Method for preparing MoSi2 (molybdenum disilicide) coating layer by surface laser cladding of molybdenum alloy
A laser cladding, molybdenum alloy technology, applied in metal material coating process, coating, superimposed layer plating and other directions, can solve the problem of easy occurrence of stress and cracks, weak coating adhesion, and high brittleness of the coating. problem, to achieve the effect of improving high temperature oxidation resistance, improving oxidation resistance and improving mechanical properties
- Summary
- Abstract
- Description
- Claims
- Application Information
AI Technical Summary
Problems solved by technology
Method used
Image
Examples
Embodiment 1
[0029] First, the surface of the molybdenum alloy is polished, ultrasonically cleaned with alcohol, dried, and then a thin layer of Si with a thickness of 25 μm is sputtered on the molybdenum alloy by magnetron sputtering, using high-purity argon as the sputtering gas, and the flow rate of the argon gas is 25sccm, the argon sputtering pressure is 0.25Pa. The mass percent is Mo 60%, Nb 3.5%, W 3.0%, Cr 2.5%, Ti 2.0%, Al 2.0%, and the balance is Si for a long time ball milling, the ball milling time is 18h, and the rotating speed is 300r / min. After that, acetone was used to adhere the alloy powder to the surface of the molybdenum alloy sputtered with Si thin layer. The thickness of the alloy powder was preset to be 0.5mm, and then placed in a heating furnace at 140°C for 30 minutes to dry. A laser is used to scan the molybdenum alloy sputtered Si thin layer. The overlapping rate of the laser scanning is 40%, the laser power is 2.0kW, and the scanning speed is 8mm / s to make the...
Embodiment 2
[0031] First, the surface of the molybdenum alloy is polished, ultrasonically cleaned with alcohol, dried, and then a thin layer of Si with a thickness of 20 μm is sputtered on the molybdenum alloy by magnetron sputtering, using high-purity argon as the sputtering gas, and the flow rate of the argon gas is 25sccm, the argon sputtering pressure is 0.25Pa. The mass percentage is Mo 55%, Nb 5.5%, W 4.5%, Cr 3.5%, Ti 2.5%, Al 3.0%, and the balance is Si for a long time ball milling, the ball milling time is 21h, and the rotating speed is 350r / min. After that, acetone was used to adhere the alloy powder to the surface of the molybdenum alloy sputtered with Si thin layer. The thickness of the alloy powder was preset to be 0.8mm, and then placed in a heating furnace at 150°C for 30 minutes to dry. A laser is used to scan the molybdenum alloy sputtered Si thin layer. The overlapping rate of the laser scanning is 40%, the laser power is 2.2kW, and the scanning speed is 6mm / s, and the...
Embodiment 3
[0033] First, the surface of the molybdenum alloy is polished, ultrasonically cleaned with alcohol, dried, and then a thin layer of Si with a thickness of 30 μm is sputtered on the molybdenum alloy by magnetron sputtering, using high-purity argon as the sputtering gas, and the flow rate of the argon gas is 25sccm, the argon sputtering pressure is 0.25Pa. The mass percentage is Mo 50%, Nb 7.5%, W 6.0%, Cr 4.5%, Ti 3.5%, Al 5.5%, and the balance is Si for a long time ball milling, the ball milling time is 24h, and the speed is 400r / min. After that, acetone was used to adhere the alloy powder to the surface of the molybdenum alloy sputtered with Si thin layer. The thickness of the alloy powder was preset to be 1.0 mm, and then it was placed in a heating furnace at 160°C for 40 minutes to dry. A laser is used to scan the molybdenum alloy sputtered Si thin layer. The overlapping rate of the laser scanning is 40%, the laser power is 2.4kW, and the scanning speed is 8mm / s, and the ...
PUM
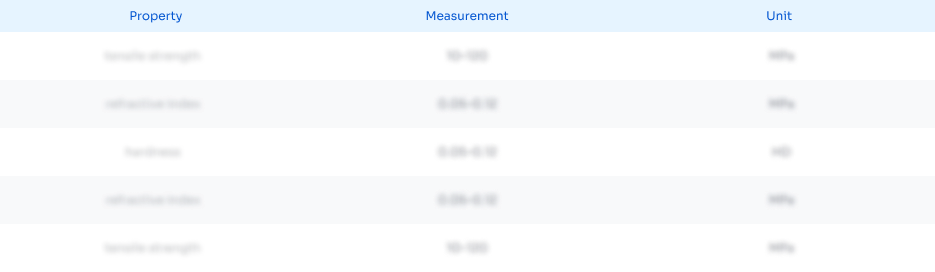
Abstract
Description
Claims
Application Information

- R&D
- Intellectual Property
- Life Sciences
- Materials
- Tech Scout
- Unparalleled Data Quality
- Higher Quality Content
- 60% Fewer Hallucinations
Browse by: Latest US Patents, China's latest patents, Technical Efficacy Thesaurus, Application Domain, Technology Topic, Popular Technical Reports.
© 2025 PatSnap. All rights reserved.Legal|Privacy policy|Modern Slavery Act Transparency Statement|Sitemap|About US| Contact US: help@patsnap.com