Material and processing technology of water scraping plate of descaling box
A processing technology and wiper technology, which is applied in the field of materials and processing technology of the descaler box wiper, can solve the problems that new materials cannot be directly processed and used, the product qualification rate is low, and the manufacturing cost is increased, so as to achieve superior performance , The processing technology is simple, and the effect of improving the grain boundary condition
- Summary
- Abstract
- Description
- Claims
- Application Information
AI Technical Summary
Problems solved by technology
Method used
Image
Examples
Embodiment 1
[0015] Embodiment 1: first process the metal abrasive tool, design and manufacture the aluminum mold according to the product drawing, be used for making paraffin core. Brush the high-temperature resistant paint 2-3 times; then carry out sand mixing modeling. The sand mixing process is as follows: raw sand plus disintegrating agent and mixing for 1 minute → adding organic grease and mixing for 2 minutes → adding water glass and mixing for 1 minute → sanding, and the modeling is completed within 30 minutes; then heating Bake the mold, heat the mold in the oven, heat it at 195°C, and take it out of the oven for 10 hours; then melt it in a 500Kg acidic intermediate frequency electric furnace, first add scrap steel into the electric furnace, and then add low-carbon ferrochromium, pure tungsten, and nickel plates , ferromolybdenum to adjust the composition of molten steel, adjust the ratio of elements and carbon content according to the pre-furnace test, add 0.05% pure aluminum for ...
Embodiment 2
[0016] Embodiment 2: first process the metal abrasive tool, design and manufacture the aluminum mold according to the product drawing, and be used for making the paraffin core. Brush the high-temperature resistant paint 2-3 times; then carry out sand-mixing molding, the sand-mixing process is as follows: raw sand plus disintegrating agent and mixing for 1 minute → adding organic grease and mixing for 3 minutes → adding water glass and mixing for 2 minutes → sanding, and the modeling is completed within 30 minutes; then heating Bake the mold, heat the mold in the oven, heat it at 200°C, and take it out of the oven for 10 hours; then melt it in a 500Kg acidic intermediate frequency electric furnace, first add scrap steel into the electric furnace, and then add low-carbon ferrochromium, pure tungsten, and nickel plates , ferromolybdenum to adjust the composition of molten steel, adjust the ratio of elements and carbon content according to the pre-furnace test, add 0.05% pure alumi...
PUM
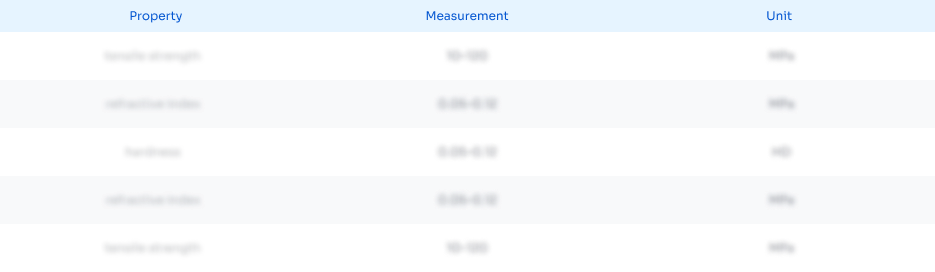
Abstract
Description
Claims
Application Information

- Generate Ideas
- Intellectual Property
- Life Sciences
- Materials
- Tech Scout
- Unparalleled Data Quality
- Higher Quality Content
- 60% Fewer Hallucinations
Browse by: Latest US Patents, China's latest patents, Technical Efficacy Thesaurus, Application Domain, Technology Topic, Popular Technical Reports.
© 2025 PatSnap. All rights reserved.Legal|Privacy policy|Modern Slavery Act Transparency Statement|Sitemap|About US| Contact US: help@patsnap.com