Composite current collector and preparation method thereof
A current collector and drying technology, applied in the field of composite current collector and its preparation, can solve the problems of limited contact resistance reduction ability, lower product qualification rate, large area drop of pole pieces, etc., and achieves not easy falling off and long cycle life , the effect of uniform pore size distribution
- Summary
- Abstract
- Description
- Claims
- Application Information
AI Technical Summary
Problems solved by technology
Method used
Image
Examples
Embodiment 1
[0040] 1. A method for preparing a composite current collector, comprising the steps of:
[0041] (1) Copper foil pretreatment: the copper foil is respectively cleaned in ethanol, acetone and deionized water in an ultrasonic cleaner to remove oil from the current collector, and dried in a vacuum drying oven at 80°C for 10 minutes.
[0042] (2) Coating carbon slurry: Prepare MOF-Co solution: take 0.3mmol potassium naphthalate and 0.3mmol cobalt nitrate, add 100ml of water, then put in the treated copper foil, and react at 80°C for 20h.
[0043] (3) Dry carbonization: first place the copper foil in step (2) in a vacuum drying oven, and dry it at 60° C. for 10 minutes, then place the copper foil in an argon atmosphere, and react at 600° C. for 10 hours.
[0044] (4) Pickling: Soak the copper foil in step (3) with 1 mol / L hydrochloric acid to obtain a copper foil with a carbon coating on the surface.
[0045] 2. A method for preparing a negative electrode material, comprising the...
Embodiment 2
[0048] 1. A method for preparing a composite current collector, comprising the steps of:
[0049] (1) Copper foil pretreatment: the copper foil is respectively cleaned in ethanol, acetone and deionized water in an ultrasonic cleaner to remove oil from the current collector, and dried in a vacuum drying oven at 60°C for 20 minutes.
[0050] (2) Coating carbon slurry: Prepare MOF-Co solution: take 0.3mmol potassium naphthalate and 0.3mmol cobalt nitrate, add 100ml of water, then put in the treated copper foil, and react at 100°C for 15h.
[0051] (3) Dry carbonization: first place the copper foil in step (2) in a vacuum drying oven, dry at 60°C for 10 minutes, then place the copper foil in an argon atmosphere, and react at 800°C for 5 hours.
[0052] (4) Pickling: Soak the copper foil in step (3) with 1 mol / L sulfuric acid to obtain a copper foil with a carbon coating on the surface.
[0053]2. A method for preparing a negative electrode material, comprising the following steps...
Embodiment 3
[0056] 1. A method for preparing a composite current collector, comprising the steps of:
[0057] (1) Copper foil pretreatment: the aluminum foil is respectively cleaned in ethanol, acetone and deionized water in an ultrasonic cleaner to remove oil from the current collector, and dried in a vacuum drying oven at 80°C for 10 minutes.
[0058] (2) Coating carbon slurry: configure MOF-Al solution, 0.01mol of aluminum nitrate nonahydrate and 0.01mol of terephthalic acid, add 65ml of N-N-dimethylformamide (DMF) to dissolve, put into aluminum foil, 220 ℃ heating 20h.
[0059] (3) Dry carbonization: first place the copper foil in step (2) in a vacuum drying oven, and dry it at 60° C. for 10 minutes, then place the copper foil in an argon atmosphere, and react at 600° C. for 10 hours.
[0060] (4) Pickling: Soak the aluminum foil in step (3) with 1 mol / L hydrochloric acid to obtain an aluminum foil with a carbon coating on the surface.
[0061] 2. A method for preparing a positive e...
PUM
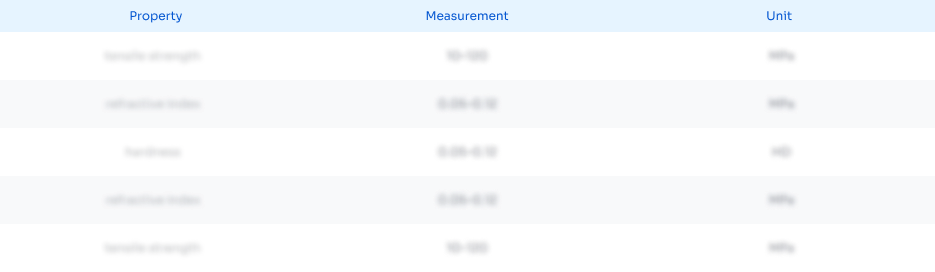
Abstract
Description
Claims
Application Information

- R&D
- Intellectual Property
- Life Sciences
- Materials
- Tech Scout
- Unparalleled Data Quality
- Higher Quality Content
- 60% Fewer Hallucinations
Browse by: Latest US Patents, China's latest patents, Technical Efficacy Thesaurus, Application Domain, Technology Topic, Popular Technical Reports.
© 2025 PatSnap. All rights reserved.Legal|Privacy policy|Modern Slavery Act Transparency Statement|Sitemap|About US| Contact US: help@patsnap.com