A kind of corrosion-resistant high-temperature resistant ceramic-organic composite coating and its preparation method and application as metal corrosion-resistant coating
A technology of high-temperature resistant ceramics and composite coatings, applied in coatings, surface reaction electrolytic coatings, devices for coating liquids on surfaces, etc., can solve problems such as poor corrosion resistance and achieve long-term resistance to neutral salt solutions Corrosion, good compatibility, improve the effect of barrier effect
- Summary
- Abstract
- Description
- Claims
- Application Information
AI Technical Summary
Problems solved by technology
Method used
Image
Examples
Embodiment 1
[0049] The sample is 7 series aluminum alloy, and the sample size is 50*50*3mm.
[0050] The first step is alloy pretreatment. Use 180-1200# water sandpaper to grind from coarse to fine, wash with water, then ultrasonically clean in acetone solution for 10min, and wash with deionized water.
[0051] The second step is micro-arc oxidation treatment. The micro-arc oxidation power supply adopts AC power supply, constant current mode, power frequency is 750Hz, pulse width is 307μs, duty cycle is 17%, and the electrolyte is composed of sodium silicate, sodium tungstate, sodium phosphate and Sodium hydroxide composition. Using a stirring and cooling device, control the solution temperature at 15°C±1°C, and the oxidation time is 25min.
[0052] The third step is to seal the holes. The sealing treatment steps are: ① Configure silane solution, add 20ml tetraethoxysilane to 40ml ethanol, place on a magnetic stirrer and stir evenly, add 10ml silane coupling agent KH570, after stirring...
Embodiment 2
[0059] The sample is 2-series aluminum alloy, and the sample size is 50*50*3mm.
[0060] The difference from Example 1 is that the second step is micro-arc oxidation treatment. The micro-arc oxidation power supply adopts DC power supply, and the control current density is 8A / dm 2 , the electrolyte consists of sodium silicate, glycerin and sodium hydroxide. Using a stirring and cooling device, control the temperature of the solution at 30°C ± 5°C, and conduct micro-arc oxidation for 15 minutes. The fourth step is to prepare a silane-modified epoxy resin organic coating. The preparation steps are as follows: ① Dissolve bisphenol A diglycidyl ether and polyamide in a solvent at a mass ratio of 10:7 to form an epoxy solution. The solvent used is xylene and n-butanol mixed in a volume ratio of 2:1, and the mass ratio of solvent to bisphenol A diglycidyl ether is 2:1. Then mix the silane solution aged for 48 hours in the third step into the epoxy solution, and the mass ratio of ...
Embodiment 3
[0065] The sample is cast aluminum alloy, and the sample size is 50*50*3mm.
[0066] The difference from Example 1 is that the fourth step is to prepare a silane-modified epoxy resin organic coating. The preparation steps are: ① dissolving bisphenol A diglycidyl ether and polyamide in a solvent at a mass ratio of 5:1 to form an epoxy solution. The solvent used is xylene and n-butanol mixed in a volume ratio of 2:1, and the mass ratio of solvent to bisphenol A diglycidyl ether is 1:1. Then mix the silane solution aged for 48 hours in the third step into the epoxy solution, and the mass ratio of the silane solution to the epoxy resin is 3:1. Stirring was continued for 5 hours to form a silane-modified epoxy resin organic polymer solution. ② The alloy after silane sealing treatment is dip-coated in silane-modified epoxy resin organic polymer solution for 10 seconds, taken out, dried naturally at room temperature for 12 hours, and then put into a constant temperature drying oven...
PUM
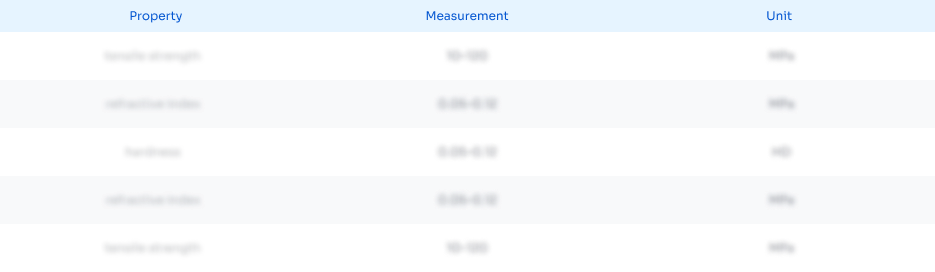
Abstract
Description
Claims
Application Information

- R&D Engineer
- R&D Manager
- IP Professional
- Industry Leading Data Capabilities
- Powerful AI technology
- Patent DNA Extraction
Browse by: Latest US Patents, China's latest patents, Technical Efficacy Thesaurus, Application Domain, Technology Topic, Popular Technical Reports.
© 2024 PatSnap. All rights reserved.Legal|Privacy policy|Modern Slavery Act Transparency Statement|Sitemap|About US| Contact US: help@patsnap.com