Method for preventing industrial robot from colliding with worker
A technology for industrial robots and workers, applied in two-dimensional position/channel control and other directions, it can solve the problems of industrial robot collision, unpredictable movement trajectory or movement trend, and difficulty in estimating the remaining time between industrial robots and workers, etc., to increase the possibility , to avoid the effect of harming workers
- Summary
- Abstract
- Description
- Claims
- Application Information
AI Technical Summary
Problems solved by technology
Method used
Image
Examples
Embodiment Construction
[0052] Specific embodiments of the present invention will be described in detail below in conjunction with the accompanying drawings.
[0053] The method for avoiding industrial robots colliding with workers in the present invention mainly uses four units, which are respectively a vision unit, a worker's motion characteristic recognition unit, a safety protection area calculation unit, and an industrial robot target position and speed adjustment unit. The vision unit includes figure 1 The internal surveillance camera 3, the external surveillance camera 5 and the sensor array 4 in. figure 1 The working area 1 in is the site range set when the industrial robot 2 completes a certain task. The industrial robot 2 forms its protection area 21 in the work area 1, and the protection area 21 represents the space where workers may be collided by the joints of the industrial robot. Area, that is, the spatial area where each joint of the industrial robot will not collide with other object...
PUM
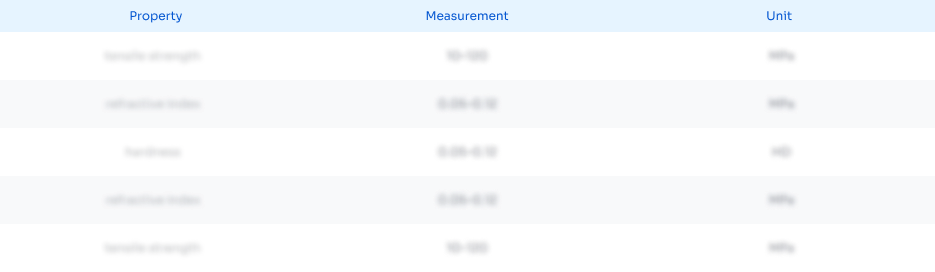
Abstract
Description
Claims
Application Information

- R&D
- Intellectual Property
- Life Sciences
- Materials
- Tech Scout
- Unparalleled Data Quality
- Higher Quality Content
- 60% Fewer Hallucinations
Browse by: Latest US Patents, China's latest patents, Technical Efficacy Thesaurus, Application Domain, Technology Topic, Popular Technical Reports.
© 2025 PatSnap. All rights reserved.Legal|Privacy policy|Modern Slavery Act Transparency Statement|Sitemap|About US| Contact US: help@patsnap.com