve the problems of poor wear resistance, low production efficiency, and low coal throughput, achieve excellent strength and toughness coordination, reduce production costs, and improve overall performance Effect
- Summary
- Abstract
- Description
- Claims
- Application Information
AI Technical Summary
Problems solved by technology
Method used
Image
Examples
Embodiment 1
[0040] A wear-resistant cast steel, comprising the following raw materials in mass percentage: C 0.26%, Cr 1.0%, Si 0.2%, Mn 1.0%, B 0.005%, S 0.019%, P 0.017%, Mo 0.2%, Ni 1.0% , rare earth 0.03%, and the balance is Fe.
[0041] Follow the steps below:
[0042] 1. Raw material smelting: put the raw material in an intermediate frequency induction furnace for smelting, the melting temperature is 1620°C, and keep for 5 minutes;
[0043] 2. Ladle: Ladle the melted raw materials, and add 0.1% aluminum alloy to the bottom of the ladle;
[0044] 3. Pouring molding: in step 2, the temperature of the mixture in the ladle is lowered to 1580°C, and then casting is performed to obtain a casting;
[0045] 4. Heat treatment:
[0046] Perform pretreatment on the castings obtained in step 3, the temperature is 800 ° C, air cooling after 4 hours of heat preservation, the casting quenching heating temperature is 900 ° C, oil quenching after 4 hours of heat preservation, tempering at 350 ° C...
Embodiment 2
[0048] A wear-resistant cast steel, comprising the following raw materials in mass percentage: C 0.33%, Cr 1.3%, Si 0.5%, Mn 1.3%, B 0.006%, S 0.035%, P 0.035%, Mo 0.3%, Ni 1.5% , Rare earth 0.06%, the balance is Fe.
[0049] Follow the steps below:
[0050] 1. Raw material smelting: put the raw material in an intermediate frequency induction furnace for smelting, the temperature of the smelting raw material is 1635°C, and keep for 7.5 minutes;
[0051] 2. Ladle: Ladle the melted raw materials, and add 0.15% aluminum alloy to the bottom of the ladle;
[0052] 3. Pouring molding: in step 2, the temperature of the mixture in the ladle is lowered to 1590°C for pouring and molding to obtain a casting;
[0053] 4. Heat treatment:
[0054]Perform pretreatment on the castings obtained in step 3, the temperature is 850 ° C, air cooling after 5 hours of heat preservation, the casting quenching heating temperature is 950 ° C, oil quenching after 5 hours of heat preservation, temperin...
Embodiment 3
[0056] A wear-resistant cast steel, comprising the following raw materials in mass percentage: C 0.29%, Cr 1.19%, Si 0.45%, Mn 1.18%, B 0.001%, S 0.001%, P 0.005%, Mo 0.27%, Ni 1.25% , Rare earth 0.045%, the balance is Fe.
[0057] Follow the steps below:
[0058] 1: Raw material smelting: put the raw material in an intermediate frequency induction furnace for smelting, the temperature of the smelting raw material is 1650°C, and keep it for 10 minutes;
[0059] Two: ladle: pour the molten raw material into a ladle, and add 0.3% aluminum alloy to the bottom of the ladle;
[0060] Three: Pouring molding: In step 2, the temperature of the mixture in the ladle is lowered to 1600°C for pouring and molding to obtain a casting;
[0061] Four: heat treatment:
[0062] Perform pretreatment on the castings obtained in step 3, the temperature is 900 ° C, air cooling after 6 hours of heat preservation, the casting quenching heating temperature is 1000 ° C, oil quenching after 6 hours o...
PUM
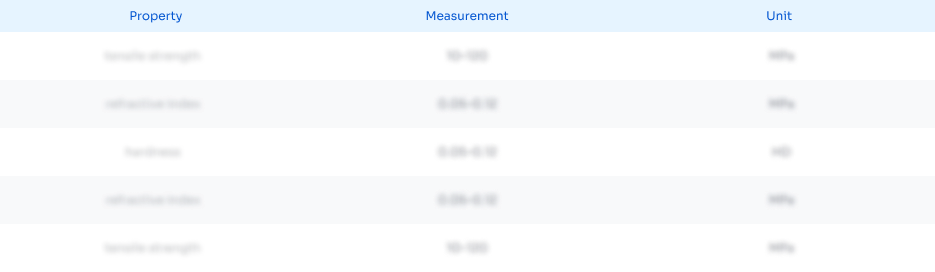
Abstract
Description
Claims
Application Information

- Generate Ideas
- Intellectual Property
- Life Sciences
- Materials
- Tech Scout
- Unparalleled Data Quality
- Higher Quality Content
- 60% Fewer Hallucinations
Browse by: Latest US Patents, China's latest patents, Technical Efficacy Thesaurus, Application Domain, Technology Topic, Popular Technical Reports.
© 2025 PatSnap. All rights reserved.Legal|Privacy policy|Modern Slavery Act Transparency Statement|Sitemap|About US| Contact US: help@patsnap.com