Method for preparing protective film for glass
A glass protective film and modification technology, used in coatings, polycarbonate coatings, polyester coatings, etc., can solve the problems of general and unsatisfactory effects, and achieve convenient use, low cost, excellent strength and toughness. Effect
- Summary
- Abstract
- Description
- Claims
- Application Information
AI Technical Summary
Problems solved by technology
Method used
Image
Examples
Embodiment 1
[0022] A preparation method for glass protective film, comprising the steps of:
[0023] Step 1, preparation of modified silicone resin: 15.0 Kg of methyltrichlorosilane, 8.0 Kg of xylylsiloxane, 10.0 Kg of diphenyldichlorosilane, 3.0 Kg of polymethylmethacrylate, epoxypropylene Alcohol 5.0 Kg, tricresyl phosphate 5.0 Kg, polybutylene terephthalate 7.0 Kg and polycarbonate 5.0 Kg are put into the reactor, add deionized water 25.0 Kg, then add cumene hydroperoxide 2.5 Kg, heated in a water bath for reaction, after the reaction, modified silicone resin was obtained;
[0024] Step 2. Preparation of nanofillers: Take 1.8 Kg of nano-titanium oxide, 2.1 Kg of nano-montmorillonite, 0.7 Kg of tin oxide powder, 4.5 Kg of calcined kaolin and 1.1 Kg of zinc oxide powder into a mold and place in a high-temperature furnace Carry out high-temperature and high-pressure calcination in a medium temperature of 1180 ° C, a pressure of 330 MPa, and a calcination time of 4 hours. After cooling, i...
Embodiment 2
[0027] A preparation method for glass protective film, comprising the steps of:
[0028] Step 1, preparation of modified silicone resin: Methyltrichlorosilane 8.0Kg, xylylsiloxane 3.0 Kg, diphenyldichlorosilane 5.0 Kg, polymethyl methacrylate 1.0 Kg, epoxypropylene Alcohol 2.0Kg, tricresyl phosphate 1.0 Kg, polybutylene terephthalate 4.0 Kg and polycarbonate 3.0 Kg are put into the reactor, add deionized water 15.0 Kg, then add cumene hydroperoxide 1.5 Kg, heated in a water bath for reaction, after the reaction, modified silicone resin was obtained;
[0029] Step 2. Preparation of nanofillers: Take 1.9 Kg of nano-titanium oxide, 2.0 Kg of nano-montmorillonite, 0.6 Kg of tin oxide powder, 4.0 Kg of calcined kaolin and 1.1 Kg of zinc oxide powder, put them into a mold, and place in a high-temperature furnace Carry out high-temperature and high-pressure calcination in a medium temperature of 1180 ° C, a pressure of 300 MPa, and a calcination time of 4 hours. After cooling, it is...
Embodiment 3
[0032] A preparation method for glass protective film, comprising the steps of:
[0033] Step 1, preparation of modified silicone resin: 12.6 Kg of methyltrichlorosilane, 5.6 Kg of xylene siloxane, 8.3 Kg of diphenyldichlorosilane, 1.7 Kg of polymethylmethacrylate, epoxypropylene Alcohol 3.5 Kg, tricresyl phosphate 3.4 Kg, polybutylene terephthalate 5.7 Kg and polycarbonate 4.0 Kg are put into the reactor, add deionized water 19.5 Kg, then add diethylpropylbenzene peroxide 1.9 Kg, heated in a water bath for reaction, after the reaction, modified silicone resin was obtained;
[0034] Step 2. Preparation of nanofillers: Take 1.0Kg of nano-titanium oxide, 1.5 Kg of nano-montmorillonite, 0.5Kg of tin oxide powder, 2.5 Kg of calcined kaolin and 0.5Kg of zinc oxide powder, put them into a mold, and place in a high-temperature furnace Carry out high-temperature and high-pressure calcination in a medium temperature of 1080 ° C, a pressure of 220 MPa, and a calcination time of 5 hours...
PUM
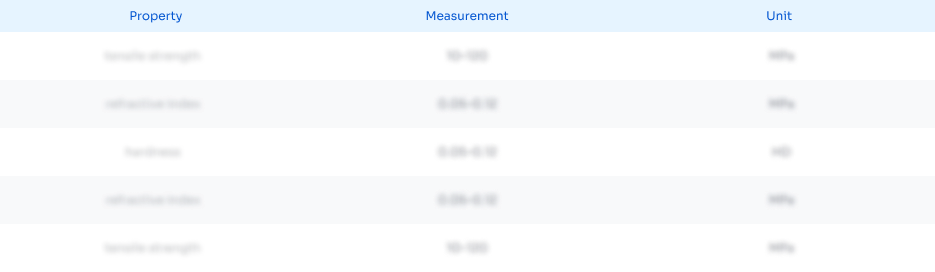
Abstract
Description
Claims
Application Information

- R&D
- Intellectual Property
- Life Sciences
- Materials
- Tech Scout
- Unparalleled Data Quality
- Higher Quality Content
- 60% Fewer Hallucinations
Browse by: Latest US Patents, China's latest patents, Technical Efficacy Thesaurus, Application Domain, Technology Topic, Popular Technical Reports.
© 2025 PatSnap. All rights reserved.Legal|Privacy policy|Modern Slavery Act Transparency Statement|Sitemap|About US| Contact US: help@patsnap.com