A kind of max phase/nitride ceramic layered gradient composite material and its rapid preparation method and application
A technology of nitride ceramics and composite materials, which is applied in ceramic layered products, chemical instruments and methods, layered products, etc. The sintering process is complex and other problems, to achieve the effect of ensuring purity and performance, low sintering temperature, and wide application prospects
- Summary
- Abstract
- Description
- Claims
- Application Information
AI Technical Summary
Problems solved by technology
Method used
Image
Examples
Embodiment 1
[0032] Choose Ti 3 SiC 2 Powder, Si 3 N 4 Powder and corresponding sintering aids are the original powder materials, and 7-layer gradient materials are prepared by SPS sintering.
[0033] Ti 3 SiC 2 Powder, Si 3 N 4 Powder and corresponding sintering aids are mixed according to the designed volume fraction, and ethanol solvent is added for wet milling, and the ball milling time is 24 hours; the mixed powder required for each layer is mixed according to the following formula figure 1 As shown in c, put them in graphite molds for layering and pressing in sequence, each layer thickness is 1mm, then install the upper and lower pressure heads and coat the graphite carbon felt to complete the mold loading work; put the mold with the sample to be sintered in the spark plasma sintering system In the furnace, vacuumize to no higher than 0.01Pa, under the axial pressure of 70MPa, raise the temperature to 1200°C at a rate of 300°C / min, and then increase the temperature at a rate o...
Embodiment 2
[0035] Choose Ti 3 SiC 2Powder, Si 3 N 4 The powder and corresponding sintering aids are the original powder materials, and the 5-layer gradient materials are prepared by SPS sintering.
[0036] Ti 3 SiC 2 Powder, Si 3 N 4 Powder and corresponding sintering aids are mixed according to the designed volume fraction, and ethanol solvent is added for wet milling, and the ball milling time is 24 hours; the mixed powder required for each layer is mixed according to the following formula figure 1 As shown in a, place the layers in the graphite mold for layering and pressing in sequence, each layer is 2mm thick, then install the upper and lower pressure heads and coat the graphite carbon felt to complete the mold loading work; put the mold with the sample to be sintered in the spark plasma sintering system In the furnace, vacuumize to no higher than 0.01Pa, under the axial pressure of 50MPa, raise the temperature to 1200°C at a rate of 200°C / min, and then increase the temperatu...
Embodiment 3
[0038] Choose Ti 3 SiC 2 Powder, Si 3 N 4 Powder and corresponding sintering aids are the original powder materials, and 6-layer gradient materials are prepared by SPS sintering.
[0039] Ti 3 SiC 2 Powder, Si 3 N 4 Powder and corresponding sintering aids are mixed according to the designed volume fraction, and ethanol solvent is added for wet milling, and the ball milling time is 24 hours; the mixed powder required for each layer is mixed according to the following formula figure 1 As shown in middle b, lay up and press in the graphite mold in turn, each layer thickness is 1.5mm, then install the upper and lower pressure heads and coat the graphite carbon felt to complete the mold loading work; put the mold with the sample to be sintered in spark plasma sintering In the furnace of the system, vacuumize to no higher than 0.01Pa, under the axial pressure of 50MPa, heat up to 1200°C at a rate of 100°C / min, and then rise to 1380°C at a rate of 150°C / min and keep for 4 minu...
PUM
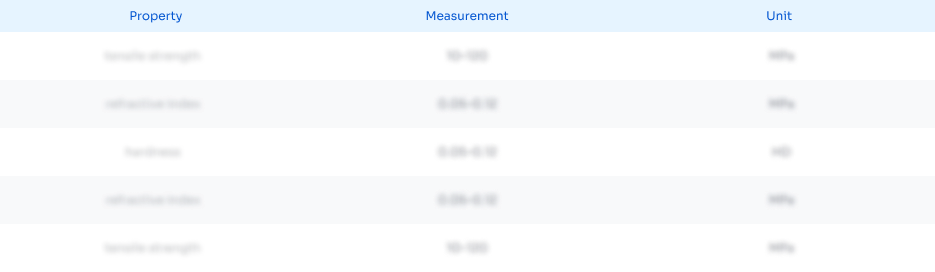
Abstract
Description
Claims
Application Information

- Generate Ideas
- Intellectual Property
- Life Sciences
- Materials
- Tech Scout
- Unparalleled Data Quality
- Higher Quality Content
- 60% Fewer Hallucinations
Browse by: Latest US Patents, China's latest patents, Technical Efficacy Thesaurus, Application Domain, Technology Topic, Popular Technical Reports.
© 2025 PatSnap. All rights reserved.Legal|Privacy policy|Modern Slavery Act Transparency Statement|Sitemap|About US| Contact US: help@patsnap.com