Deironing method for vanadium-bearing stone coal lixivium
A technology of leachate and vanadium stone, which is applied in the field of vanadium-containing stone coal extraction, can solve the problems of high iron content in leachate, waste of resources, waste of iron resources, etc., and achieve the effects of low iron content, reduced impact, and low vanadium loss rate
- Summary
- Abstract
- Description
- Claims
- Application Information
AI Technical Summary
Problems solved by technology
Method used
Examples
Embodiment 1
[0030] A method for removing iron from vanadium-bearing coal leachate. The specific steps of the iron removal method are:
[0031] Step 1. First crush the vanadium-containing stone coal to a particle size of less than 3mm, roast it at 750~800℃ for 1~1.3h, cool to room temperature, and then grind to a particle size of less than 0.074mm accounting for 65~80wt% to obtain Vanadium stone coal calcine.
[0032] Step 2: Mix the vanadium-containing coal calcine with water according to a liquid-solid ratio of 0.8 to 1.3 L / kg to obtain a vanadium-containing coal slurry.
[0033] Step 3: Adding the leaching agent to the vanadium-containing coal slurry, stirring at 80-88°C for 2 to 4 hours, and separating the solid and liquid to obtain the vanadium-containing coal leaching solution and the leaching residue.
[0034] The leaching agent is a mixture of soluble acids, soluble oxalate-containing substances and fluoride salts, and the ratio of the amount of hydrogen ion substances in the leaching age...
Embodiment 2
[0040] A method for removing iron from vanadium-bearing coal leachate. The specific steps of the iron removal method are:
[0041] Step 1. The vanadium-containing stone coal is crushed to a particle size of less than 3mm, roasted at 780~860℃ for 1.2~1.6h, cooled to room temperature, and then ground to a particle size of less than 0.074mm accounting for 65~80wt% to obtain Vanadium stone coal calcine.
[0042] Step 2: Mix the vanadium-containing coal calcine with water according to a liquid-solid ratio of 1.1 to 1.6 L / kg to obtain vanadium-containing coal slurry.
[0043] Step 3: Adding the leaching agent to the vanadium-containing coal slurry, stirring at 85-95°C for 3 to 5 hours, and separating the solid and liquid to obtain the vanadium-containing coal leaching solution and the leaching residue.
[0044] The leaching agent is a mixture of soluble acids, soluble oxalate-containing substances and fluoride salts, and the ratio of the amount of hydrogen ion substances in the leaching ag...
Embodiment 3
[0053] A method for removing iron from vanadium-bearing coal leachate. The specific steps of the iron removal method are:
[0054] Step 1. First crush the vanadium-containing stone coal to a particle size of less than 3mm, roast it at 850~900℃ for 1.5~2h, cool to room temperature, and then grind to a particle size of less than 0.074mm accounting for 65~80wt% to obtain vanadium Stone coal calcine.
[0055] Step 2: Mix the vanadium-containing coal calcine with water according to the liquid-solid ratio of 1.5-2L / kg to obtain vanadium-containing coal slurry.
[0056] Step 3: Adding the leaching agent to the vanadium-containing coal slurry, stirring at 90-100°C for 4.5-6 hours, and separating the solid and liquid to obtain the vanadium-containing coal leaching solution and the leaching residue.
[0057] The leaching agent is a mixture of soluble acids, soluble oxalate-containing substances and fluoride salts, and the ratio of the amount of hydrogen ion substances in the leaching agent to ...
PUM
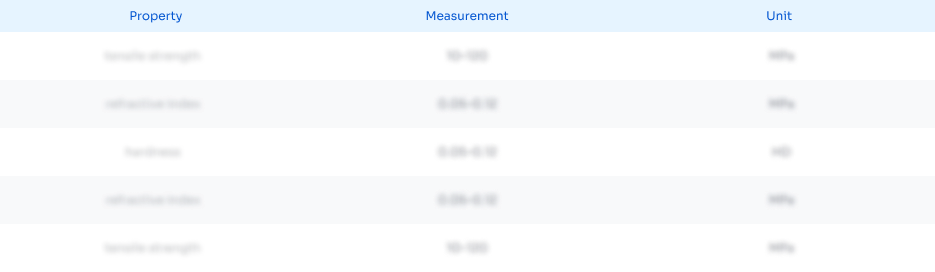
Abstract
Description
Claims
Application Information

- R&D
- Intellectual Property
- Life Sciences
- Materials
- Tech Scout
- Unparalleled Data Quality
- Higher Quality Content
- 60% Fewer Hallucinations
Browse by: Latest US Patents, China's latest patents, Technical Efficacy Thesaurus, Application Domain, Technology Topic, Popular Technical Reports.
© 2025 PatSnap. All rights reserved.Legal|Privacy policy|Modern Slavery Act Transparency Statement|Sitemap|About US| Contact US: help@patsnap.com