Preparation method of silicon nitride-based composite foamed ceramic
A technology based on composite foam and silicon nitride, which is applied in the field of foamed ceramic materials, can solve the problems of poor strength and achieve strong corrosion resistance, improved strength and high temperature resistance, and good high temperature conductivity
- Summary
- Abstract
- Description
- Claims
- Application Information
AI Technical Summary
Problems solved by technology
Method used
Examples
Embodiment 1
[0038] In terms of parts by weight, weigh 30 parts of formaldehyde, 40 parts of phenol, 18 parts of ammonia water with a mass concentration of 10%, and 80 parts of deionized water, add formaldehyde to the deionized water, and stir at 120 r / min for 10 minutes at room temperature to obtain Formaldehyde solution, add phenol and ammonia water to the formaldehyde solution, stir and react at 240r / min in a water bath at 85°C for 10min, keep the temperature for 15min, and obtain the reactant, wash the reactant three times with deionized water, place in Stand for 1 hour under negative pressure of -0.06MPa, then dry in an oven at 60°C for 1 hour, and cool at room temperature to obtain phenolic resin; then weigh 20 parts of magnesium hydroxide and 40 parts of bicarbonate in parts by weight ammonium, 80 parts of deionized water, magnesium hydroxide was added to the deionized water, stirred at 1000r / min at room temperature for 1h to obtain milk of magnesia, ammonium bicarbonate was added to...
Embodiment 2
[0040] In terms of parts by weight, weigh 35 parts of formaldehyde, 50 parts of phenol, 21 parts of ammonia water with a mass concentration of 10%, and 90 parts of deionized water, add formaldehyde to the deionized water, and stir at 140 r / min for 11 minutes at room temperature to obtain Formaldehyde solution, add phenol and ammonia water to the formaldehyde solution, stir and react at 260r / min in a water bath at 90°C for 12min, keep the temperature for 25min, and obtain the reactant, wash the reactant 4 times with deionized water, place in Stand still under negative pressure of -0.04MPa for 1 hour, then dry in an oven at 70°C for 1 hour, and cool at room temperature to obtain phenolic resin; then weigh 25 parts of magnesium hydroxide and 50 parts of bicarbonate in parts by weight ammonium, 100 parts of deionized water, magnesium hydroxide was added into the deionized water, stirred at a speed of 1100r / min at room temperature for 1h to obtain milk of magnesia, ammonium bicarbon...
Embodiment 3
[0042] In terms of parts by weight, weigh 40 parts of formaldehyde, 60 parts of phenol, 24 parts of ammonia water with a mass concentration of 10%, and 100 parts of deionized water, add formaldehyde to the deionized water, and stir at a speed of 160 r / min for 12 minutes at room temperature to obtain Formaldehyde solution, add phenol and ammonia water to the formaldehyde solution, stir and react at 280r / min in a water bath at 95°C for 15min, keep the temperature for 30min, and obtain the reactant, wash the reactant 5 times with deionized water, place in Stand for 2 hours under negative pressure of -0.02MPa, then dry in an oven at 80°C for 2 hours, and cool at room temperature to obtain phenolic resin; then weigh 30 parts of magnesium hydroxide and 60 parts of bicarbonate in parts by weight Ammonium, 120 parts of deionized water, magnesium hydroxide was added to deionized water, stirred at 1200r / min at room temperature for 2h to obtain milk of magnesia, ammonium bicarbonate was a...
PUM
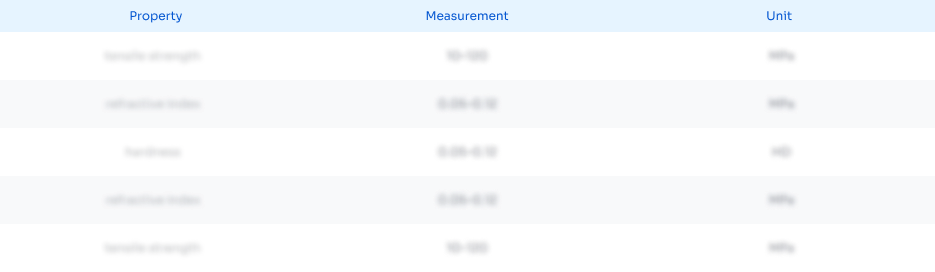
Abstract
Description
Claims
Application Information

- R&D
- Intellectual Property
- Life Sciences
- Materials
- Tech Scout
- Unparalleled Data Quality
- Higher Quality Content
- 60% Fewer Hallucinations
Browse by: Latest US Patents, China's latest patents, Technical Efficacy Thesaurus, Application Domain, Technology Topic, Popular Technical Reports.
© 2025 PatSnap. All rights reserved.Legal|Privacy policy|Modern Slavery Act Transparency Statement|Sitemap|About US| Contact US: help@patsnap.com