Cu-Ni-Si-Co-Ti-RE copper alloy and preparation method thereof
A cu-ni-si-co-ti-re, copper alloy technology, applied in the field of copper alloy materials, can solve the problems of high environmental protection requirements, long production process flow, high production cost, reduce macro and micro segregation, The effect of reducing the depth of the liquid cavity and improving the shape
- Summary
- Abstract
- Description
- Claims
- Application Information
AI Technical Summary
Problems solved by technology
Method used
Image
Examples
preparation example Construction
[0052] The preparation method of above-mentioned Cu-Ni-Si-Co-Ti-RE copper alloy specifically comprises the following steps:
[0053] (1) Melting and casting: first melt Cu, Ni, Co and Ti under the condition of covering calcined charcoal and electrode graphite powder, then add Si and 25% of all rare earth copper alloys, then remove slag, then heat up, and then degas , and then add 75% of the total rare earth copper alloy, then sample analysis, the temperature is controlled at 1240±10°C, then the composition is adjusted, and then the drawing is cast, and the temperature is controlled at 1215±10°C;
[0054] (2) Hot rolling: the hot rolling temperature is 800~1000℃, and the hot rolling time is 1~10h;
[0055] (3) Spray treatment: the finishing temperature of hot rolling is kept above 700°C;
[0056] (4) Face milling: the milling amount of the upper knife is 0.5mm, and the milling amount of the lower knife is 0.6mm;
[0057] (5) Rough rolling: the reduction rate of rough rolling ...
Embodiment 1
[0068] The alloy of the present invention is smelted using the following raw materials: electrolytic copper, pure nickel, pure cobalt, pure titanium, pure silicon, rare earth copper alloy; the composition of the alloy is shown in Example 1 of Table 1.
[0069] (1) Melting and casting: (bright wire copper 30% + recycled copper 70%) + nickel + cobalt + titanium + covering (calcined charcoal + electrode graphite powder) → melting + silicon + 25% rare earth copper alloy → slag removal → heating ( 1220°C)→degassing (10min)+75% rare earth copper alloy→sampling analysis (temperature control at 1240±10°C)→composition adjustment→drawing (temperature control at 1215±10°C);
[0070] (2) Hot rolling: the hot rolling temperature is 900°C, and the holding time is 6h;
[0071] (3) Spray treatment: the finishing temperature of hot rolling is 710°C;
[0072] (4) Face milling: upper knife 0.5mm, lower knife 0.6mm;
[0073] (5) Rough rolling: the reduction rate is 50%;
[0074] (6) Bell jar a...
Embodiment 2
[0083] The alloy of the present invention is smelted using the following raw materials: electrolytic copper, pure nickel, pure cobalt, pure titanium, pure silicon, rare earth copper alloy; the composition of the alloy is shown in Example 2 of Table 1.
[0084] (1) Melting and casting: (bright wire copper 30% + recycled copper 70%) + nickel + cobalt + titanium + covering (calcined charcoal + electrode graphite powder) → melting + silicon + 25% rare earth copper alloy → slag removal → heating ( 1220°C)→degassing (10min)+75% rare earth copper alloy→sampling analysis (temperature control at 1240±10°C)→composition adjustment→drawing (temperature control at 1215±10°C);
[0085] (2) Hot rolling: the hot rolling temperature is 920°C, and the holding time is 6h;
[0086] (3) Spray treatment: the finishing temperature of hot rolling is 700°C;
[0087] (4) Face milling: upper knife 0.5mm, lower knife 0.6mm;
[0088] (5) Rough rolling: the reduction rate is 60%;
[0089] (6) Bell jar ann...
PUM
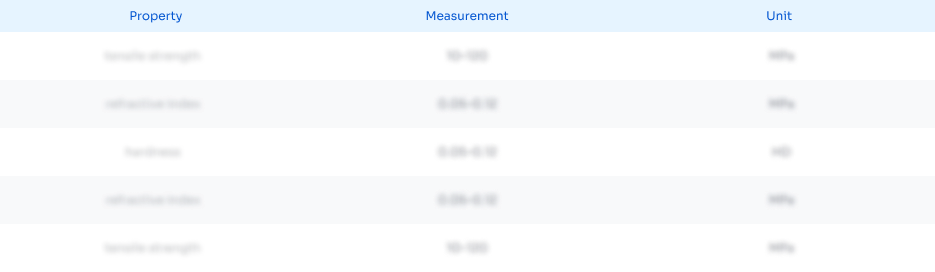
Abstract
Description
Claims
Application Information

- R&D
- Intellectual Property
- Life Sciences
- Materials
- Tech Scout
- Unparalleled Data Quality
- Higher Quality Content
- 60% Fewer Hallucinations
Browse by: Latest US Patents, China's latest patents, Technical Efficacy Thesaurus, Application Domain, Technology Topic, Popular Technical Reports.
© 2025 PatSnap. All rights reserved.Legal|Privacy policy|Modern Slavery Act Transparency Statement|Sitemap|About US| Contact US: help@patsnap.com