3D printing flame-retardant antibacterial composite material
A composite material, 3D printing technology, applied in the direction of additive processing, can solve the problem of single performance, achieve the effect of superior flame retardant and improve product performance
- Summary
- Abstract
- Description
- Claims
- Application Information
AI Technical Summary
Problems solved by technology
Method used
Image
Examples
Embodiment 1
[0016] The 3D printing flame-retardant and antibacterial composite material in this embodiment is composed of the following components in parts by mass: 10 parts of urea-formaldehyde resin, 8 parts of perchlorethylene resin, 8 parts of fluorosilicone rubber, 6 parts of N-methylpyrrolidone, 8 parts of diethylene glycol monoethyl ether, 8 parts of soybean oil, 6 parts of methyl isobutyl carbinol, 8 parts of methyl benzoate, 8 parts of antimicrobial peptides, 6 parts of p-chloro-m-xylenol, 6 parts of eucalyptus oil, 6 parts of biguanide trioctylbenzene sulfonate, 8 parts of sodium hydrosulfide, 6 parts of porcelain powder, 4 parts of titanium nitride powder, 8 parts of sodium dihydrogen phosphate, 6 parts of barium sulfate powder, 4 parts of molybdenum disulfide powder, 6 parts of lead iodate powder, 4 parts of praseodymium oxide powder, 4 parts of diethyl ethyl phosphonate, 6 parts of nano-zinc oxide, 6 parts of hexabromobenzene, 6 parts of acrylonitrile, 6 parts of sodium dodecy...
Embodiment 2
[0022] The 3D printing flame-retardant and antibacterial composite material in this embodiment is composed of the following components in parts by mass: 12 parts of urea-formaldehyde resin, 10 parts of perchlorethylene resin, 10 parts of fluorosilicone rubber, 8 parts of N-methylpyrrolidone, 10 parts of diethylene glycol monoethyl ether, 10 parts of soybean oil, 8 parts of methyl isobutyl carbinol, 10 parts of methyl benzoate, 10 parts of antimicrobial peptides, 8 parts of p-chloro-m-xylenol, 8 parts of eucalyptus oil, 8 parts of biguanide trioctylbenzene sulfonate, 10 parts of sodium hydrosulfide, 8 parts of porcelain powder, 6 parts of titanium nitride powder, 10 parts of sodium dihydrogen phosphate, 8 parts of barium sulfate powder, 6 parts of molybdenum disulfide powder, 8 parts of lead iodate powder, 6 parts of praseodymium oxide powder, 6 parts of diethyl ethyl phosphonate, 8 parts of nano-zinc oxide, 8 parts of hexabromobenzene, 8 parts of acrylonitrile, 8 parts of sodiu...
Embodiment 3
[0028] The 3D printing flame-retardant and antibacterial composite material in this embodiment is composed of the following components by mass: 14 parts of urea-formaldehyde resin, 12 parts of perchlorethylene resin, 12 parts of fluorosilicone rubber, 10 parts of N-methylpyrrolidone, 12 parts of diethylene glycol monoethyl ether, 12 parts of soybean oil, 10 parts of methyl isobutyl carbinol, 12 parts of methyl benzoate, 12 parts of antimicrobial peptides, 10 parts of p-chloro-m-xylenol, 10 parts of eucalyptus oil, 10 parts of biguanide trioctylbenzene sulfonate, 12 parts of sodium hydrosulfide, 10 parts of porcelain powder, 8 parts of titanium nitride powder, 12 parts of sodium dihydrogen phosphate, 10 parts of barium sulfate powder, 8 parts of molybdenum disulfide powder, 10 parts of lead iodate powder, 8 parts of praseodymium oxide powder, 8 parts of diethyl ethyl phosphonate, 10 parts of nano-zinc oxide, 10 parts of hexabromobenzene, 10 parts of acrylonitrile, 10 parts of so...
PUM
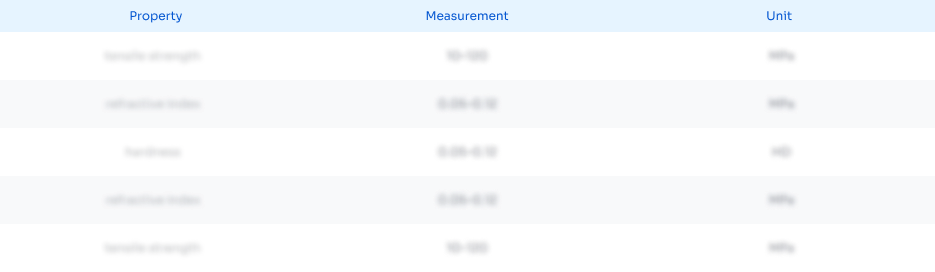
Abstract
Description
Claims
Application Information

- R&D
- Intellectual Property
- Life Sciences
- Materials
- Tech Scout
- Unparalleled Data Quality
- Higher Quality Content
- 60% Fewer Hallucinations
Browse by: Latest US Patents, China's latest patents, Technical Efficacy Thesaurus, Application Domain, Technology Topic, Popular Technical Reports.
© 2025 PatSnap. All rights reserved.Legal|Privacy policy|Modern Slavery Act Transparency Statement|Sitemap|About US| Contact US: help@patsnap.com