Casting-forging composite plastic forming process for brake disc
A technology of plastic forming and brake discs, which is applied in the manufacturing industry, can solve the problems of difficult forming of brake discs and unsatisfactory mechanical properties, and achieve the effects of high internal temperature, improved comprehensive mechanical properties, and reduced secondary heating
- Summary
- Abstract
- Description
- Claims
- Application Information
AI Technical Summary
Problems solved by technology
Method used
Examples
Embodiment 1
[0031] The casting-forging composite plastic forming process of the brake disc of the present invention comprises the following steps,
[0032] Step 1: metal smelting;
[0033] Metal smelting includes the selection of raw materials to ensure that the alloy composition of the raw materials is: carbon 0.25%, silicon 0.032%, manganese 0.57%, vanadium 0.27%, chromium 1.27%, nickel 0.32%, molybdenum 0.72%, and the rest is iron.
[0034] Step 2: Composition analysis;
[0035] Carry out component analysis on the smelted raw materials, smelt the raw materials at 1500-1750°C, check the composition of the melt by sampling after half an hour of smelting, and supplement the components with reduced components, and continue smelting for half an hour after the supplement is completed;
[0036] Step 3: Before pouring, spray a special coating on the cavity of the casting mold, dry and cure it, and then perform an overall preheating treatment. The preheating method is far-infrared heating, and...
Embodiment 2
[0048] The casting-forging composite plastic forming process of the brake disc of the present invention comprises the following steps,
[0049] Step 1: metal smelting;
[0050] Metal smelting includes the selection of raw materials to ensure that the alloy composition of the raw materials is: carbon 0.31%, silicon 0.038%, manganese 0.73%, vanadium 0.33%, chromium 1.33%, nickel 0.38%, molybdenum 0.78%, and the rest is iron;
[0051] Step 2: Composition analysis;
[0052] Carry out component analysis on the smelted raw materials, smelt the raw materials at 1500-1750°C, check the composition of the melt by sampling after half an hour of smelting, and supplement the components with reduced components, and continue smelting for half an hour after the supplement is completed;
[0053] Step 3: Before pouring, spray a special coating on the cavity of the casting mold, dry and cure it, and then perform an overall preheating treatment. The preheating method is far-infrared heating, and...
Embodiment 3
[0065] The casting-forging composite plastic forming process of the brake disc of the present invention comprises the following steps,
[0066] Step 1: metal smelting;
[0067] Metal smelting includes the selection of raw materials to ensure that the alloy composition of the raw materials is: carbon 0.28%, silicon 0.035%, manganese 0.68%, vanadium 0.3%, chromium 1.3%, nickel 0.35%, molybdenum 0.75%, and the rest is iron.
[0068] Step 2: Composition analysis;
[0069] Carry out component analysis on the smelted raw materials, smelt the raw materials at 1500-1750°C, check the composition of the melt by sampling after half an hour of smelting, and supplement the components with reduced components, and continue smelting for half an hour after the supplement is completed;
[0070] Step 3: Before pouring, spray a special coating on the cavity of the casting mold, dry and cure it, and then perform an overall preheating treatment. The preheating method is far-infrared heating, and t...
PUM
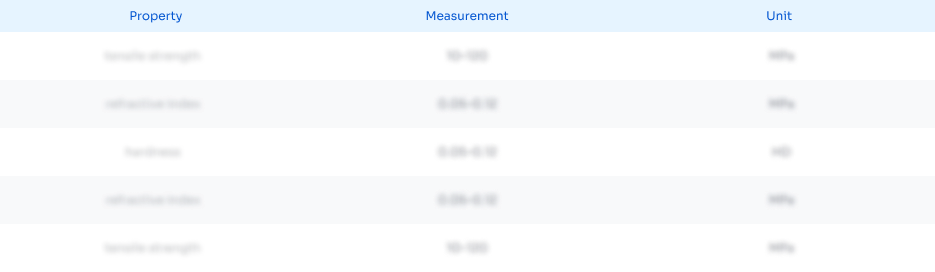
Abstract
Description
Claims
Application Information

- Generate Ideas
- Intellectual Property
- Life Sciences
- Materials
- Tech Scout
- Unparalleled Data Quality
- Higher Quality Content
- 60% Fewer Hallucinations
Browse by: Latest US Patents, China's latest patents, Technical Efficacy Thesaurus, Application Domain, Technology Topic, Popular Technical Reports.
© 2025 PatSnap. All rights reserved.Legal|Privacy policy|Modern Slavery Act Transparency Statement|Sitemap|About US| Contact US: help@patsnap.com