Pulverized coal melt separation and recovery method for low-grade iron resources
A recycling method and low-grade technology, applied in fluidized bed furnaces and other directions, can solve the problems of low thermal conductivity of slag layer, no thermal conductivity of coke layer, and high energy consumption
- Summary
- Abstract
- Description
- Claims
- Application Information
AI Technical Summary
Problems solved by technology
Method used
Image
Examples
Embodiment 1
[0018] The water-quenched copper slag in Yunnan has a TFe content of 40.57% and a natural alkalinity of 0.15. Grinding the copper slag to a powder with a particle size of less than 0.125 mm, mixing it with lime and coal powder to prepare carbon-containing pellets with R=1. The dried pellets were placed in a corundum crucible with a grate on the bottom. The pellets are first reduced to metallized pellets with a metallization rate of 95% at a temperature of 1280°C, and then melted at 1450°C. The hot air rising from the bottom convects the pellets through the small holes of the grate, and the pellets are melted It drips through the small holes into the crucible below and forms a layer of slag and iron. In the melting stage, the amount of air introduced into the bottom of the tube furnace is controlled according to the carbon-to-oxygen ratio, the residual carbon content of the metallized pellets is controlled at about 10%, and the O / C ratio is controlled at 1.5, 1.0 and 0.8, resp...
Embodiment 2
[0020] Mix Yunnan water-quenched copper slag into flux and coal powder to prepare carbon-containing pellets with R=1, and reduce them to metallized pellets with metallization rates of 78%, 85%, and 95% at 1280°C, and then at 1450°C The melting is carried out in the temperature range of ℃. When the C / O ratio in the melting stage is controlled at 1.0, the yields of granular iron obtained by melting are 93%, 91% and 92%, respectively. The degree of reduction of metallized pellets has little effect on the melting stage, but considering To the influence of the melting zone of the melting furnace, the metallization rate should be controlled above 85%.
[0021] Case 3
[0022] Jiangxi copper slag has a TFe content of 42.94% and a natural alkalinity of 0.07; Jinchang low-nickel slag has a TFe content of 40.78% and a natural alkalinity of 0.05; Jinchang high-nickel slag has a TFe content of 32.97% and a natural alkalinity of 0.17. The slags above are ground and mixed with lime and c...
PUM
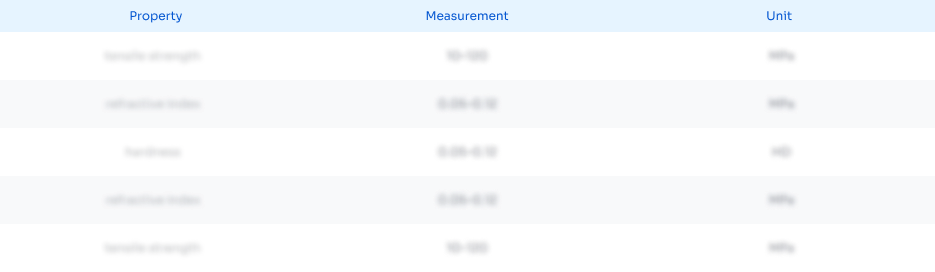
Abstract
Description
Claims
Application Information

- R&D
- Intellectual Property
- Life Sciences
- Materials
- Tech Scout
- Unparalleled Data Quality
- Higher Quality Content
- 60% Fewer Hallucinations
Browse by: Latest US Patents, China's latest patents, Technical Efficacy Thesaurus, Application Domain, Technology Topic, Popular Technical Reports.
© 2025 PatSnap. All rights reserved.Legal|Privacy policy|Modern Slavery Act Transparency Statement|Sitemap|About US| Contact US: help@patsnap.com