Method for manufacturing wheel mold
A manufacturing method and wheel technology, which is applied in the field of wheel molds, can solve problems such as poor mold hardness, improper structure control, and insufficient wheel precision, and achieve ideal anti-oxidation, ensure machinability, and refine austenite grains.
- Summary
- Abstract
- Description
- Claims
- Application Information
AI Technical Summary
Problems solved by technology
Method used
Examples
Embodiment 1
[0027] A method for manufacturing a wheel mold, the chemical composition and mass percentage of the wheel mold material are: 3.5% carbon, 1.9% silicon, 1% nickel, <0.8% copper, 0.5% manganese, 0.35% molybdenum, 0.35% chromium, <0.06% titanium, <0.06% zirconium, <0.01% sulfur, <0.01% phosphorus, <0.01% rhenium, <0.01% scandium, and the rest is iron;
[0028] Described preparation method comprises the following steps:
[0029] Step (1): Dosing according to the chemical composition of the materials designed above, the raw materials are pig iron, ferrosilicon, electrolytic nickel, electrolytic copper, ferromanganese, ferromolybdenum, ferrochromium, micron titanium oxide, nano zirconium carbide, rhenium oxide and scandium oxide ;
[0030] Step (2): Melting all raw materials in an intermediate frequency induction furnace at a melting temperature of 1480°C to obtain castings;
[0031] Step (3): Surface heat treatment is carried out on the prepared casting at a heating temperature o...
Embodiment 2
[0034] A method for manufacturing a wheel mold, the chemical composition and mass percentage of the wheel mold material are: 3.65% carbon, 1.95% silicon, 1.2% nickel, <9% copper, 0.6% manganese, 0.4% molybdenum, 0.4% chromium, <0.07% titanium, <0.07% zirconium, <0.015% sulfur, <0.015% phosphorus, <0.015% rhenium, <0.015% scandium, and the rest is iron;
[0035] Described preparation method comprises the following steps:
[0036] Step (1): Dosing according to the chemical composition of the materials designed above, the raw materials are pig iron, ferrosilicon, electrolytic nickel, electrolytic copper, ferromanganese, ferromolybdenum, ferrochromium, micron titanium oxide, nano zirconium carbide, rhenium oxide and scandium oxide ;
[0037] Step (2): Melting all raw materials in an intermediate frequency induction furnace at a melting temperature of 1520°C to obtain castings;
[0038] Step (3): Surface heat treatment is carried out on the prepared casting at a heating temperatu...
Embodiment 3
[0041] A method for manufacturing a wheel mold, the chemical composition and mass percentage of the wheel mold material are: 3.8% carbon, 2.0% silicon, 1.3% nickel, <1% copper, 0.7% manganese, 0.5% molybdenum, 0.5% chromium, <0.08% titanium, <0.08% zirconium, <0.02% sulfur, <0.02% phosphorus, <0.02% rhenium, <0.02% scandium, and the rest is iron;
[0042] Described preparation method comprises the following steps:
[0043] Step (1): Dosing according to the chemical composition of the materials designed above, the raw materials are pig iron, ferrosilicon, electrolytic nickel, electrolytic copper, ferromanganese, ferromolybdenum, ferrochromium, micron titanium oxide, nano zirconium carbide, rhenium oxide and scandium oxide ;
[0044] Step (2): Melting all raw materials in an intermediate frequency induction furnace at a melting temperature of 1560°C to obtain castings;
[0045] Step (3): Surface heat treatment is carried out on the prepared casting at a heating temperature of ...
PUM
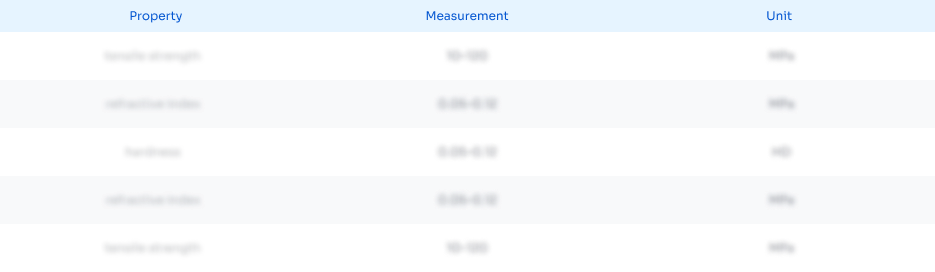
Abstract
Description
Claims
Application Information

- Generate Ideas
- Intellectual Property
- Life Sciences
- Materials
- Tech Scout
- Unparalleled Data Quality
- Higher Quality Content
- 60% Fewer Hallucinations
Browse by: Latest US Patents, China's latest patents, Technical Efficacy Thesaurus, Application Domain, Technology Topic, Popular Technical Reports.
© 2025 PatSnap. All rights reserved.Legal|Privacy policy|Modern Slavery Act Transparency Statement|Sitemap|About US| Contact US: help@patsnap.com