Disperse deep blue dye color paste and preparation method thereof
A technology for dispersing dark blue and dye paste, applied in the field of dyes, can solve the problems of low utilization rate of dyes, poor compatibility between disperse dyes and synthetic thickeners, large floating color, etc., and achieve good dye transfer and permeability, Good washing fastness and moderate viscosity
- Summary
- Abstract
- Description
- Claims
- Application Information
AI Technical Summary
Problems solved by technology
Method used
Image
Examples
preparation example Construction
[0027] If there is no special description, the water-soluble nonionic surfactant in the present invention is selected from one or more of fatty alcohol polyoxyethylene ether, alkylphenol polyoxyethylene ether, fatty acid polyoxyethylene ester; The nonionic thickener is selected from one or more of polyethylene glycol, polyether nonionic surfactants, polyvinylpyrrolidone, and polyvinyl alcohol; the oil-soluble nonionic surfactant is selected from fat One or more of alcohol polyoxyethylene ether, alkylphenol polyoxyethylene ether, fatty acid polyoxyethylene ester, sorbitan fatty acid ester, fatty acid glyceride; the dispersant is sulfonated lignin, naphthalene sulfonate One or more of sodium formaldehyde condensate and benzyl naphthalenesulfonic acid formaldehyde condensate, and the average molecular weight of the sulfonated lignin dispersant is 10000-15000, and the sulfonation degree is 0.8-1.5, and the dispersant is Sulfonated lignin and sodium naphthalenesulfonate formaldehyd...
Embodiment 1
[0035] Take the following raw materials for use: disperse dark blue dye 10%, resist salt 0.9%, water-soluble nonionic surfactant 7%, nonionic thickener 2.5%, oil-soluble nonionic surfactant 5%, ethanol 6 %, starch 4%, vinyl acetate 6%, acrylic acid 6%, emulsifier 1.0%, urea 2.1%, preservative 0.6%, dispersant 4%, glacial acetic acid 1.2%, chitosan 2.5%, also contains penetrant , leveling agent and anti-migration agent, and the content of penetrating agent in the color paste is 2g / L, the leveling agent is 3g / L, and the anti-migration agent is 4.5g / L. The disperse dark blue dye is a high-strength dispersion Dye, the strength is 200~500%.
[0036] Prepare disperse dark blue dye paste as follows:
[0037] (1) Add water to the reaction vessel, add starch while stirring, and gradually expand and gelatinize the starch under stirring at room temperature; after the starch is fully dissolved, add vinyl acetate, stir, and drop emulsifier until the entire reaction system It is milky whi...
Embodiment 2
[0043] Take the following raw materials for use: 9% disperse dark blue dye, 0.8% anti-staining salt, 5% water-soluble nonionic surfactant, 2% nonionic thickener, 4% oil-soluble nonionic surfactant, 5% ethanol %, starch 3%, vinyl acetate 5%, acrylic acid 5%, emulsifier 0.7%, urea 1.5%, preservative 0.3%, dispersant 3%, glacial acetic acid 0.9%, chitosan 2%, also contains penetrant , leveling agent and anti-migration agent, and the content of penetrant in the color paste is 1g / L, the leveling agent is 2g / L, and the anti-migration agent is 4g / L. The disperse dark blue dye is a high-strength disperse dye , the strength is 200~500%.
[0044] Prepare disperse dark blue dye paste as follows:
[0045] (1) Add water to the reaction vessel, add starch while stirring, and gradually expand and gelatinize the starch under stirring at room temperature; after the starch is fully dissolved, add vinyl acetate, stir, and drop emulsifier until the entire reaction system It is milky white, then...
PUM
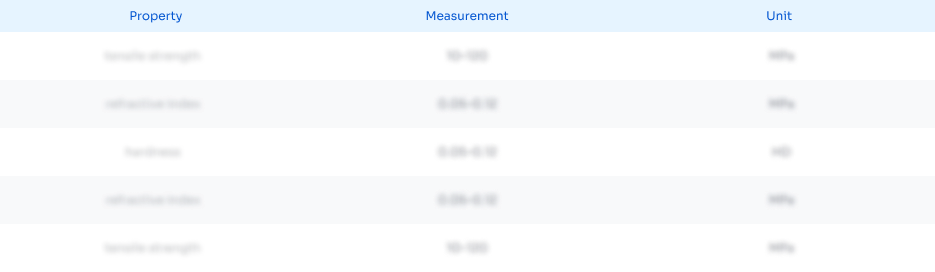
Abstract
Description
Claims
Application Information

- R&D
- Intellectual Property
- Life Sciences
- Materials
- Tech Scout
- Unparalleled Data Quality
- Higher Quality Content
- 60% Fewer Hallucinations
Browse by: Latest US Patents, China's latest patents, Technical Efficacy Thesaurus, Application Domain, Technology Topic, Popular Technical Reports.
© 2025 PatSnap. All rights reserved.Legal|Privacy policy|Modern Slavery Act Transparency Statement|Sitemap|About US| Contact US: help@patsnap.com