Process for production of methacrylic acid esters
A technology of methacrylate and methacrylic acid, applied in the preparation of carboxylate, carboxylate/lactone, and carboxyamide, etc., can solve the problem of no research on conversion and limited applicability of MMA residue recovery yield , limited capacity, etc.
- Summary
- Abstract
- Description
- Claims
- Application Information
AI Technical Summary
Problems solved by technology
Method used
Image
Examples
specific Embodiment
[0075] The following examples are provided to illustrate the invention and should not be construed as limiting its scope.
comparative test 1-10
[0076] Comparative Test 1 -10%Cs 2 O / SiO 2 Catalyst preparation (not an example of the invention)
[0077] 2.72 g of cesium acetate was dissolved in 75 g of deionized water to prepare an aqueous cesium acetate solution. Then add this aqueous solution to the silica gel ( Grade 636 silica gel, commercially available from Aldrich) in a round bottom flask. The mixture was stirred for 10 minutes, then rotovaped under vacuum to remove water. The powder was further dried in a vacuum oven at room temperature overnight, then dried at 120°C for 4 hours and calcined at 450°C for 5 hours in an air atmosphere in a box furnace. The calcined powder contained a nominal 10 wt% Cs 2 O and are named 10% Cs 2 O / SiO 2 . It was then pressed and sieved into 14-20 mesh particles, and then loaded into a fixed-bed reactor for catalytic performance evaluation.
comparative test 2-10
[0078] Comparative test 2 -10%Cs 2 O / Bi / SiO 2 (Bi / Si=0.0014) preparation of catalyst (not an embodiment of the invention)
[0079] Preparation containing 0.174gBi(NO 3 ) 3 ·5H 2 O and 50 g deionized water in water. Then 0.62 g of 5% by weight aqueous nitric acid was added to the mixture to help dissolve the bismuth nitrate salt. The mixture was stirred at room temperature, and then 2.27 g of cesium acetate were added. The solution was transferred to a solution containing 15 g of silica gel ( grade 636, commercially available from Aldrich Company) in a round bottom flask. The mixture was stirred for 10 min, then rotovaped under vacuum at 50 °C to remove water. The resulting powder was dried at 120° C. for 5 hours and calcined at 450° C. for 5 hours in an air atmosphere in a box furnace. It is then pressed and sieved into 14-20 mesh particles and named 10% Cs 2 O / Bi / SiO 2 (Bi / Si=0.0014), which has a nominal atomic ratio of Bi / Si of 0.0014.
PUM
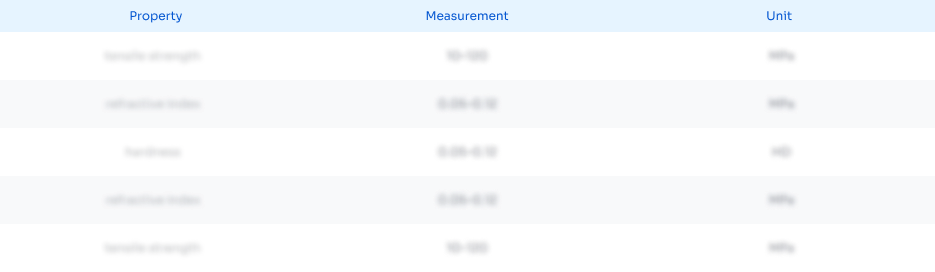
Abstract
Description
Claims
Application Information

- Generate Ideas
- Intellectual Property
- Life Sciences
- Materials
- Tech Scout
- Unparalleled Data Quality
- Higher Quality Content
- 60% Fewer Hallucinations
Browse by: Latest US Patents, China's latest patents, Technical Efficacy Thesaurus, Application Domain, Technology Topic, Popular Technical Reports.
© 2025 PatSnap. All rights reserved.Legal|Privacy policy|Modern Slavery Act Transparency Statement|Sitemap|About US| Contact US: help@patsnap.com