Preparing method for machine barrel inner wall wear-resisting layer
A technology of wear-resistant layer and machine barrel, which is applied in coating, metal material coating process, etc., can solve the problem of unsatisfactory wear-resistant performance of alloy wear-resistant layer, uneven surface of alloy wear-resistant layer, uneven heating of alloy wear-resistant layer Balance and other issues, to achieve the effect of continuous automatic production, reduce heat energy consumption, and convenient preparation
- Summary
- Abstract
- Description
- Claims
- Application Information
AI Technical Summary
Problems solved by technology
Method used
Image
Examples
Embodiment Construction
[0031] The present invention will be further described in detail below in conjunction with the accompanying drawings and embodiments.
[0032] Such as Figure 1 to Figure 11 As shown, the preparation method of the barrel inner wall wear-resistant layer of the present embodiment comprises the following steps,
[0033] 1. Put the iron-based alloy powder in the inner cavity of the machine barrel, and seal the openings at both ends of the machine barrel after the iron-based alloy powder is placed;
[0034] 2. Place the barrel 4 with both ends closed in a heating furnace with a temperature of 1000-1300°C for heating. When the barrel 4 is heated in the heating furnace, keep the radial rotation and keep moving back and forth in the axial direction. When the inner cavity of the barrel After the iron-based alloy powder is uniformly melted in the inner cavity of the barrel, the molten iron-based alloy powder will cover the inner peripheral surface of the inner wall of the barrel with t...
PUM
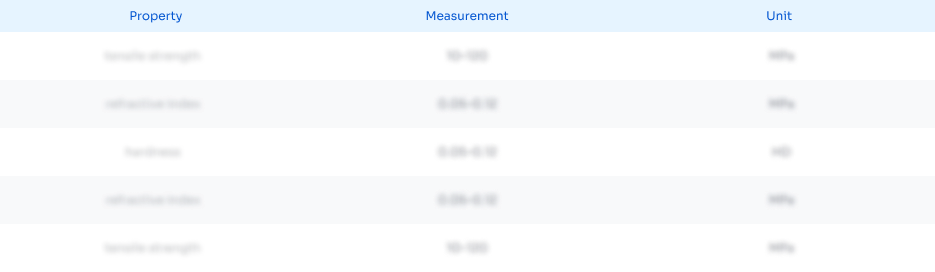
Abstract
Description
Claims
Application Information

- R&D Engineer
- R&D Manager
- IP Professional
- Industry Leading Data Capabilities
- Powerful AI technology
- Patent DNA Extraction
Browse by: Latest US Patents, China's latest patents, Technical Efficacy Thesaurus, Application Domain, Technology Topic, Popular Technical Reports.
© 2024 PatSnap. All rights reserved.Legal|Privacy policy|Modern Slavery Act Transparency Statement|Sitemap|About US| Contact US: help@patsnap.com