Method for preparing bone black high-cohesiveness wave-transparent coating powder
A high-adhesion, coating powder technology, applied in the direction of coating, can solve the problems of low expansion rate, easy peeling or other destructive changes, destructive changes during use, and achieve the effect of simple preparation process
- Summary
- Abstract
- Description
- Claims
- Application Information
AI Technical Summary
Problems solved by technology
Method used
Examples
example 1
[0017] First collect fresh beef bones, wash them and dry them, crush them and sieve them to prepare 20-mesh beef bone particles, then stir and mix them with deionized water at a mass ratio of 1:10, and then heat them at 100°C Boil for 25 minutes, then let stand to cool to room temperature, filter and collect the boiled beef bone particles, dry naturally at 65°C for 6 hours, then grind and sieve to prepare 80-mesh beef bone powder; The bone powder was placed in a tube furnace, and then the air was vented with nitrogen. Under a nitrogen atmosphere, it was preheated at 120°C for 25 minutes, and then the temperature was raised to 550°C at a rate of 10°C / min. Cool to room temperature, collect bone charcoal and grind and sieve to prepare 120 mesh bone charcoal powder; by weight, weigh 10 parts of stearyl methacrylate and 15 parts of methoxypolyethylene glycol methacrylic acid Esters, 3 parts of ethylene glycol dimethacrylate, 2 parts of 1,4-butanediol, 1 part of ammonium persulfate ...
example 2
[0020] First collect fresh bovine bone, wash it and dry it, crush it and sieve it to prepare 25-mesh bovine bone particles, then mix it with deionized water according to the mass ratio of 1:10, and then mix it with deionized water at 102°C Boil for 27 minutes, then let it cool down to room temperature, filter and collect the boiled beef bone particles, dry naturally at 72°C for 7 hours, then grind and sieve to prepare 85-mesh beef bone powder; the beef bone powder prepared above The bone powder was placed in a tube furnace, and then the air was vented with nitrogen to remove the air. Under a nitrogen atmosphere, it was preheated at 135°C for 27 minutes, then the temperature was raised to 575°C at a rate of 10°C / min, and then kept for 2 hours for carbonization. Cool to room temperature, collect bone charcoal and grind and sieve to prepare 125 mesh bone charcoal powder; by weight, weigh 12 parts of stearyl methacrylate, 17 parts of methoxypolyethylene glycol methacrylic acid Est...
example 3
[0023]First collect fresh beef bones, wash them and dry them, crush them and sieve them to prepare 30-mesh beef bone particles, then stir and mix them with deionized water at a mass ratio of 1:10, and then heat them at 105°C Boil for 30 minutes, then let stand to cool to room temperature, filter and collect the boiled beef bone particles, dry in the air and then dry at 80°C for 8 hours, then grind and sieve to prepare 90-mesh beef bone powder; The bone powder was placed in a tube furnace, and then the air was vented with nitrogen. Under a nitrogen atmosphere, it was preheated at 150°C for 30 minutes, then the temperature was raised to 600°C at a rate of 10°C / min, and then carbonized for 2 hours. Cool to room temperature, collect bone charcoal and grind and sieve to prepare 130 mesh bone charcoal powder; by weight, weigh 15 parts of stearyl methacrylate, 20 parts of methoxypolyethylene glycol methacrylic acid Esters, 5 parts of ethylene glycol dimethacrylate, 3 parts of 1,4-but...
PUM
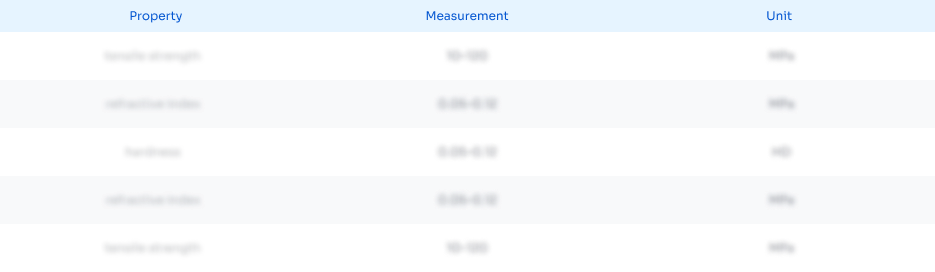
Abstract
Description
Claims
Application Information

- R&D
- Intellectual Property
- Life Sciences
- Materials
- Tech Scout
- Unparalleled Data Quality
- Higher Quality Content
- 60% Fewer Hallucinations
Browse by: Latest US Patents, China's latest patents, Technical Efficacy Thesaurus, Application Domain, Technology Topic, Popular Technical Reports.
© 2025 PatSnap. All rights reserved.Legal|Privacy policy|Modern Slavery Act Transparency Statement|Sitemap|About US| Contact US: help@patsnap.com