Making method of scratch-resistant thin film
A production method and film technology, applied in the field of scratch-resistant film production, can solve the problems of high molecular chain rigidity, good weather resistance, decreased mechanical strength, etc., and achieve a simple preparation method, good scratch resistance, and protected appearance quality. Effect
- Summary
- Abstract
- Description
- Claims
- Application Information
AI Technical Summary
Problems solved by technology
Method used
Examples
Embodiment 1
[0022] In an embodiment of the present invention, a method for manufacturing an anti-scratch film includes the following steps:
[0023] 1) Weigh the raw materials; the raw materials include by weight: 85 parts of oily polyurethane, 40 parts of PC resin, 40 parts of PE resin, 5 parts of curing agent, 1 part of anti-scratch agent, 0.2 parts of drier, vinyl bis stearamide 0.1 part, 0.1 part of slip agent, 65 parts of organic solvent. The curing agent is isocyanate. The drier is a cobalt soap drier. The slippery agent is erucamide. The organic solvent is a mixture of butanone and ethyl ester.
[0024] 2) Bake the PC resin at 95°C for 4 hours, then mix it with oily polyurethane, PE resin, curing agent, anti-scratch agent, drier, vinyl bisstearamide, slip agent, organic solvent, pour into the reactor and stirred at 120rpm for 8min.
[0025] 3) Raise the temperature in the reactor to 280°C, lower the pressure to below 150Pa, react under this condition for 1.5h to obtain a polym...
Embodiment 2
[0028] In an embodiment of the present invention, a method for manufacturing an anti-scratch film includes the following steps:
[0029] 1) Weigh the raw materials; the raw materials include by weight: 115 parts of oily polyurethane, 90 parts of PC resin, 90 parts of PE resin, 35 parts of curing agent, 18 parts of anti-scratch agent, 3 parts of drier, vinyl bis stearamide 4 parts, 4 parts of slip agent, 95 parts of organic solvent. The curing agent is isocyanate. The drier is a cobalt soap drier. The slippery agent is erucamide. The organic solvent is a mixture of butanone and ethyl ester.
[0030] 2) Bake the PC resin at 120°C for 8 hours, then mix it with oily polyurethane, PE resin, curing agent, anti-scratch agent, drier, vinyl bis stearamide, slip agent, organic solvent, pour into the reactor and stirred at 250rpm for 30min.
[0031] 3) Raise the temperature in the reactor to 320° C., lower the pressure to below 150 Pa, react under this condition for 4 hours to obtai...
Embodiment 3
[0034] In an embodiment of the present invention, a method for manufacturing an anti-scratch film includes the following steps:
[0035] 1) Weigh the raw materials; the raw materials include by weight: 90 parts of oily polyurethane, 45 parts of PC resin, 45 parts of PE resin, 10 parts of curing agent, 1 part of anti-scratch agent, 0.4 part of drier, vinyl bis stearamide 0.3 parts, 0.1 parts of slip agent, 70 parts of organic solvent. The curing agent is isocyanate. The drier is a cobalt soap drier. The slippery agent is erucamide. The organic solvent is a mixture of butanone and ethyl ester.
[0036] 2) Bake the PC resin at 100°C for 4.5 hours, then mix it with oily polyurethane, PE resin, curing agent, scratch-resistant agent, drier, vinyl bis stearamide, slip agent, and organic solvent, Pour into the reaction kettle and stir at 150rpm for 10min.
[0037] 3) Raise the temperature in the reactor to 290°C and lower the pressure to below 120Pa, and react under these conditi...
PUM
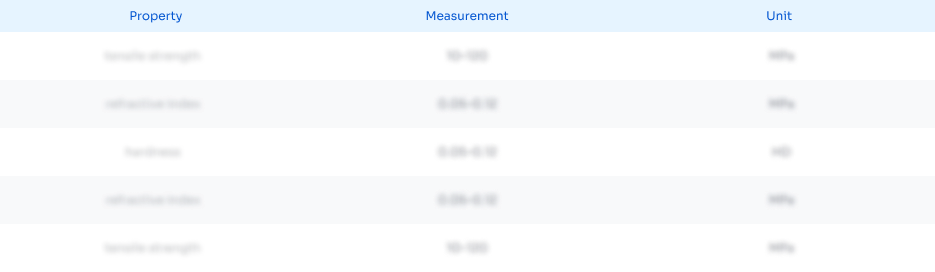
Abstract
Description
Claims
Application Information

- R&D
- Intellectual Property
- Life Sciences
- Materials
- Tech Scout
- Unparalleled Data Quality
- Higher Quality Content
- 60% Fewer Hallucinations
Browse by: Latest US Patents, China's latest patents, Technical Efficacy Thesaurus, Application Domain, Technology Topic, Popular Technical Reports.
© 2025 PatSnap. All rights reserved.Legal|Privacy policy|Modern Slavery Act Transparency Statement|Sitemap|About US| Contact US: help@patsnap.com