Preparation method of fireproof paint
A fire-resistant coating, stirring and mixing technology, which is applied in the direction of fire-resistant coatings, epoxy resin coatings, polyurea/polyurethane coatings, etc., can solve the problems of fire-resistant coatings such as durability, poor weather resistance, and poor bonding strength, and achieve good adhesion , good water resistance, and the effect of slowing down the attack
- Summary
- Abstract
- Description
- Claims
- Application Information
AI Technical Summary
Problems solved by technology
Method used
Image
Examples
Embodiment approach
[0023] Flame retardant auxiliary agent: in parts by mass, take 10-15 parts of expandable graphite, 4-8 parts of sepiolite, 5-8 parts of titanium dioxide, and 1-3 parts of barium sulfate, grind and pulverize for 20-30 minutes, pass 200-mesh sieve to collect the sieved particles to obtain the flame retardant auxiliary agent.
[0024] Silicone acrylic emulsion: Take OP-10 according to the mass ratio of 1~3:2~4:9~12, add sodium dodecylsulfonate and distilled water and mix to obtain a mixed emulsion, and take 4~8 parts by mass N-butyl acrylate, 8~12 parts of methyl methacrylate, 4~8 parts of styrene, 10~14 parts of methacrylic acid, 6~12 parts of vinyltriethoxysilane, 8~13 parts of octamethylcyclo Tetrasiloxane, 3~7 parts of mixed emulsion were mixed, stirred and mixed for 40~50 minutes to obtain a stirred mixture, and the stirred mixture was ammonium persulfate and sodium bicarbonate with a mass ratio of 90~100:1~3:2~5, Stir and mix at 75-80°C for 3-5 hours, adjust the pH to 7-8,...
Embodiment 1
[0034] Flame retardant auxiliary agent: in parts by mass, mix 10 parts of expandable graphite, 4 parts of sepiolite, 5 parts of titanium dioxide, and 1 part of barium sulfate, grind and pulverize for 20 minutes, pass through a 200-mesh sieve, and collect the sieved particles, namely Flame retardant auxiliaries.
[0035] Silicone acrylic emulsion: take OP-10 and mix it with sodium dodecylsulfonate and distilled water at a mass ratio of 1:2:9 to obtain a mixed emulsion. In terms of parts by mass, take 4 parts of n-butyl acrylate and 8 parts of formazan Methyl acrylate, 4 parts of styrene, 10 parts of methacrylic acid, 6 parts of vinyltriethoxysilane, 8 parts of octamethylcyclotetrasiloxane, and 3 parts of mixed emulsion were mixed and stirred for 40 minutes to obtain For the mixture, take ammonium persulfate and sodium bicarbonate in a mass ratio of 90:1:2, stir and mix at 75°C for 3 hours, adjust the pH to 7, and cool to room temperature to obtain a silicon-acrylic emulsion.
...
Embodiment 2
[0045] Flame retardant auxiliary agent: in parts by mass, mix 15 parts of expandable graphite, 8 parts of sepiolite, 8 parts of titanium dioxide, and 3 parts of barium sulfate, grind and pulverize for 30 minutes, pass through a 200-mesh sieve, and collect the sieved particles, namely Flame retardant auxiliaries.
[0046] Silicone acrylic emulsion: Take OP-10 and mix it with sodium dodecylsulfonate and distilled water at a mass ratio of 3:4:12 to obtain a mixed emulsion. In terms of parts by mass, take 8 parts of n-butyl acrylate and 12 parts of formazan Methyl acrylate, 8 parts of styrene, 14 parts of methacrylic acid, 12 parts of vinyltriethoxysilane, 13 parts of octamethylcyclotetrasiloxane, and 7 parts of mixed emulsion were mixed and stirred for 50 minutes to obtain For the mixture, take ammonium persulfate and sodium bicarbonate in a mass ratio of 100:3:5, stir and mix at 80°C for 5 hours, adjust the pH to 8, and cool to room temperature to obtain a silicon-acrylic emulsi...
PUM
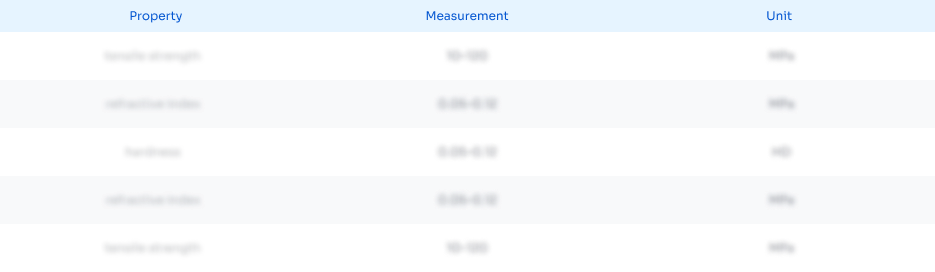
Abstract
Description
Claims
Application Information

- R&D
- Intellectual Property
- Life Sciences
- Materials
- Tech Scout
- Unparalleled Data Quality
- Higher Quality Content
- 60% Fewer Hallucinations
Browse by: Latest US Patents, China's latest patents, Technical Efficacy Thesaurus, Application Domain, Technology Topic, Popular Technical Reports.
© 2025 PatSnap. All rights reserved.Legal|Privacy policy|Modern Slavery Act Transparency Statement|Sitemap|About US| Contact US: help@patsnap.com