mo of a nickel base alloy as the binder phase 2 nib 2 Base cermet and preparation method thereof
A nickel-based alloy and metal-based technology, applied in the field of Mo2NiB2-based cermet materials, can solve the problems of large shrinkage, uneven shrinkage, and easy distortion of the billet, and achieve the effects of good toughness, less internal defects, and high strength
- Summary
- Abstract
- Description
- Claims
- Application Information
AI Technical Summary
Problems solved by technology
Method used
Image
Examples
Embodiment 1
[0040] (1) Mix 1945g MoB powder, 955g NiB powder, 1404g Mo powder and 1995g Ni powder with 100g glucose, 30g polymethyl methacrylate, 20g polyvinyl butyral and 1500g absolute ethanol, and ball mill for 10h Obtain a slurry with a solid content of 45 vol%;
[0041] Among them, the synthesis method of MoB is: mixing Mo powder and B powder at a molar ratio of 1:1, then ball milling for 2 hours, and then synthesizing in a self-propagating synthesizer in an argon atmosphere with a synthesis pressure of 0.1 MPa; the synthesis of NiB The method is: Ni powder and B powder are mixed according to a molar ratio of 1:1 and then ball milled for 2 hours, and then synthesized in a self-propagating synthesizer in an argon atmosphere at a synthesis pressure of 0.1MPa;
[0042] (2) The slurry is made by a pressure spray drying granulator, and the conditions are that the spray pressure is 0.6MPa and the inlet temperature of the drying tower is 180°C;
[0043] (3) Treat the powder obtained by spray dryi...
Embodiment 2
[0047] (1) Mix 2918g of MoB powder, 1909g of NiB powder, 100g of B powder, 3882g of Mo powder and 4891g of Ni powder with 200g of glucose, 100g of polymethyl methacrylate, 100g of polyvinyl butyral and 2500g of absolute ethanol. , Vibrating mill for 30 hours to obtain a slurry with a solid content of 60 vol%;
[0048] Among them, the synthesis method of MoB is: mixing Mo powder and B powder at a molar ratio of 1.1:1 and then ball milling for 2 hours, and then synthesizing in a self-propagating synthesizer in an argon atmosphere with a synthesis pressure of 5MPa; the synthesis method of NiB It is: Ni powder and B powder are mixed according to a molar ratio of 1.2:1 and then ball milled for 2h, and then synthesized in a self-propagating synthesizer in an argon atmosphere, the synthesis pressure is 5MPa;
[0049] (2) The slurry is made by a pressure spray drying granulator, and the conditions are that the spray pressure is 1.5MPa and the inlet temperature of the drying tower is 220°C;...
Embodiment 3
[0054] (1) Mix 1945g MoB powder, 1909g NiB powder, 100gB powder, 2255gMo powder and 1391g Ni powder, and mix with 150g glucose, 50g polymethyl methacrylate, 50g polyvinyl butyral and 2000g absolute ethanol , Vibrating mill for 20 hours to obtain a slurry with a solid content of 50vol%;
[0055] Among them, the synthesis method of MoB is: Mo powder and B powder are mixed according to a molar ratio of 1.1:1 and then ball milled for 2 hours, and then synthesized in a self-propagating synthesizer in an argon atmosphere with a synthesis pressure of 3MPa; the synthesis method of NiB It is: Ni powder and B powder are mixed according to a molar ratio of 1.1:1 and then ball milled for 2h, and then synthesized in a self-propagating synthesizer in an argon atmosphere, the synthesis pressure is 4MPa;
[0056] (2) The slurry is made into powder with a pressure spray drying granulator, and the conditions are that the spray pressure is 1MPa and the inlet temperature of the drying tower is 200°C; ...
PUM
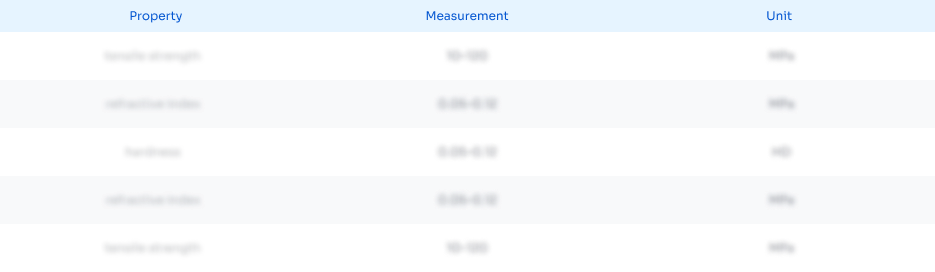
Abstract
Description
Claims
Application Information

- R&D
- Intellectual Property
- Life Sciences
- Materials
- Tech Scout
- Unparalleled Data Quality
- Higher Quality Content
- 60% Fewer Hallucinations
Browse by: Latest US Patents, China's latest patents, Technical Efficacy Thesaurus, Application Domain, Technology Topic, Popular Technical Reports.
© 2025 PatSnap. All rights reserved.Legal|Privacy policy|Modern Slavery Act Transparency Statement|Sitemap|About US| Contact US: help@patsnap.com