Surface coating cutting tool and manufacturing method thereof
A surface coating and cutting tool technology, applied in chemical instruments and methods, liquid chemical plating, metal material coating processes, etc., can solve the problems of easy peeling, low crystallinity of titanium carbide layer, layer peeling, etc. Excellent surface smoothness, excellent cutting performance, the effect of improving the bonding force
- Summary
- Abstract
- Description
- Claims
- Application Information
AI Technical Summary
Problems solved by technology
Method used
Image
Examples
preparation example Construction
[0062] Preparation of alumina sol:
[0063] First, alcohols (e.g., ethanol, 1-butanol) and water are added as solvents, and acids (e.g., hydrochloric acid, nitric acid) are added to aluminum alkoxides (e.g., aluminum sec-butoxide (ASB), aluminum propoxide) As a catalyst, sodium laurate (C 11 h 23 COONa) or sodium dodecylbenzenesulfonate (DBSN) as a surfactant, after stirring in the temperature range below -10 to 20°C, the same temperature range as the stirring, such as stirring and aging treatment The aging treatment is carried out at a temperature range of -10 to 20° C. or lower over a long period of 12 hours or more in total to form an alumina sol. In addition, the alumina sol used in the present invention preferably uses dimethylformamide (DMF) and acetylacetone (AcAc) as a chelating agent. This is for the purpose of suppressing excessively accelerated crystallization. If a chelating agent having an effect of suppressing excessively accelerated crystallization is not use...
Embodiment 1
[0078] Next, the present invention will be described more specifically by way of examples.
[0079] (a1) As raw material powders, fine particle WC powder with an average particle diameter of 0.8 μm, medium-grained WC powder with an average particle diameter of 2 to 3 μm, and TiCN powder, ZrC powder, and TaC powder with an average particle diameter of 1 to 3 μm are prepared. powder, NbC powder, Cr 3 C 2powder, VC powder, and Co powder. These raw material powders were mixed into the specified compounding composition shown in Table 1, and paraffin wax was further added and ball milled in acetone for 24 hours. After drying under reduced pressure, they were stamped and formed into specified shape of the compact, and the compact is vacuum sintered in a vacuum of 5 Pa at a temperature of 1400°C for 1 hour. After sintering, the cutting edge is subjected to R: 0.05mm edge grinding , thereby manufacturing WC-based cemented carbide tool substrates A, B, C, D, E, E1, E2, E3, E4, E5 (ref...
Embodiment 2
[0139] As raw material powders, TiCN (TiC / TiN=50 / 50 by mass ratio) powder, Mo 2 C powder, NbC powder, TaC powder, WC powder, Co powder, and Ni powder were blended into the prescribed compounding composition shown in Table 9, and wet-mixed with a ball mill for 24 hours. After drying, press molding under a pressure of 98MPa To make a compact, the compact was sintered in a nitrogen atmosphere of 1.3kPa at a temperature of 1540°C for 1 hour. After sintering, the cutting edge was subjected to R: 0.07mm edge grinding. Thus, TiCN-based cermet tool bases F, G, H, I, J, J1, J2, J3, J4, J5 (referred to as tool bases F to J5) having insert shapes according to ISO standard CNMG120412 were produced. However, for the tool base J2, in a nitrogen atmosphere of 1.3 kPa, the temperature increase rate was set to 2 °C / min, and after the temperature was raised from room temperature to 1540 °C and kept for 30 minutes, it was set to a vacuum of 13 Pa and kept at 1540 °C for 30 minutes. After 10 min...
PUM
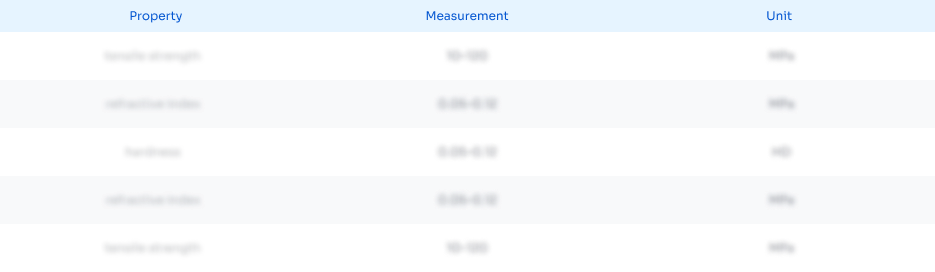
Abstract
Description
Claims
Application Information

- R&D Engineer
- R&D Manager
- IP Professional
- Industry Leading Data Capabilities
- Powerful AI technology
- Patent DNA Extraction
Browse by: Latest US Patents, China's latest patents, Technical Efficacy Thesaurus, Application Domain, Technology Topic, Popular Technical Reports.
© 2024 PatSnap. All rights reserved.Legal|Privacy policy|Modern Slavery Act Transparency Statement|Sitemap|About US| Contact US: help@patsnap.com