Center porosity control method for 35CrMo round blooms with cross section diameter being 280 mm
A technology of center loosening and control method, applied in the manufacture of converters, etc., can solve the problems of slow solidification and cooling, small specific surface area, affecting product quality, etc., achieve uniform composition and temperature of molten steel, improve purity, and increase density Effect
- Summary
- Abstract
- Description
- Claims
- Application Information
AI Technical Summary
Problems solved by technology
Method used
Examples
Embodiment
[0025] A steelmaking plant adopts 120t converter smelting→LF furnace refining→RH refining→six-machine and six-strand casting machine to produce 35CrMo round tube by continuous casting with φ280mm section. At the end of converter blowing, the end point carbon is controlled at 0.15%, the end point phosphorus is 0.009%, the end point temperature is controlled at 1675°C, and the ladle slag thickness is controlled at 56mm.
[0026] When the molten steel reaches the LF refining furnace, the molten steel fluctuates slightly for argon blowing, and there is no major overturning phenomenon. The mass percentage of Als out of the station is controlled at 0.041%. After the refining is completed, the molten steel is softly blown with argon. After the treatment, the fixed temperature is 1611°C, the outbound [S] of LF is 0.006%, and [S]+[P] is 0.020%.
[0027] After the molten steel arrives at the station, the RH refining argon blowing argon flow rate is controlled at 1350NL / min, the processi...
PUM
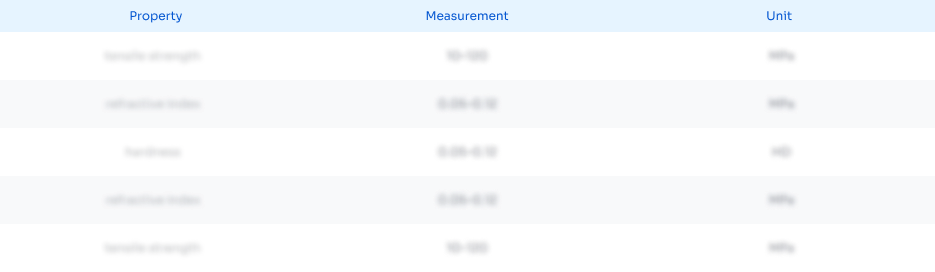
Abstract
Description
Claims
Application Information

- R&D Engineer
- R&D Manager
- IP Professional
- Industry Leading Data Capabilities
- Powerful AI technology
- Patent DNA Extraction
Browse by: Latest US Patents, China's latest patents, Technical Efficacy Thesaurus, Application Domain, Technology Topic, Popular Technical Reports.
© 2024 PatSnap. All rights reserved.Legal|Privacy policy|Modern Slavery Act Transparency Statement|Sitemap|About US| Contact US: help@patsnap.com