Integrated forging and forming method for reactor pressure vessel barrel flange adapter tube section
A technology for cylinder flanges and pressure vessels, which is applied to engine components, mechanical equipment, etc., can solve the problems of reducing the safety of cylinder flange joints, poor quality stability in complex stress areas, and increasing the workload of in-service inspections. Achieve the effects of shortening the equipment manufacturing cycle, solving the anisotropy of forgings, and avoiding structural defects in forgings
- Summary
- Abstract
- Description
- Claims
- Application Information
AI Technical Summary
Problems solved by technology
Method used
Image
Examples
Embodiment Construction
[0044] figure 1 It is a flow chart of the process steps of the overall forging forming method of the flange connection section of the present invention. In each step of the process method, the initial forging temperature of the steel ingot forging is 850°C, and the final forging temperature of the steel ingot forging is 1270°C. When the temperature is lower than 850°C, the forging should be re-sent into the heating furnace for heating to 1270°C, so that the forging temperature of the forging should be kept within the range of 850°C-1270°C. Its steps of the forging forming method of the present embodiment are as follows:
[0045] Steel ingot heating: the material of the steel ingot in this embodiment is 508-3 steel, and the amount of steel ingot is 100 tons. First, the steel ingot is heated in sections, and the steel ingot is put into the heating furnace for heating to improve the plasticity of the metal, make it easy to flow and form and obtain a good forged structure, and ch...
PUM
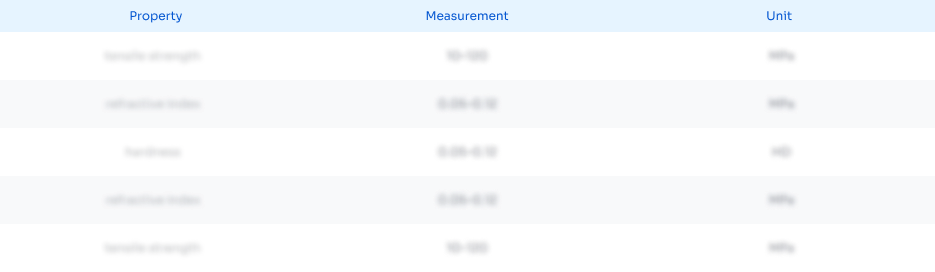
Abstract
Description
Claims
Application Information

- R&D
- Intellectual Property
- Life Sciences
- Materials
- Tech Scout
- Unparalleled Data Quality
- Higher Quality Content
- 60% Fewer Hallucinations
Browse by: Latest US Patents, China's latest patents, Technical Efficacy Thesaurus, Application Domain, Technology Topic, Popular Technical Reports.
© 2025 PatSnap. All rights reserved.Legal|Privacy policy|Modern Slavery Act Transparency Statement|Sitemap|About US| Contact US: help@patsnap.com