Macromolecule heat conduction and dissipation blended composite material and automatic preparation method
A composite material and polymer technology, which is applied in the fields of polymer thermal conduction and heat dissipation blended composite materials and automatic preparation, can solve the problems of ineffective improvement of thermal conductivity, influence of continuity of production, uneven dispersion of thermally conductive fillers, etc., and saves energy. The effect of manpower, uniform dispersion and promotion, shortening production cycle
- Summary
- Abstract
- Description
- Claims
- Application Information
AI Technical Summary
Problems solved by technology
Method used
Examples
preparation example Construction
[0027] An automatic preparation method for polymer thermal conduction and heat-conducting blended composite materials, comprising the steps of:
[0028] 1) First use powder surface activation treatment agent to surface-treat the thermally conductive filler in a high-speed mixer for 20 minutes;
[0029] 2) Then enter another high-speed mixer through an automatic conveying device, and mix with other raw materials evenly;
[0030] 3) Automatically convey the mixture obtained in the previous step to the internal mixer for internal mixing and kneading for 15 minutes;
[0031] 4) The obtained mixture can be directly extruded into a twin-screw extruder for granulation.
Embodiment 1
[0034]First, add 40 parts of alumina and 5 parts of aluminum nitride into the high-speed mixer, then add 0.6 parts of silane coupling agent KH-550, and perform surface treatment on the heat-conducting powder for 20 minutes by high-speed stirring, and the obtained pretreated powder Send in the internal mixer that 53.1 parts of PBT resins, 0.4 parts of antioxidant 1010, 0.4 parts of antioxidant 168, 0.5 parts of TAF lubricant and 5 parts of SBS-g-MAH toughening agent are housed through automatic conveying device, in Internal mixing and kneading were carried out at 240° C. for 15 minutes, and then the obtained mixture was automatically conveyed to a twin-screw extruder for extrusion and granulation.
[0035] The raw materials in this example are all calculated in parts by mass, and the total mass parts of the feed is 100 parts, the same below.
Embodiment 2
[0037] First, add 40 parts of alumina, 6 parts of aluminum nitride and 2.5 parts of boron nitride into the high-speed mixer, then add 0.7 parts of silane coupling agent KH-550, and conduct surface treatment on the heat-conducting powder for 20 minutes by high-speed stirring , the obtained pretreatment powder is sent to the container with 40.2 parts of PA6 resin, 0.4 part of antioxidant 1010, 0.6 part of antioxidant 168, 0.2 part of PETS lubricant, 0.4 part of PE wax and 9 parts of EPDM-g through the automatic conveying device - In the internal mixer of MAH toughening agent, perform internal mixing and kneading at 220° C. for 15 minutes, and then automatically transfer the obtained mixture to a twin-screw extruder for extrusion and granulation.
PUM
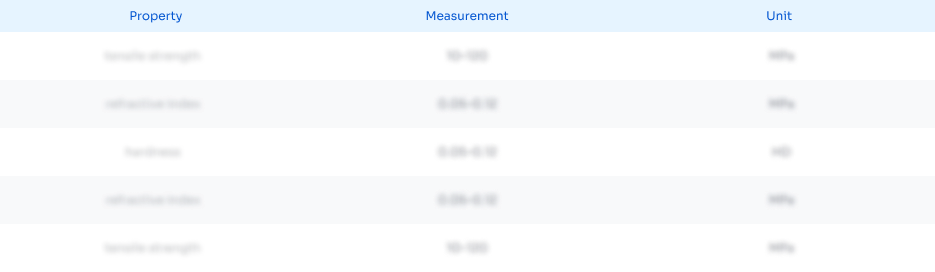
Abstract
Description
Claims
Application Information

- R&D
- Intellectual Property
- Life Sciences
- Materials
- Tech Scout
- Unparalleled Data Quality
- Higher Quality Content
- 60% Fewer Hallucinations
Browse by: Latest US Patents, China's latest patents, Technical Efficacy Thesaurus, Application Domain, Technology Topic, Popular Technical Reports.
© 2025 PatSnap. All rights reserved.Legal|Privacy policy|Modern Slavery Act Transparency Statement|Sitemap|About US| Contact US: help@patsnap.com