Preparation method of composite ceramic insulating coating
A technology of insulating coatings and composite ceramics, applied in coatings, anti-corrosion coatings, etc., can solve problems such as poor mechanical properties and processability, precision and reliability constraints, and achieve good combination, good processability, adhesion and High filming effect
- Summary
- Abstract
- Description
- Claims
- Application Information
AI Technical Summary
Problems solved by technology
Method used
Examples
example 1
[0024] Add 30g of boric acid into 300mL of deionized water, stir at 50°C at 300r / min until the boric acid is completely dissolved, then add 100g of urea, continue stirring at 60°C for 30min, stir evenly, put it in a drying oven, and evaporate at 50°C To dryness, the composite material was obtained, and the composite material was placed in a muffle furnace, heated to 900 ° C for 5 h in a nitrogen atmosphere, and after cooling to room temperature, the calcined product was washed twice with hydrochloric acid with a mass fraction of 1%, and then dehydrated with ethanol Wash the calcined product twice, transfer it to a drying oven after washing, and dry it to a constant weight at 55°C to obtain nano-flaky boron nitride. Take 15g of phosphoric acid, add 50mL of deionized water, stir and heat at 300r / min to 50 ℃, add 5g aluminum hydroxide, continue to stir for 10min, add 10g magnesium oxide, 1g nano-sheet boron nitride, 3g silica sol, 3g nano-titanium dioxide after cooling to 40 ℃, co...
example 2
[0026] Add 40g of boric acid into 400mL of deionized water, stir at 55°C at 350r / min until the boric acid is completely dissolved, then add 110g of urea, continue stirring at 62°C for 35min, stir evenly, put it in a drying oven, and evaporate at 55°C To dryness, the composite material was obtained. The composite material was placed in a muffle furnace, heated to 920°C for 5 hours under nitrogen atmosphere, and calcined for 5 hours. After cooling to room temperature, the calcined product was washed twice with hydrochloric acid with a mass fraction of 1%, and then dehydrated with ethanol. Wash the calcined product twice, transfer it to a drying oven after washing, and dry it to a constant weight at 58 ° C to obtain nano-flaky boron nitride. Take 20 g of phosphoric acid, add 80 mL of deionized water, and stir and heat at 350 r / min to 55 ℃, add 8g aluminum hydroxide, continue to stir for 15min, add 12g magnesium oxide, 1g nano-sheet boron nitride, 4g silica sol, 4g nano-titanium di...
example 3
[0028] Add 50g of boric acid into 500mL of deionized water, stir at 60°C at 400r / min until the boric acid is completely dissolved, then add 120g of urea, continue stirring at 65°C for 40min, stir evenly, put it into a drying oven, and evaporate at 60°C To dryness, the composite material was obtained. The composite material was placed in a muffle furnace, heated to 950°C for 6 hours in a nitrogen atmosphere, and calcined for 6 hours. After cooling to room temperature, the calcined product was washed with 1% hydrochloric acid for 3 times, and then dehydrated with ethanol. Wash the calcined product 3 times, transfer it to a drying oven after washing, and dry it to a constant weight at 60°C to obtain nano-flaky boron nitride. Take 25g of phosphoric acid, add 100mL of deionized water, and stir and heat at 400r / min to 60 ℃, add 10g aluminum hydroxide, continue to stir for 20min, add 15g magnesium oxide, 2g nano-flaky boron nitride, 5g silica sol, 5g nano-titanium dioxide after coolin...
PUM
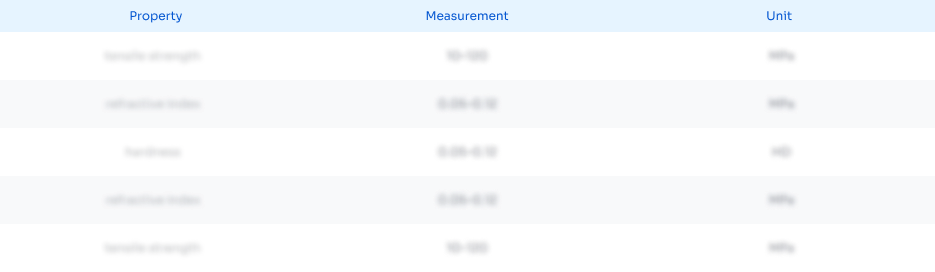
Abstract
Description
Claims
Application Information

- R&D
- Intellectual Property
- Life Sciences
- Materials
- Tech Scout
- Unparalleled Data Quality
- Higher Quality Content
- 60% Fewer Hallucinations
Browse by: Latest US Patents, China's latest patents, Technical Efficacy Thesaurus, Application Domain, Technology Topic, Popular Technical Reports.
© 2025 PatSnap. All rights reserved.Legal|Privacy policy|Modern Slavery Act Transparency Statement|Sitemap|About US| Contact US: help@patsnap.com