Microsphere powder of micron-scale highly cross-linked polymer and preparation method and application thereof
A high-crosslinking, polymer technology, applied in the field of polymer polymerization, can solve the problems of damage to the physical properties of the formed body, and achieve the effects of good sphericity, good transparency and low sulfate content
- Summary
- Abstract
- Description
- Claims
- Application Information
AI Technical Summary
Problems solved by technology
Method used
Image
Examples
Embodiment 1
[0044] 1. 0.2 part of sodium dodecyl diphenyl ether disulfonate and 0.8 part of polyethylene glycol are added to 492 parts of deionized water and dissolved completely to obtain sodium dodecyl diphenyl ether disulfonate and polyethylene glycol solution;
[0045] 2. Mix 38 parts of methyl methacrylate and 62 parts of ethylene glycol dimethacrylate, and stir until they are completely miscible;
[0046] 3. Add the mixed solution obtained in step 2 and 0.12 parts of potassium persulfate to the stabilizer solution obtained in step 1 at the same time, and obtain a pre-emulsion through high-speed dispersion;
[0047] 4. Add the pre-emulsion to a four-neck flask equipped with an electric stirrer, a thermometer and a condenser tube, turn on the stirrer, and raise the temperature to 50°C, feed nitrogen to keep the temperature constant, and keep the temperature for 4 hours. After the reaction is finished, a polymer emulsion is obtained.
[0048] 5. The polymer emulsion is spray-dried at...
Embodiment 2
[0050] 1. Mix 0.5 parts of sodium lauryl sulfate, 0.4g of polypropylene glycol and 0.4g of ECOSURF TM EH-9 was added to 389 parts of deionized water and dissolved completely to obtain a stabilizer solution;
[0051] 2. Mix 29 parts of methyl acrylate and 71 parts of allyl methacrylate, and stir until they dissolve completely;
[0052] 3. Add the mixed solution obtained in step 2 and 0.1 part of ammonium persulfate to the stabilizer solution obtained in step 1 at the same time, and obtain a pre-emulsion through high-speed dispersion;
[0053] 4. Add the pre-emulsion to a four-necked flask equipped with an electric stirrer, a thermometer and a condenser tube, turn on the stirrer, and raise the temperature to 55°C, feed nitrogen to keep the temperature constant, keep the temperature for 8 hours, and the reaction is over. A polymer emulsion is obtained.
[0054] 5. The polymer emulsion is spray-dried at a temperature of 130° C. to 160° C. to finally obtain a powder of micron-siz...
Embodiment 3
[0056] 1. Add 0.1 part of sodium dodecyl sulfonate and 1 part of polyvinyl alcohol 1788 to 407 parts of deionized water and dissolve them completely to obtain a stabilizer solution;
[0057] 2. Mix 50 parts of styrene and 50 parts of trimethylolpropane trimethacrylate and stir until completely miscible;
[0058] 3. Add the mixed solution obtained in step 2 and 0.08 part of potassium persulfate to the stabilizer solution obtained in step 1 at the same time, and obtain a pre-emulsion through high-speed dispersion;
[0059] 4. Add the pre-emulsion to a four-necked flask equipped with an electric stirrer, a thermometer and a condenser tube, turn on the stirrer, and raise the temperature to 80°C, feed nitrogen to keep the temperature constant, keep the temperature for 4 hours, and the reaction is over. A polymer emulsion is obtained.
[0060] 5. The polymer emulsion is spray-dried at a temperature of 120° C. to 150° C. to finally obtain a powder of micron-sized highly cross-linked...
PUM
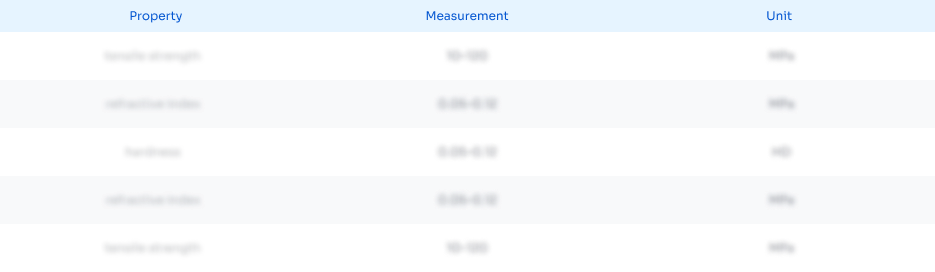
Abstract
Description
Claims
Application Information

- R&D
- Intellectual Property
- Life Sciences
- Materials
- Tech Scout
- Unparalleled Data Quality
- Higher Quality Content
- 60% Fewer Hallucinations
Browse by: Latest US Patents, China's latest patents, Technical Efficacy Thesaurus, Application Domain, Technology Topic, Popular Technical Reports.
© 2025 PatSnap. All rights reserved.Legal|Privacy policy|Modern Slavery Act Transparency Statement|Sitemap|About US| Contact US: help@patsnap.com