Epoxidized SBS, blocked macromolecular active amine toughening agent, preparation and application thereof to epoxy resin
A block polymer and epoxidation technology, applied in the field of epoxy resin toughening, can solve the problems of loss of flexural strength and flexural modulus, unfavorable wide application of products, loss of elastic modulus of materials, etc. Recovery of solvent and catalyst, effect of not easy to gel
- Summary
- Abstract
- Description
- Claims
- Application Information
AI Technical Summary
Problems solved by technology
Method used
Image
Examples
Embodiment 1
[0060] Embodiment 1, the synthesis of phosphotungstic peroxide heteropolyacid phase transfer catalyst
[0061] 7.56g tungstic acid and 35ml hydrogen peroxide (mass concentration 30%) were stirred and reacted at 65°C for 4 hours, the yellow color became colorless, stop the reaction, filter, and add 1.9ml phosphoric acid (mass volume concentration 40%) aqueous solution to the filtrate , after stirring for 15 minutes, add dropwise the dichloromethane solution of 132 grams of methyl trioctyl ammonium chloride (mass concentration 3.8%), after stirring for 15 minutes, leave to stand for layering, take the lower layer solution and carry out decompression at 45°C Distillation to obtain phosphotungstic peroxide heteropolyacid phase transfer catalyst, referred to as PWC, a colorless transparent viscous body.
[0062] The infrared spectrogram of the phosphotungstic peroxide heteropolyacid prepared in the present embodiment is as follows figure 2 shown.
Embodiment 2~3
[0063] Embodiment 2~3 is the preparation of epoxidized SBS
Embodiment 2
[0064] Embodiment 2, the preparation of epoxidized SBS (eSBS46)
[0065] Put 6.7 grams of SBS501 (produced by South Korean LG Chemical), 125.7 grams of dichloroethane, 0.67 grams of phosphotungstic acid phase transfer catalyst PWC, 15 ml of hydrogen peroxide (mass concentration 30%) and 10 ml of deionized water, at 60 ° C Stir for 3 hours, then add the reactant in normal hexane, let stand to separate and reclaim the upper layer product and the lower layer catalyst respectively, and the upper layer product is washed in a large amount of normal hexane and methanol, and vacuum-dried to obtain epoxidized SBS. The oxidation rate is 46%, referred to as eSBS46, the mass is 6.5 grams, and the yield is 97%. The reaction liquid in the lower layer is extracted and recovered with ethyl acetate to obtain 0.61 g of PWC catalyst, and the recovery rate is 91.4%.
PUM
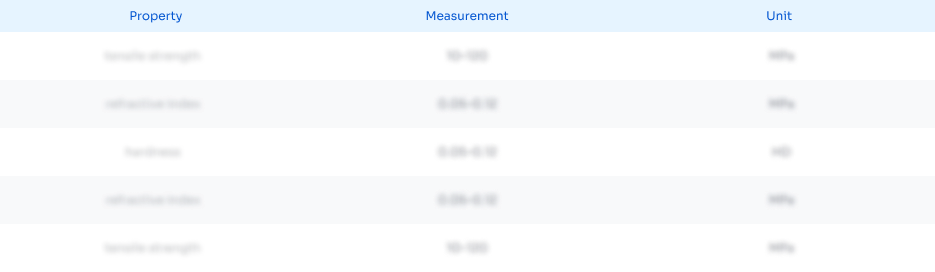
Abstract
Description
Claims
Application Information

- R&D Engineer
- R&D Manager
- IP Professional
- Industry Leading Data Capabilities
- Powerful AI technology
- Patent DNA Extraction
Browse by: Latest US Patents, China's latest patents, Technical Efficacy Thesaurus, Application Domain, Technology Topic, Popular Technical Reports.
© 2024 PatSnap. All rights reserved.Legal|Privacy policy|Modern Slavery Act Transparency Statement|Sitemap|About US| Contact US: help@patsnap.com