Anti-creeping cable material for automobile wire and preparation method of cable material
A wire and cable material and anti-creep technology, which is applied in the field of creep-resistant automotive wire and cable material and its preparation, can solve the problems of poor creep resistance and unsatisfactory performance, achieve good high temperature resistance, improve creep resistance, and creep resistance good denaturing effect
- Summary
- Abstract
- Description
- Claims
- Application Information
AI Technical Summary
Problems solved by technology
Method used
Image
Examples
Embodiment Construction
[0012] A creep-resistant automotive wire and cable material, made of the following raw materials by weight (kg): polyethylene 70, neopentyl glycol dibenzoate 15, ultra-fine whisker silicon 20, aluminum distearate 6, Atomized magnesium alloy powder 12, metallocene cycloolefin polymer 30, river sand 14, tuff 16, polyetherimide 22, solid paraffin 7, copper mine tailings 17, boron mud 8, diisodecyl adipate 12. Magnesium reduction slag 10. Tetraacicular zinc oxide whiskers 9.
[0013] A method for preparing a creep-resistant automotive wire and cable material, comprising the following steps:
[0014] (1) Mix river sand, tuff, copper ore tailings, boron mud, and magnesium reduction slag evenly, pulverize, sieve, then heat and melt to form a molten liquid, fully stir it, put it into clean water for water quenching, and dry it. Crushing, sieving, 2500r / min wet ball milling for 2 hours, drying, and then using argon with a flow rate of 40L / min as the carrier gas to send the dried powde...
PUM
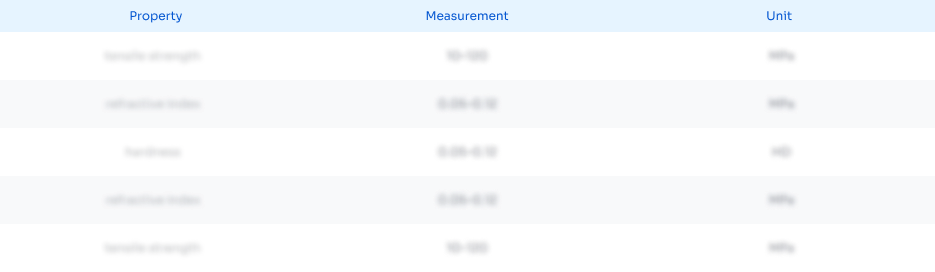
Abstract
Description
Claims
Application Information

- R&D Engineer
- R&D Manager
- IP Professional
- Industry Leading Data Capabilities
- Powerful AI technology
- Patent DNA Extraction
Browse by: Latest US Patents, China's latest patents, Technical Efficacy Thesaurus, Application Domain, Technology Topic, Popular Technical Reports.
© 2024 PatSnap. All rights reserved.Legal|Privacy policy|Modern Slavery Act Transparency Statement|Sitemap|About US| Contact US: help@patsnap.com