A short-process steelmaking process of biomass iron-containing agglomerates and a method for producing stainless steel
A biomass and short-process technology, applied in the field of iron and steel metallurgy, can solve the problems of short-process steelmaking of biomass iron-containing agglomerates, etc., to improve energy utilization efficiency, improve gasification yield, and promote biomass gasification. Effect
- Summary
- Abstract
- Description
- Claims
- Application Information
AI Technical Summary
Problems solved by technology
Method used
Image
Examples
Embodiment 1
[0046] In the process of previous research, the application has made a series of breakthroughs, and has improved the gasification yield and the quality of direct reduced iron, with significant progress, and applied for an invention patent (2017101469513-a biomass gasification and direct reduction The iron co-production method and additives used, the application date is: 2016-03-13). In the process of continuing research, the applicant further adopted the short-process steelmaking process of biomass iron-containing agglomerates, and prepared high-quality molten steel, which greatly shortened the process of iron and steel smelting and improved the efficiency of smelting.
[0047] The applicant conducted further in-depth research, and creatively proposed that no binder is added to the iron-containing agglomerate, and the modified biomass and iron-containing raw materials are hot-pressed at high temperature to improve the iron-containing agglomerate. strength, avoiding the crushin...
Embodiment 2
[0086] The basic content of this embodiment is the same as embodiment 1, the difference is:
[0087] The additive in the step 1 is composed of sodium carbonate, laterite nickel ore, dolomite, plant ash and chromium slag; the mass percentage of each component is: sodium carbonate: 15%, laterite nickel ore: 30%, dolomite: 30%, Plant ash: 15%, chromium residue: 10%. Described chromium slag chemical composition mass percent is as follows: SiO 2 : 28%, Al 2 o 3 : 8%, CaO: 30%, MgO: 15%, Fe 2 o 3 : 10%, Cr 2 o 6 : 0.8% and Na 2 Cr 2 o 7 : 1%, the rest are impurities. The metallization rate of direct reduced iron, biomass gasification yield and tar yield were detected after the reaction. The experimental results are recorded in Table 1. It should be noted that the modified solution is an alkaline solution, the alkaline solution is a KOH solution, and the mass concentration of the KOH solution is 3%. On the one hand, the chromium slag can effectively reduce the chromium s...
Embodiment 3
[0091] The basic content of this embodiment is the same as embodiment 1, the difference is:
[0092] The iron ore concentrate of described step 1 is made up of Hayangdi, Tubarang powder, Canadian fine powder, Kazakhstan powder and Jinbuba powder, and the composition of ore is as shown in table 2, and the mass percent of various mineral powders is: Hayangdi: 10%, Tubalang powder: 20%, Canadian fine powder: 40%, Kazakh powder: 15%, Jinbuba powder: 15%. The metallization rate of direct reduced iron, biomass gasification yield, and tar yield were detected after the reaction. The experimental results are recorded in Table 1.
[0093] Table 2 Mineral powder composition (wt / %)
[0094]
[0095] It is worth noting that the modified solution is an alkaline solution, and the alkaline solution is NaOH and Ca(OH) 2 The mixed solution, the mass concentration of the mixed solution is 4%, NaOH and Ca(OH) 2 The mass ratio is 4:1.
[0096]The second step: electric furnace smelting: hot ...
PUM
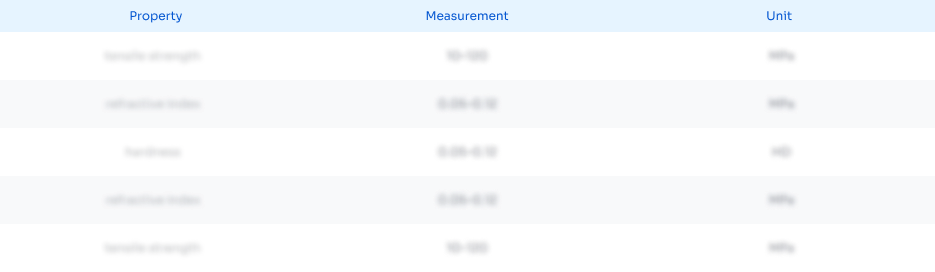
Abstract
Description
Claims
Application Information

- Generate Ideas
- Intellectual Property
- Life Sciences
- Materials
- Tech Scout
- Unparalleled Data Quality
- Higher Quality Content
- 60% Fewer Hallucinations
Browse by: Latest US Patents, China's latest patents, Technical Efficacy Thesaurus, Application Domain, Technology Topic, Popular Technical Reports.
© 2025 PatSnap. All rights reserved.Legal|Privacy policy|Modern Slavery Act Transparency Statement|Sitemap|About US| Contact US: help@patsnap.com