A composite lithium ion battery separator
A lithium-ion battery, ion battery technology, applied in secondary batteries, battery pack parts, circuits, etc., can solve the problem of wettability, porosity, low electrolyte absorption rate, unsatisfactory comprehensive performance of the diaphragm, and thermal shrinkage of the diaphragm. Reduction and other problems, to achieve the effect of excellent contact angle and liquid absorption rate, conducive to transmission, and excellent air permeability
- Summary
- Abstract
- Description
- Claims
- Application Information
AI Technical Summary
Problems solved by technology
Method used
Image
Examples
Embodiment 1
[0020] Prepare a polytetrafluoroethylene DMF solution with a mass concentration of 6%, and take an appropriate amount of the solution for electrospinning. The electrospinning parameters are as follows: the spinning voltage is 18kV, the propulsion rate is 0.015mL / min, the spinning receiving distance is 25cm, and the syringe The needle is 10#, and the polytetrafluoroethylene fiber membrane is obtained by spinning at room temperature for 8 hours; the bisphenol A polycarbonate DMF solution with a mass concentration of 6% is prepared, and the polytetrafluoroethylene fiber membrane is soaked in it for 2 hours, and then Take it out and put it in a vacuum drying oven and dry it at 100°C for 24 hours to obtain a polytetrafluoroethylene / polycarbonate composite fiber membrane. After determination, the mass fraction of polytetrafluoroethylene is 87%, and the mass fraction of polycarbonate is 13%.
Embodiment 2
[0022] Prepare a polytetrafluoroethylene DMF solution with a mass concentration of 15%, and take an appropriate amount of the solution for electrospinning. The electrospinning parameters are as follows: the spinning voltage is 18kV, the propulsion rate is 0.015mL / min, the spinning receiving distance is 25cm, and the syringe The needle is 10#, spinning at room temperature for 2h to obtain a polytetrafluoroethylene fiber membrane; prepare a tetrachlorobisphenol A polycarbonate DMF solution with a mass concentration of 2%, put the polytetrafluoroethylene fiber membrane into it and soak for 5h , and then take it out and put it into a vacuum drying oven and dry it at 100°C for 24 hours to obtain a polytetrafluoroethylene / polycarbonate composite fiber membrane. After determination, the mass fraction of polytetrafluoroethylene is 93%, and the mass fraction of polycarbonate is 7%.
Embodiment 3
[0024] Prepare a polytetrafluoroethylene DMF solution with a mass concentration of 12%, and take an appropriate amount of the solution for electrospinning. The electrospinning parameters are as follows: the spinning voltage is 18kV, the propulsion rate is 0.015mL / min, and the spinning receiving distance is 25cm. The needle is 10#, and the polytetrafluoroethylene fiber membrane is obtained by spinning at room temperature for 6 hours; the tetrabromobisphenol A polycarbonate DMF solution with a mass concentration of 5% is prepared, and the polytetrafluoroethylene fiber membrane is soaked in it for 4 hours , and then take it out and put it into a vacuum drying oven and dry it at 100°C for 24 hours to obtain a polytetrafluoroethylene / polycarbonate composite fiber membrane. After determination, the mass fraction of polytetrafluoroethylene is 80%, and the mass fraction of polycarbonate is 20%.
PUM
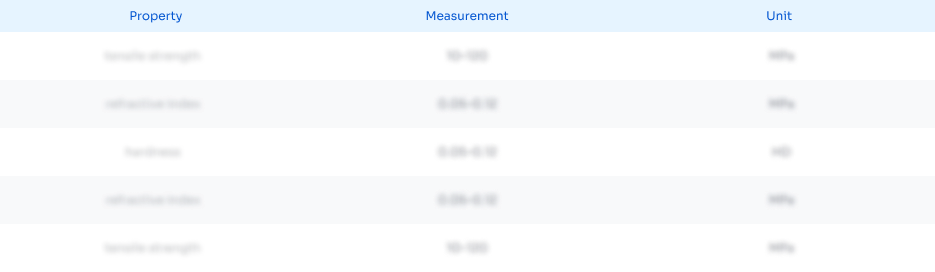
Abstract
Description
Claims
Application Information

- R&D Engineer
- R&D Manager
- IP Professional
- Industry Leading Data Capabilities
- Powerful AI technology
- Patent DNA Extraction
Browse by: Latest US Patents, China's latest patents, Technical Efficacy Thesaurus, Application Domain, Technology Topic, Popular Technical Reports.
© 2024 PatSnap. All rights reserved.Legal|Privacy policy|Modern Slavery Act Transparency Statement|Sitemap|About US| Contact US: help@patsnap.com