Low-alloy steel high in strength and toughness performance and preparing method of low-alloy steel
A low-alloy steel and high-performance technology, applied in the field of iron and steel metallurgy, can solve problems that affect the qualified rate of finished products and profit margins, high energy consumption in production and manufacturing, and long manufacturing processes for high-performance steel products.
- Summary
- Abstract
- Description
- Claims
- Application Information
AI Technical Summary
Problems solved by technology
Method used
Image
Examples
preparation example Construction
[0043] The present invention also provides a method for preparing the above-mentioned low alloy steel with high strength and toughness, which includes the following steps:
[0044] a) The smelted molten steel with the required composition is continuously cast into 200-300mm thick slabs through continuous casting equipment, the superheat is controlled at 15-30℃, the drawing speed is 0.8-1.2m / min, and the straightening section casting The surface temperature of the blank is controlled at 900-950℃, and the center temperature is 1300-1480℃;
[0045] b) After the billet is discharged, it is quickly descaled and cooled on-line, and then uses the high temperature of the core of the cast billet to achieve a uniform temperature return;
[0046] c) After the surface temperature of the slab rises to 1050~1100℃, the slab is sent to the subsequent rolling mill for direct rough rolling, and the thickness of the intermediate slab is controlled to be 3-4 times the thickness of the finished product; ...
Embodiment 1
[0058] The molten steel that has been smelted, the Nb+Ti addition in the steel is 0.032%, the gas element N content is 42ppm and the composition has reached the Q460E requirements is continuously cast into a 250mm billet through the continuous casting equipment, and the pouring temperature, the drawing speed and the second With the cold water distribution system, the surface temperature of the straightening section of the cast slab detected is 913℃ and the core temperature is 1308℃.
[0059] Then, when the surface temperature of the cast slab is at 825°C, descaling and cooling starts, and when the cooling stops, the surface temperature of the slab is detected to be 610°C.
[0060] Then the cast slab is cut to length and waits for the billet to return to red on the roller table. When the surface temperature rises to 1055°C, direct rolling begins. The final rolling temperature of the rough rolling stage is 965°C and the thickness of the intermediate billet is 135mm. After the rough ro...
Embodiment 2
[0063] The finished smelted steel with Nb+Ti addition amount of 0.051%, gas element N content detected as 25ppm, and the composition has reached X80M requirements, is continuously cast into 300mm steel billets through continuous casting equipment, and the pouring temperature, drawing speed and two With the cold water distribution system, the surface temperature of the straightening section of the cast slab detected is 906℃, and the core temperature is 1475℃.
[0064] Then, when the surface temperature of the cast slab is at 890°C, descaling and cooling starts, and when the cooling stops, the surface temperature of the slab is detected to be 570°C.
[0065] Then the cast slab is cut to length and waits for the billet to return to red on the roller table. When the surface temperature rises to 1098℃, direct rolling begins. The final rolling temperature of the rough rolling stage is 1000℃ and the thickness of the intermediate slab is 100mm. After rough rolling, the stand rolls are conti...
PUM
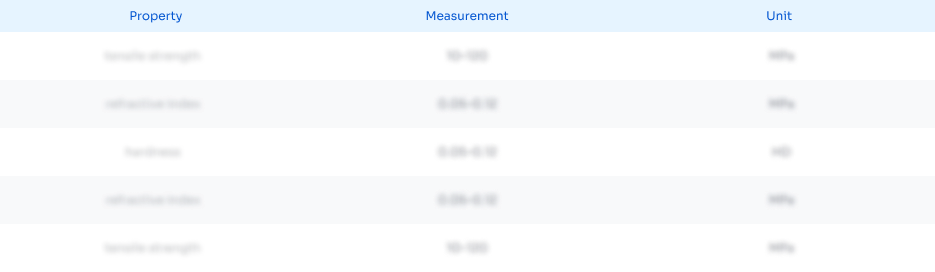
Abstract
Description
Claims
Application Information

- R&D
- Intellectual Property
- Life Sciences
- Materials
- Tech Scout
- Unparalleled Data Quality
- Higher Quality Content
- 60% Fewer Hallucinations
Browse by: Latest US Patents, China's latest patents, Technical Efficacy Thesaurus, Application Domain, Technology Topic, Popular Technical Reports.
© 2025 PatSnap. All rights reserved.Legal|Privacy policy|Modern Slavery Act Transparency Statement|Sitemap|About US| Contact US: help@patsnap.com