Carbon-calcium aluminate composite powder and preparation method thereof
A technology of calcium aluminate and composite powder is applied in the fields of carbon-calcium aluminate composite powder and its preparation, and refractory pouring materials, which can solve the problems of poor oxidation resistance, poor dispersibility and poor wettability, and achieves improved dispersibility and convenience. Control, the effect of few influencing factors
- Summary
- Abstract
- Description
- Claims
- Application Information
AI Technical Summary
Problems solved by technology
Method used
Image
Examples
Embodiment 1
[0045] The present embodiment provides a kind of preparation method of carbon-calcium aluminate composite powder, and this method is raw material with alumina powder (purity ≥ 99.0%) and calcium stearate (purity ≥ 99.0%), by mass parts, Made from the following raw materials: Calcium Stearate 85.61%, Aluminum Oxide 14.39%. Put the uniformly mixed raw materials in a corundum crucible, bury carbon in a resistance furnace for sintering, raise the temperature to 1600°C, and keep it at 1600°C for 4 hours. After the furnace temperature drops to room temperature, turn off the power and open the furnace door to take out the materials. The fired material is crushed and ground to obtain carbon-calcium aluminate composite powder.
[0046] Specifically, the heating rate of the heating process is carried out in the following manner:
[0047] Below 700°C, the heating rate is 5°C / min;
[0048] From 700°C to 1100°C, the heating rate is 4°C / min;
[0049] From 1100°C to 1200°C, the heating ra...
Embodiment 2
[0056] The present embodiment provides a kind of preparation method of carbon-calcium aluminate composite powder, and this method is raw material with aluminum oxide powder (purity ≥ 99.0%) and calcium gluconate (purity ≥ 99.0%), by mass parts. Made from the following raw materials: Calcium Gluconate 80.8%, Aluminum Oxide 19.2%. Put the uniformly mixed raw materials in a corundum crucible, in a tube furnace, under the protection of nitrogen, raise the temperature to 1400°C, keep it at 1400°C for 3 hours, after the furnace temperature drops to room temperature, turn off the power and open the furnace door to take out the materials . The fired material is crushed and ground to obtain carbon-calcium aluminate composite powder.
[0057] Specifically, the heating process is the same as in Example 1.
[0058] The carbon-calcium aluminate composite powder prepared in this example is detected and analyzed by XRD and Raman spectroscopy, the results can be found in image 3 and Fig...
Embodiment 3
[0062] The present embodiment provides a kind of preparation method of carbon-calcium aluminate composite powder, and this method is raw material with aluminum oxide powder (purity ≥ 99.0%) and calcium gluconate (purity ≥ 99.0%), by mass parts. Made from the following raw materials: Calcium Gluconate 80.8%, Aluminum Oxide 19.2%. Put the uniformly mixed raw materials in a corundum crucible, in a tube furnace, under the protection of argon, raise the temperature to 1200°C, keep it at 1200°C for 4 hours, after the furnace temperature drops to room temperature, turn off the power and open the furnace door to remove the materials take out. The fired material is crushed and ground to obtain carbon-calcium aluminate composite powder.
[0063] Specifically, the heating process is the same as in Example 1.
[0064] The carbon-calcium aluminate composite powder that makes in the present embodiment is detected and analyzed with XRD and Raman spectrum, and its result and image 3 and ...
PUM
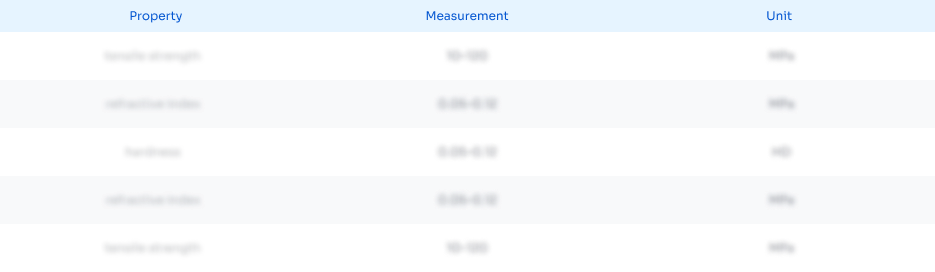
Abstract
Description
Claims
Application Information

- Generate Ideas
- Intellectual Property
- Life Sciences
- Materials
- Tech Scout
- Unparalleled Data Quality
- Higher Quality Content
- 60% Fewer Hallucinations
Browse by: Latest US Patents, China's latest patents, Technical Efficacy Thesaurus, Application Domain, Technology Topic, Popular Technical Reports.
© 2025 PatSnap. All rights reserved.Legal|Privacy policy|Modern Slavery Act Transparency Statement|Sitemap|About US| Contact US: help@patsnap.com